Colt Group repairing leaks while keeping refineries running with Artec Leo
Challenge: Rapidly repairing leaking piping systems at continuous cycle production facilities in a way that doesn’t require them to be shut down and minimizes environmental impact.
Solution: Artec Leo, Artec Studio
Result: Instead of sketching out the repairs needed to fix leaks while keeping facilities active, the Colt Group now 3D scans them in a more accurate, up to 18-times faster workflow.
Why Artec 3D?: Using Artec Leo’s built-in display and wireless functionality, the firm is able to capture as-fitted geometries in the field, and customize repair solutions to meet client needs.
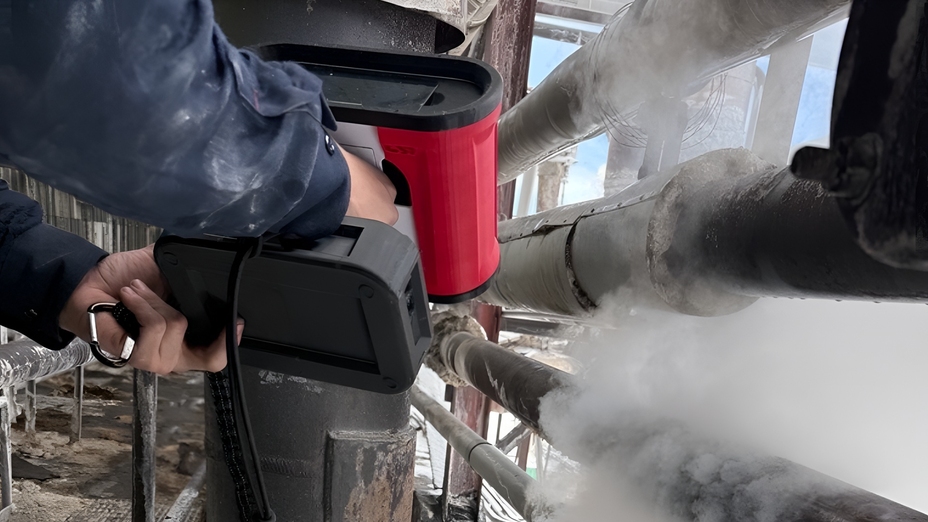
A Colt Group engineer 3D scanning pipework using Artec Leo. Image courtesy of the Colt Group
Pressurized piping repair is a particularly common issue at oil & gas refineries, where valves, fittings, and connections are prone to corrosion and fatigue cracking. Traditionally, repairs are designed by taking physical measurements and hand-drawing the component to be repaired, but complex, odd geometric features are increasingly making this methodology seem obsolete.
Measuring the diameter of pipes that range in width from one inch to over a meter – with an accuracy of just a tenth of an inch – can also be extremely challenging for engineers.
Then there’s timing: broken pipes often carry unpleasant substances with the potential to disrupt operations. While many site operators schedule routine maintenance, fixing these issues is an urgent task. Machinery like petrochemical reactors can’t just be deactivated either. Turning these off spontaneously would cause equipment the size of a multi-story building to fail.
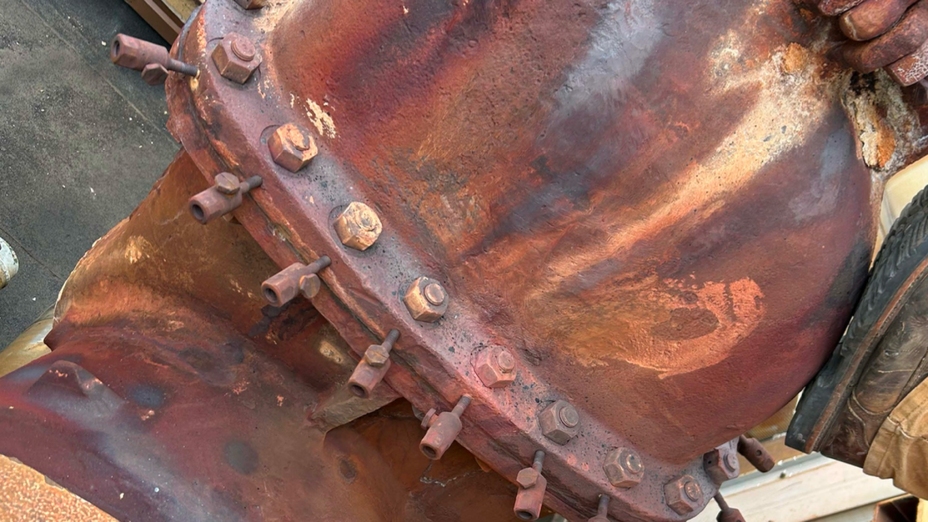
An example of the complex valve geometry the Colt Group is tasked with repairing. Image courtesy of the Colt Group
Clearly, a stop-gap solution is required to allow for quick, accurate repairs. That’s where service providers like the Colt Group really excel. With 30 offices serving customers across half the US, the company carries out repairs on-site with Artec Leo, while keeping critical assets running.
“We do ‘online’ leak repair. The faster we can do the job, the faster we can seal the leak for a customer, and decrease the likelihood of having to shut down,” explained the Colt Group IT Director Wally Whitley. “We’re also helping save our customers quite a bit of money by minimizing lost product and maintaining productivity.”
“We keep them from having to shut down their process. The quicker we can do each step of our process, the more valuable we are to the customer.”
Unlocking ‘online’ refinery repairs
Until recently, all Colt Group engineers would arrive on-site at a customer’s refinery or plant and measure affected areas of piping via manual sketching. Once ready, these drawings or 2D PDFs would be sent to its engineering team, so they could design the repair solution.
This process, which is still used to map out repairs on infrastructure composed entirely of basic geometries, yields sufficiently accurate representations of leak sites, but often takes two people to carry out, and it can take many hours.
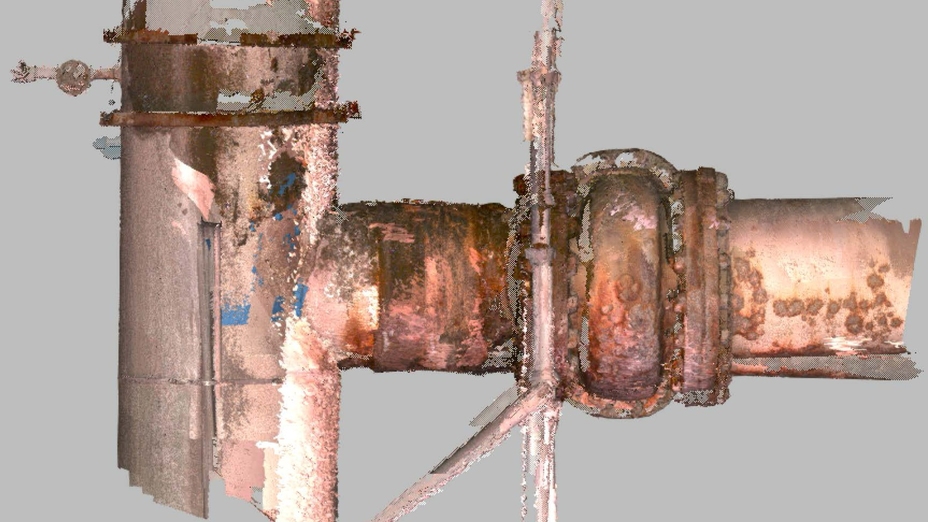
A pipework 3D scan captured with Artec Leo by the Colt Group. Image courtesy of the Colt Group
These speed and customization concerns have caused the company to reconsider its approach to measurement, but 3D scanning wasn’t always the front-running technology. In fact, the Colt Group’s Head of Engineering Mike Yates says he had major doubts over it, after previously finding it impossible to design parts for clients using sub-par scan data.
“I have received scans before over time. One of our customers previously had a team come out and do some kind of scan,” recalled Yates. “Essentially, a bunch of data points were taken, but it wasn’t anything we could turn into a solid part.”
“It was kind of unusable. That was around ten years ago, and that framed my opinion of 3D scanning. So honestly, I was skeptical.”
Revamping site mapping
Despite these early reservations, Whitley says the Colt Group’s CEO Jason Box came across Artec Leo last year, and it was such a different device, he insisted his firm “had to try it out.”
Since then, the wireless, AI-powered 3D scanner has proven so easy-to-use and fast that the company’s technicians have been able to quickly get to grips with it and start capturing piping in just 15-20 minutes. Describing Leo as “very intuitive,” Yates says his team has found its built-in display to be particularly useful, as it allows them to confirm they’ve got the data they need “when areas go from green to red,” without having to check a PC monitor.
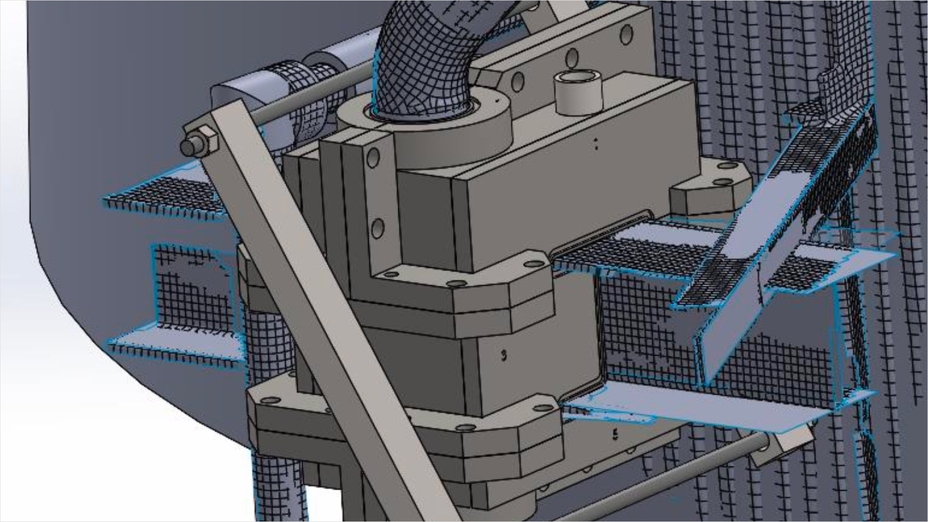
A pipe repair clamp designed based on Artec 3D scans. Image courtesy of the Colt Group
In terms of accuracy, he adds that “Leo is obviously superior,” but the Colt Group has benefited more from the new level of pace and customization it’s now able to measure with. “What we use the Leo for is the odd geometries that show up in the field,” Yates continued. “Not everything is circles or squares and follows a path. Some geometries are odd, some are impossible, and measuring others would take so long that it’s not worth the effort.”
Customizing leak repair clamps
Switching to Artec 3D scanning has also seen the Colt Group start using Artec Studio. The industry-acclaimed scan data capture and processing software comes with multiple features designed to make life easy for new adopters. The program’s Autopilot automatically chooses the right algorithm for dealing with a scan, so even newcomers can optimize results.
According to Whitley, the platform has proven so easy for the firm’s technicians to use that over the last year, they’ve been able to create accurate models using only the presets Artec Leo came with. This accessibility has really freed up the Colt Group to experiment.
Since adopting Artec Leo across its business, the Colt Group has also been bowled over by the results. More accurate measurements have meant fewer reworks, while faster data capture has allowed them to deliver a more premium, accelerated service.

A Colt Group engineer installing a massive pipe repair clamp. Image courtesy of the Colt Group
Already, Leo is allowing the company to carry out more projects with the same team. One day, Yates believes that Leo will capture up to half the tens of thousands of parts it measures each year. As such, the Colt Group hasn’t calculated the ROI on its devices, but it’s anticipated they’ll easily deliver the cost savings required to pay for themselves in the years to come.
“You just point Leo at an object, and it scans what you’re looking at. That’s the obvious future with measuring. That’s the path it’s going to take over time. It just works, that’s the key really.”
Scanners behind the story
Try out the world's leading handheld 3D scanners.