BD Engineering digitaliza un Toyota Supra completo con el Artec Leo para crear modos de derrape personalizados
Desafío: Desmontar todo un automóvil deportivo Toyota Supra y digitalizar sus partes para crear modelos 3D que se puedan personalizar y convertir en modificaciones en el mercado de repuestos.
Solución: Artec Leo, Artec Eva, Artec Studio.
Resultado: Un modelo Supra tan detallado que está configurado para ser utilizado como un entorno de simulación dinámica para probar nuevas geometrías de suspensión, así como un diferencial y un freno de mano hidráulico rediseñado para aplicaciones de derrape.
¿Por qué Artec 3D? Medir manualmente cada pieza habría hecho que la ingeniería inversa del Supra fuera una tarea poco práctica. Con el increíblemente rápido e inalámbrico Artec Leo, BD Engineering ha sido capaz de digitalizar fácilmente el automóvil en cuestión de horas y utilizar los datos resultantes para desarrollar una base de diseños de piezas para derrape nunca antes vistos en Artec Studio.
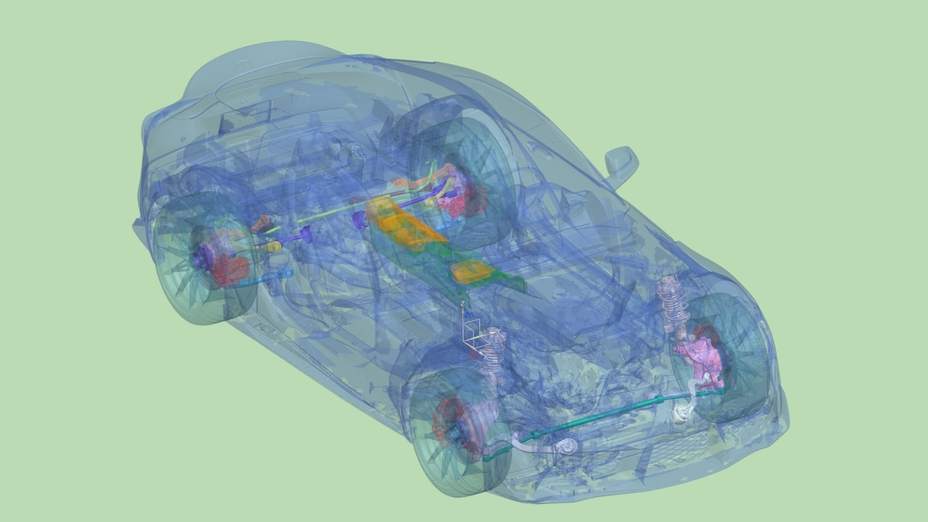
El Toyota Supra de ingeniería inversa de BD Engineering y las modificaciones planificadas. Imagen cortesía de BD Engineering.
¿Alguna vez has soñado con armar tu auto perfecto? Muchos lo han hecho, como muestra la floreciente industria de piezas de repuesto automotriz de $16 mil millones de EE. UU. Pero, ¿qué tan fácil es lograr esto en realidad?
Uno de los principales desafíos de la personalización es garantizar que las modificaciones encajen a la perfección con el chasis o la carrocería existente de un automóvil. Como la mayoría de los fabricantes de equipos originales no están interesados en compartir datos de diseño valiosos con los desarrolladores de piezas del mercado de repuestos, esto crea un problema importante: ¿cómo saber lo que se esconde debajo del capó al modificar vehículos?
Afortunadamente para los ingenieros (y entusiastas de los automóviles), las tecnologías de ingeniería inversa avanzan a buen ritmo y ahora permiten digitalizar las piezas en segundos. Algunas empresas del mercado de accesorios se han apegado a sus pistolas de ruedas, utilizando tallado o moldura para la personalización, pero no BD Engineering, que continúa superando los límites en la industria automotriz, y más allá, con la ayuda del escaneo de Artec 3D.
'Cerrando el círculo' en BD Engineering
Hace ocho años, el ingeniero Adam Bao se propuso crear modificaciones de automóviles en su universidad local. Sin embargo, lo que comenzó como un proyecto apasionante se convirtió rápidamente en lo que ahora es Illumaesthetic, un próspero negocio que ha personalizado autos exhibidos en las principales ferias comerciales automotrices como SEMA y Tokyo Auto Salon.
A su vez, estas historias de éxito han llevado a una demanda de la clientela industrial, médica y de defensa, lo que ha llevado a Bao y al cofundador Nikita Rushmanov a crear otra empresa: BD Engineering. Equipada con escaneo 3D y maquinaria de fabricación avanzada, la empresa ayuda a los clientes con todo, desde la creación rápida de prototipos e inspección hasta la producción bajo demanda.
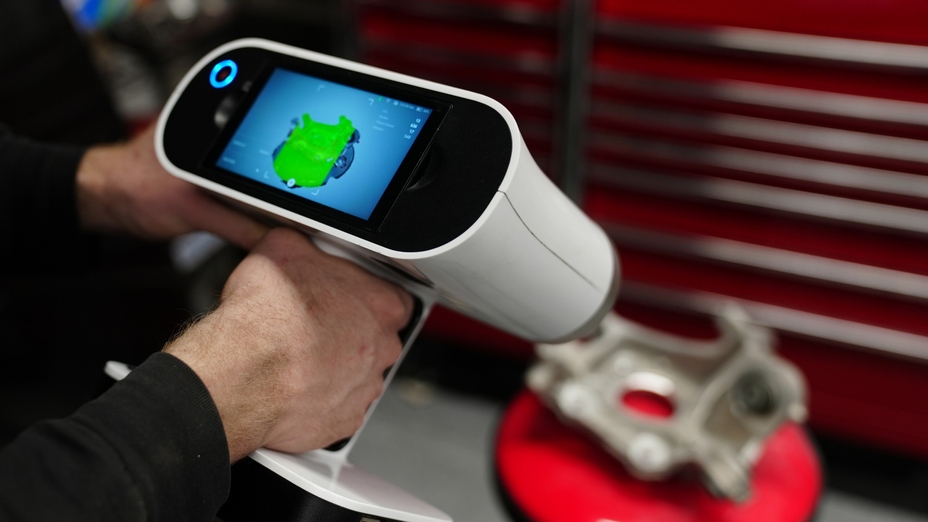
Digitalización de una pieza de suspensión con la pantalla incorporada del Artec Leo. Imagen cortesía de BD Engineering.
Pero, ¿cómo terminó BD Engineering utilizando el escaneo 3D en primer lugar? En los primeros días, Bao jugaba con la fotogrametría de los teléfonos inteligentes, digitalizando objetos y convirtiéndolos en archivos de diseño listos para editar. Al darse cuenta de que la tecnología no era lo suficientemente rápida ni precisa, buscó un nuevo enfoque, basado en un escáner 3D rápido de 0,1 mm de precisión: Artec Eva.
A medida que crecía la demanda del mercado de repuestos, BD Engineering se puso en contacto con Indicate Technologies. El socio certificado por Artec Gold aconsejó a la empresa que se actualizara a Artec Leo, un dispositivo inalámbrico impulsado por IA que permitió que sus dos empresas florecieran simultáneamente. Esto, a pesar de que las instalaciones están a cientos de kilómetros de distancia, en Newark y Los Ángeles respectivamente.
Más tarde, Rushmanov se mudó al norte del estado, pero la pareja descubrió que inicialmente podían compartir al Leo de un lado a otro de California, con su naturaleza todo en uno, completa con una pantalla incorporada, lo que hace que sea más fácil que nunca llevar su trabajo a la carretera. Desde entonces, el dúo emprendedor no sólo ha integrado el escaneo 3D en su flujo de trabajo más amplio, sino que ha ideado una forma bastante única de hacerlo.
«En el sector de la automoción, veo a mucha gente escaneando sólo la mitad del coche», explicó Bao. «Esa no es una muy buena idea. Cuando escanee en el sentido de las agujas del reloj, notarás que el lugar donde comienza y termina puede estar a 6-12 pulgadas de distancia. A menos que tenga un bucle circular completo, hay mucha propagación de errores. Entonces dijimos: “Mejor, vamos a escanear todo el coche”. Yo lo llamo cerrar el círculo».
«Con el Artec Leo, la diferencia en el tiempo que se tarda en escanear la parte delantera en comparación con todo el automóvil es tan insignificante, que simplemente pensamos “¿por qué no escanear todo?”»
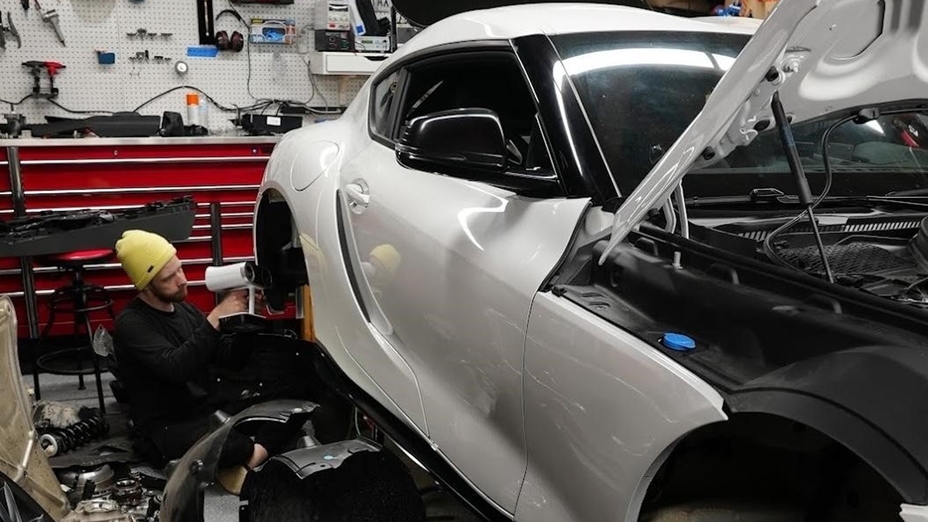
Nikita Rushmanov, cofundador de BD Engineering, digitalizando un Supra con el Artec Leo. Imagen cortesía de BD Engineering.
A la deriva hacia nuevas verticales
No satisfechos con su trabajo en Illumaesthetic, personalizando indicadores y luces traseras para empresas como General Motors y BMW, en un momento incluso mejorando el parachoques de un icónico Subaru, la pareja ahora se ha fijado un objetivo más elevado: la ingeniería inversa de vehículos completos.
En uno de los primeros escaneos exteriores de un vehículo completo, Bao descubrió que podía usar el Artec Eva para digitalizar un Honda S2000 completo. Aunque el proyecto sólo le llevó dos horas, dice que poner un mínimo de cinta adhesiva en el coche le ralentizó, y con el Leo de 35 millones de pt/s, podría haberlo hecho mucho más rápido.
«Obviamente, estaba motivado para poner la menor cantidad posible de marcadores en el S2000», dijo Bao. «Así que empecé con lo que pensaba que necesitaba, luego me di cuenta de que necesitaba más, y estaba constantemente yendo y viniendo. Con el Leo es tan rápido que podrías pasar 15 minutos preparando los faros, los espejos, las ventanas, cualquier moldura de plástico negro y otros 15 minutos escaneando».
Como parte del último proyecto de digitalización de BD Engineering, Rushmanov ha realizado la ingeniería inversa de su coche de trabajo: un GR Toyota Supra 2023. Al desmontar el automóvil y escanear cada pieza de la suspensión, así como su bastidor auxiliar, ha podido crear una modificación extensa, con un freno de mano hidráulico diseñado para derrapar.
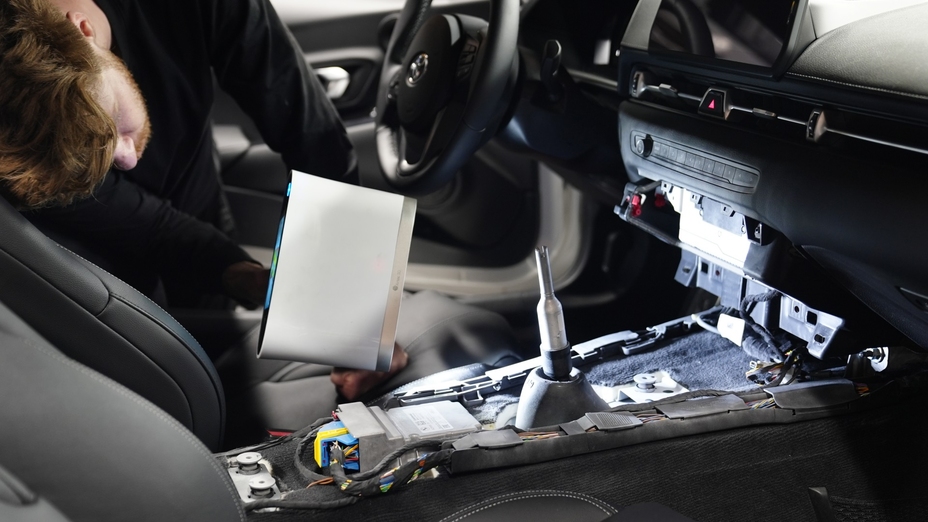
Rushmanov usando un Artec Leo para escanear en 3D el freno de mano de un Toyota Supra. Imagen cortesía de BD Engineering.
Mientras que el rápido y maniobrable Leo garantizó que esto fuera rápido y fácil, Rushmanov dice que el conjunto de herramientas de edición de Artec Studio demostró ser igualmente útil para agilizar la alineación de la malla, superar las limitaciones de diseño y eliminar polígonos para reducir el tamaño del archivo de exportación.
«Artec Studio puede recorrer un largo camino, de hecho disfruto mucho usándolo», agregó Rushmanov. «El enfoque de Artec Studio para la ingeniería inversa es bastante innovador, debido a la forma en que le permite resolver todas sus restricciones de diseño a la vez, y luego reacondicionarlo. Ahorra mucho tiempo».
«Hemos realizado ingeniería inversa de todo el coche, con el objetivo de establecer un entorno de simulación dinámico que optimice numéricamente el coste de las nuevas piezas de suspensión».
Establecimiento de una configuración de «escaneo-a-fábrica»
En medio de la creciente demanda de piezas digitalizadas e impresas en 3D, BD Engineering ha comenzado a trabajar cada vez más con clientes fuera de la base automotriz tradicional de Illumaesthetic. Según Bao, lo ha conseguido yendo más allá de ofrecer la impresión 3D como «servicio intermediario».
Dice que, típicamente, los fabricantes de equipos originales pedían maquetas impresas en 3D para «comercializar vehículos, no a través de renders, sino de fotos de piezas físicas» para su promoción antes del lanzamiento. Si bien Illumaesthetic todavía recibe estos clientes, BD Engineering ha comenzado a usar la tecnología en otros lugares, en un caso para crear un fuselaje, que se ha convertido en un molde para fabricar drones de prácticas de tiro militar.
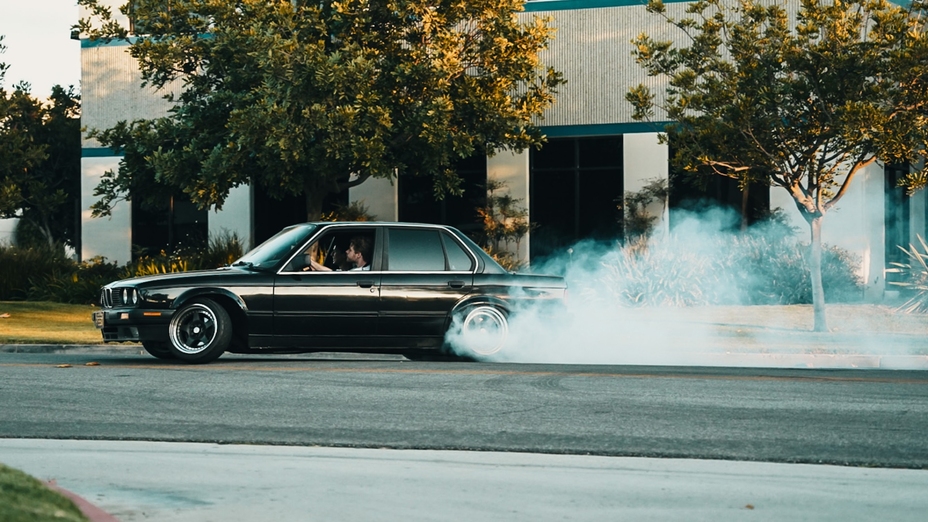
Rushmanov mostrando sus habilidades de derrape en un BMW clásico. Imagen cortesía de BD Engineering.
En cuanto a sus modificaciones del Supra, Rushmanov planea fabricarlos y venderlos a drifteros de todo el mundo. Mientras tanto, dice que su empresa tiene la intención de establecer una «configuración de escaneo-a-fábrica», en la que los clientes puedan dejar las cosas para su digitalización y tener piezas visuales o de rendimiento listas para la producción en el plazo de un mes.
«Constantemente nos entregan cosas para escanearlas en 3D, porque los clientes ven que lo que hacemos deja a todos los demás fuera de la liga. No nos limitamos a escanear lo que se necesita, sino que llevamos las cosas a otro nivel».
Escáneres detrás de la historia
Prueba los escáneres 3D líderes en el mundo.