Curtis Cabs bringt mit Artec Leo sein Reverse Engineering auf Vordermann
Herausforderung: Ein branchenführender Hersteller von kundenspezifischen Kabinengehäusen musste seine Abläufe beim Reverse Engineering beschleunigen, um Termine einzuhalten und mit der steigenden Marktnachfrage Schritt halten zu können.
Lösung: Artec Leo, Artec Studio, Geomagic for SOLIDWORKS
Ergebnis: Das Design- und Konstruktionsteam des Unternehmens konnte die Scangeschwindigkeit für ein Fahrzeug von 4-8 Stunden auf unter eine Stunde reduzieren. Und die Scanverarbeitung, welche früher 2-3 Tage pro Fahrzeug in Anspruch nahm, ist jetzt in weniger als einer Stunde abgeschlossen.
Warum Artec? Die Möglichkeit, ohne störende Kabel oder Laptops zu scannen, bedeutet auch, dass Leo problemlos überall dorthin gebracht werden kann, wo sie hinwollen. Bei jedem Durchlauf des Scanners werden pro Sekunde Millionen von Datenpunkten erfasst, wobei der Scan in Echtzeit auf dem hinten angebrachten Touchscreen von Leo angezeigt wird.
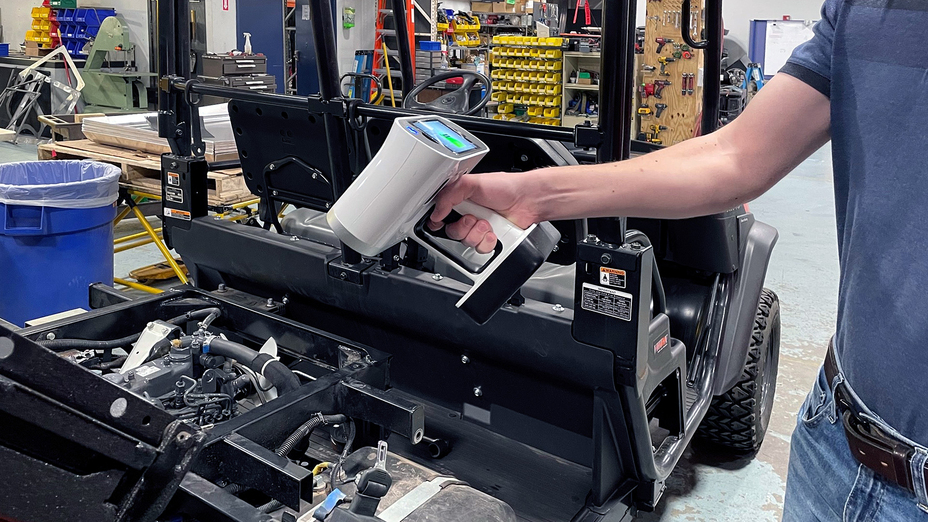
Bild mit freundlicher Genehmigung von Curtis Cabs.
Am Anfang war nur Staunen. Denn als die Konstrukteure von Curtis Industries erstmals ihren neuen 3D-Scanner des Typs Artec Leo in die Hand nahmen, hätten sie niemals erwartet, dass sie mit diesem Gerät ihren Scan-to-CAD-Workflow bei nur einem Projekt um ganze 38 Stunden verkürzen könnten. Doch so sollte es geschehen.
Und schon bald entdeckten sie, dass die Vorteile von Leo weit über ein paar Dutzend Stunden Zeitersparnis bei jedem einzelnen Scanauftrag hinausgehen.
Seit 1968 ist das in Massachusetts ansässige Unternehmen innovativ tätig und führend in der Entwicklung und Herstellung von kundenspezifischen Kabinengehäusen für Traktoren, UTVs und Golfwagen, Schnee- und Eisbeseitigungsgeräte und noch vieles mehr.
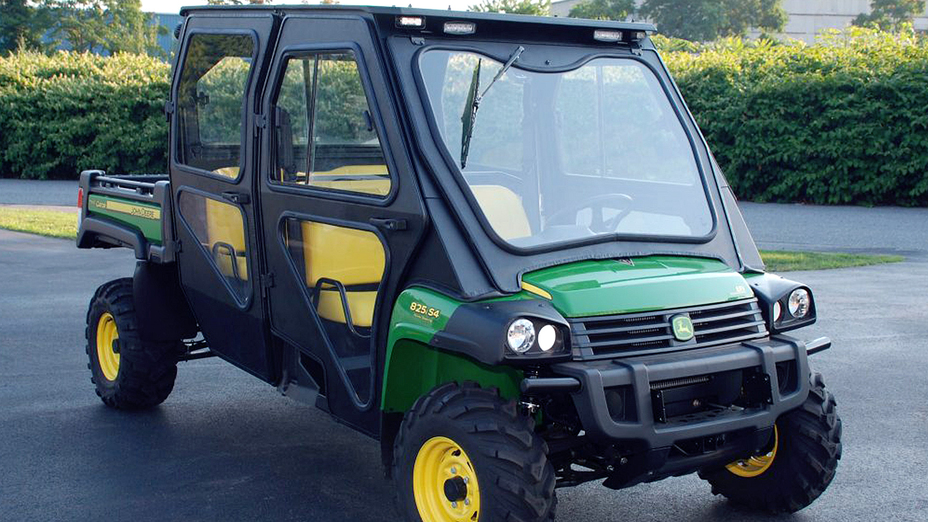
Eine Kabinenüberdachung von Curtis Cabs für einen John Deere Gator XUV. Bild mit freundlicher Genehmigung von Curtis Cabs.
Unterstützung der höchsten Qualitätsstandards
Was die Produktlinien von Curtis Industries angeht, so ist hier die perfekte Passform das A und O. In den Worten von Steve Smith, Design Engineering Manager beim Unternehmen: „Unsere kundenspezifischen Kabinen werden so gefertigt, dass sie zu den Fahrzeugen passen, so als wären sie eine natürliche Erweiterung, die von Anfang mit verbaut wurde.“
„Jede einzelne Dichtung, jede Halterung, jedes Montageloch, jedes Fenster und jede Tür muss ausnahmslos an der richtigen Stelle und mit den richtigen Maßen angebracht sein.“
„Aus diesem Grund“, so fährt Smith fort, „bieten unsere Kabinen den Fahrern über Jahre hinweg ein Maximum an Komfort und Schutz. Um dies zu erreichen, muss jede einzelne Dichtung, Halterung, Montageöffnung, jedes Fenster und jede Tür ausnahmslos an der richtigen Stelle und in den richtigen Maßen angebracht sein.“
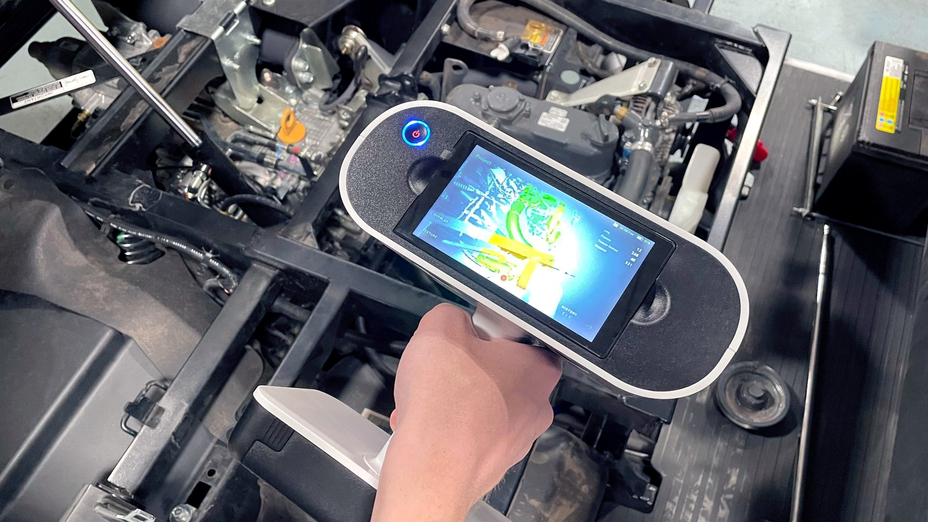
3D-Scannen des Motorraums eines Nutzfahrzeugs von Kubota mit Artec Leo. Bild mit freundlicher Genehmigung von Curtis Cabs.
Curtis Industries genießt in den USA überregional einen tadellosen Ruf. Um die ständig steigende Marktnachfrage zu befriedigen und die eigenen strengen Fristen einzuhalten, ergründen Curtis Industries und sein Konstruktions-Team unermüdlich neue Möglichkeiten zur Verbesserung ihrer Produkte und Arbeitsabläufe, darunter auch einen der wichtigsten: ihren Ablauf beim Reverse Engineering.
Der Ablauf beim Reverse Engineering
In der ersten Phase des Arbeitsablaufs für die Entwicklung von Kabinengehäusen muss das spezifische Fahrzeugmodell, für das das neue Kabinengehäuse hergestellt werden soll, rekonstruiert werden.
Um einen passgenauen und flexiblen Sitz der Kabinen zu gewährleisten, benötigen die Konstrukteure von Curtis genaue Maße des Zielfahrzeugs, bevor diese in der nächsten Phase verwendet werden, wenn auf der Grundlage der bekannten Maße ein CAD-Prototypmodell der Kabine erstellt wird.
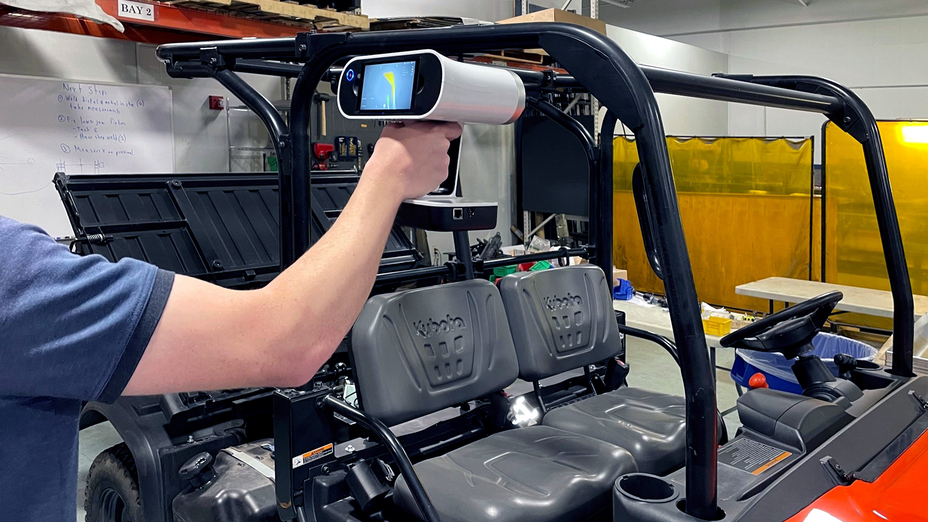
3D-Scannen des Überrollbügels eines Nutzfahrzeugs von Kubota mit Artec Leo. Bild mit freundlicher Genehmigung von Curtis Cabs.
Um dies zu erreichen, wurde in der Vergangenheit eine Reihe von Werkzeugen verwendet, darunter Maßbänder, Messschieber, Senklote und ein Arm einer Koordinatenmessmaschine (KMG).
Vom KMG zu Artec Leo
Obwohl der KMG-Arm durch seine Scans ausreichend präzise Maße lieferte, machten die langsame Arbeitsgeschwindigkeit des Arms, die schweren Montageplatten und die begrenzte Reichweite jede Arbeit zu einer langwierigen und mühsamen Angelegenheit – ganz zu schweigen davon, dass das Gerät während jeder Sitzung mindestens viermal neu positioniert werden musste.
Ein typischer Arbeitsgang mit dem KMG dauerte 4-8 Stunden, und das war erst der Anfang. Die gleichen KMG-Scans würden weitere 2 bis 3 Tage oder mehr in Anspruch nehmen, bevor die Konstrukteure von Curtis mit ihrer Arbeit beginnen konnten.
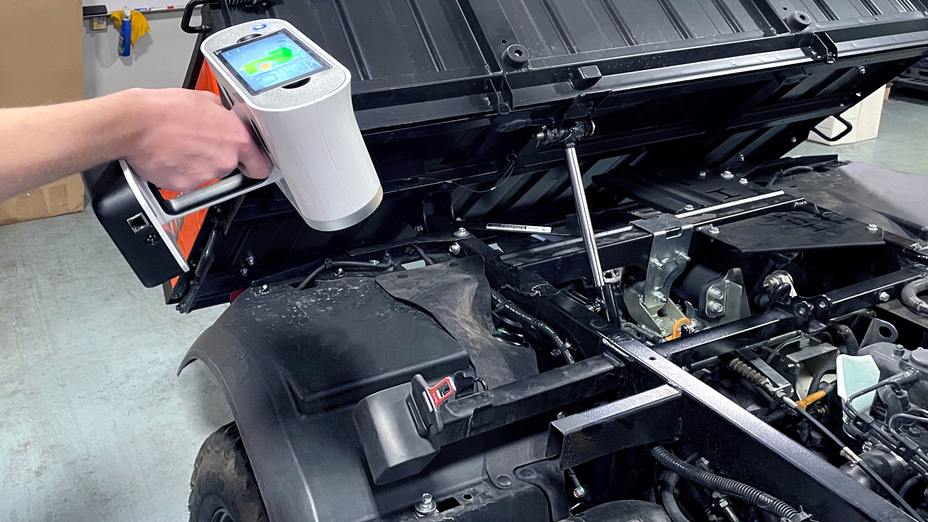
3D-Scannen des Motorbereichs eines Nutzfahrzeugs von Kubota mit Artec Leo. Bild mit freundlicher Genehmigung von Curtis Cabs.
Smith erkannte, dass dieser Teil des Arbeitsablaufs für sein Team zu zeitaufwändig war, und machte sich auf die Suche nach einer besseren Lösung. Bei seinen Recherchen stieß er auf das 3D-Scannen, und nur wenige Stunden später kontaktierte er Bo Helmrich vom Artec Ambassador Digitize Designs. Dieser erzählte ihm von Artec Leo, einem professionellen 3D-Scanner, mit dem das Problem gelöst werden könnte.
Ein einziger Scan genügte
Doch da man nur das glauben sollte, was man gesehen hat, nahm Helmrich die Fahr durch einen Schneesturm auf sich, um persönlich Smith und seine Ingenieure in ihrem Werk in Massachusetts zu treffen. Dort scannte Helmrich zur Demonstration der Fähigkeiten von Leo einen großen Traktor.
Smith und sein Team waren hocherfreut zu erleben, wie einfach und schnell Helmrich das Fahrzeug gescannt hatte, wobei bei jedem Durchlauf des Scanners Millionen von Datenpunkten erfasst wurden, und das alles ohne störende Kabel oder einen zusätzlich angeschlossenen Laptop.
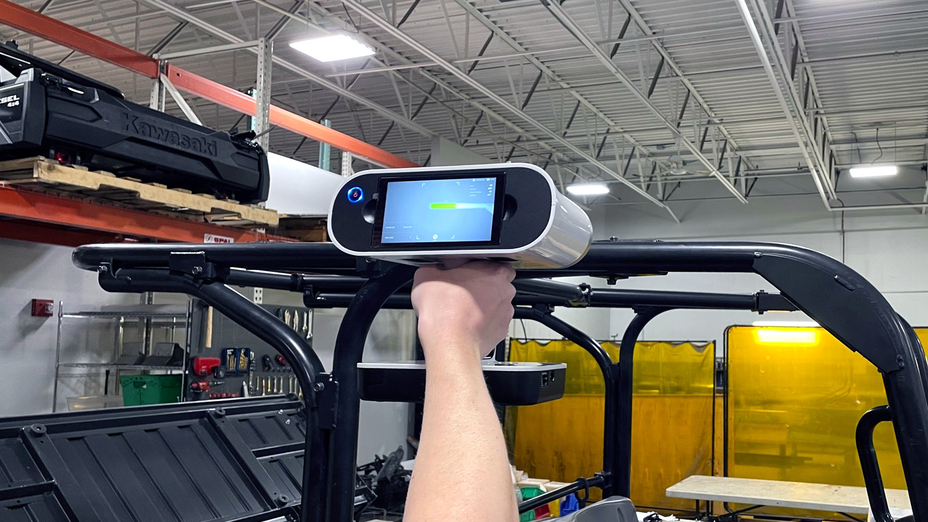
3D-Scannen des oberen Überrollbügels eines Nutzfahrzeugs von Kubota mit Artec Leo. Bild mit freundlicher Genehmigung von Curtis Cabs.
Mit dem in Leo integrierten Touchscreen konnten Smith und sein Team in Echtzeit beobachten, wie der Scan des Fahrzeugs entstand, wodurch Sie sofort sahen, dass alle benötigten Formen und Merkmale erfasst worden waren.
Minuten später: Export der Scans in CAD
Wenige Minuten später führte Helmrich dem Team vor, wie es ist, die Scandaten aus der Software Artec Studio über das Geomagic-for-SOLIDWORKS-Plugin direkt in SOLIDWORKS zu exportieren. Dort wurden die Oberflächenscans des Fahrzeugs durch Hinzufügen von Ebenen, Zylindern und anderen Referenzmerkmalen nahtlos in ein CAD-Modell umgewandelt.
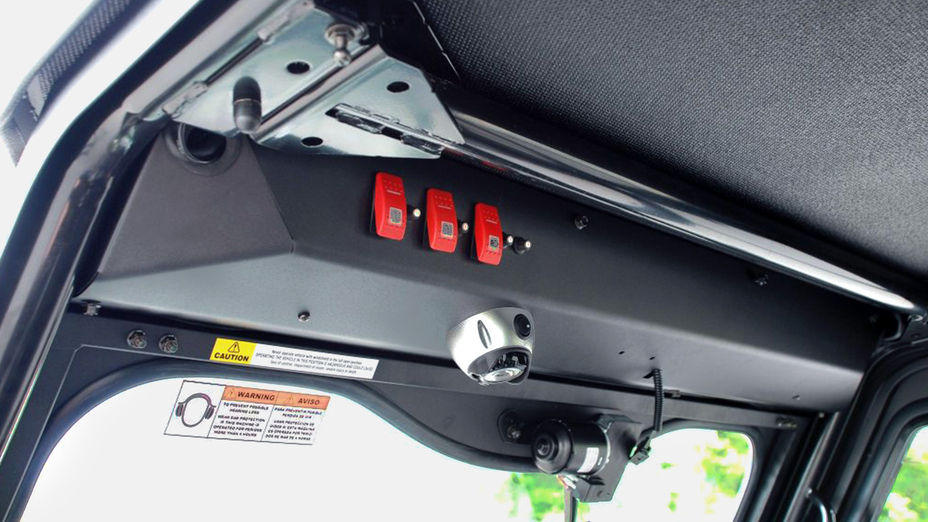
Innenverkleidung und Überrollbügel von Curtis Cabs für einen John Deere Gator XUV. Bild mit freundlicher Genehmigung von Curtis Cabs.
„Das ist ein enormer Fortschritt in unserem Ablauf vom Entwurf zur Fertigung.“
„Wir waren erstaunt, wie schnell und schmerzlos Leo alles gescannt hatte, verglichen mit dem, was wir früher mit unserem KMG gewohnt waren. Da wir unsere Produkte auf der Grundlage gescannter Fahrzeugdaten entwickeln, ist dies für uns ein enormer Fortschritt in unserem Ablauf vom Entwurf zur Fertigung“, so Smith.
Curtis Industries entschied sich noch am selben Tag für den Kauf eines Leo.
Leo im Vergleich zum KMG
Um die bedeutenden Veränderungen zu quantifizieren, die Leo bereits für den Ablauf vom Scan zu CAD gebracht hatte, kehrten Smith und sein Team nach dem Kauf zu ihrem traditionellen Ansatz mit KMG zurück und zeichneten jeden Schritt beim Scannen eines Fahrzeugs für die Konstruktion einer neuen Kabinenverkleidung auf.
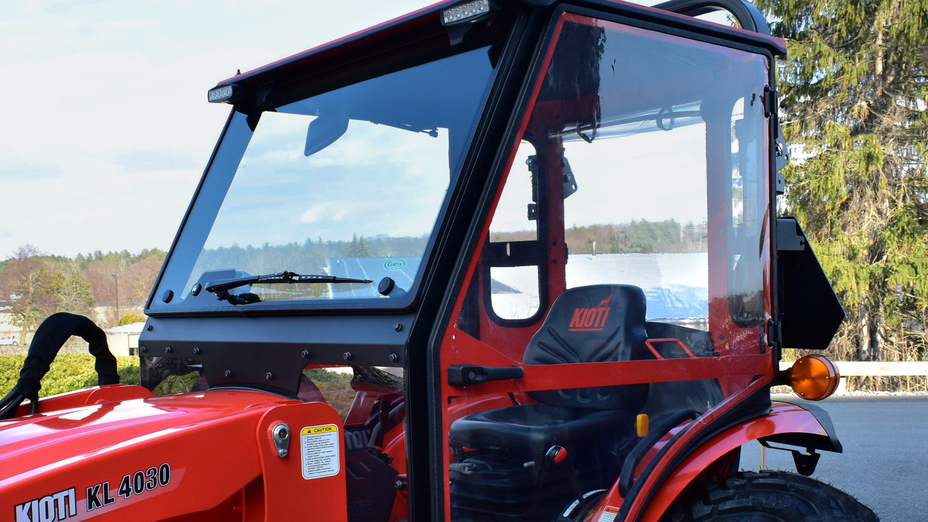
Ein von Curtis Cabs spezialangefertigtes Kabinengehäuse für einen Bobcat CT20. Bild mit freundlicher Genehmigung von Curtis Cabs.
Danach wiederholten sie den denselben Arbeitsablauf mit demselben Fahrzeug und unter Einbeziehung von Artec Leo und zeichneten auch diesen auf. Der Kontrast war, um es vorsichtig auszudrücken, verblüffend:
Scan-Geschwindigkeit: Wofür sie früher mit einem KMG 4-8 Stunden gebraucht hatten, benötigen sie nun mit Leo weniger als eine Stunde.
Umfang der Oberflächendaten: Im Gegensatz zum KMG-Arm, der nur eine Handvoll Merkmale misst, erfasst Leo sämtliche gescannten Oberflächen, Vertiefungen und unregelmäßigen Formen eines Fahrzeugs, so dass diese Fülle von geometrischen Daten in CAD als genaue Referenzmodelle für die Erstellung neuer Produktentwürfe verwendet werden können.
Scan-Verarbeitung: Pro Fahrzeug von 2 bis 3 Tagen oder mehr mit KMG-Scans auf unter eine Stunde mit Leo.
Die goldene Synergie: Tragbarkeit und Nutzerfreundlichkeit
Smith und sein Team profitieren von der Nutzerfreundlichkeit von Leo und der kurzen Lernkurve, dank der die Einarbeitung neuer Konstrukteure erleichtert wird. Und natürlich von der Tragbarkeit des Scanners.
„Leo kann problemlos und jederzeit mitgenommen oder zu einem Fahrzeug gebracht werden, wann immer wir ihn brauchen.“
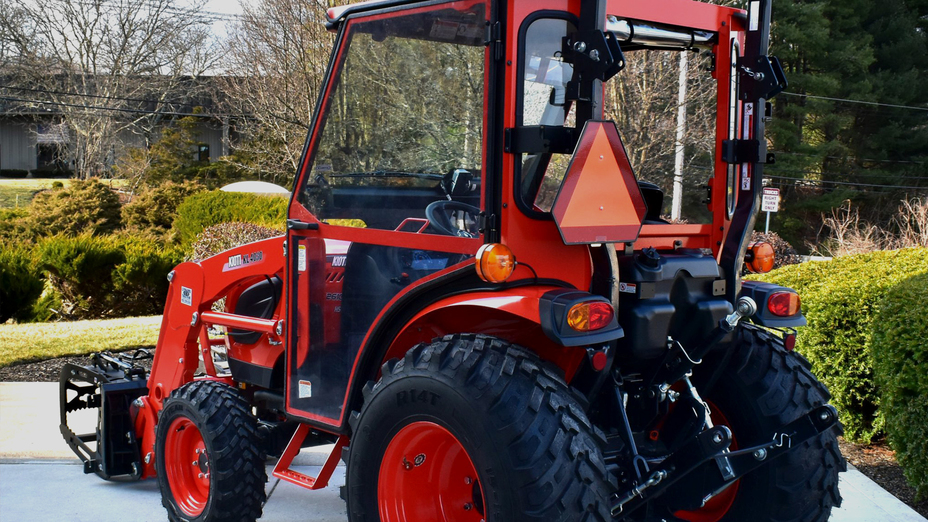
Rückansicht der von Curtis Cabs gebauten Kabine eines Bobcat CT20. Bild mit freundlicher Genehmigung von Curtis Cabs.
Im Vergleich zu dem schweren und unhandlichen KMG, das zum Scannen zu den Fahrzeugen transportiert werden musste, sagt Smith: „Leo kann problemlos und jederzeit mitgenommen oder zu einem Fahrzeug gebracht werden, wann immer wir ihn brauchen.“
Smith und sein Team freuen sich nun darauf, ihren Leo in den kommenden Monaten und Jahren unternehmensweit für immer mehr Anwendungen einzusetzen, darunter das Reverse Engineering von Fahrzeug- und Traktoranbauteilen und noch vieles mehr.
Scanner hinter der Geschichte
Testen Sie die weltweit führenden 3D-Scanner.