Bringing artisanal boat repair into the 21st century with Artec 3D scanning
Challenge: Capturing complex boat geometries with the speed and accuracy needed to model, CNC machine, and install refit & repair parts faster than industry competitors.
Solution: Artec Leo, Artec Ray II, Artec Studio, Quicksurface
Result: Instead of taking six hours to size up boat cockpits and decking, the firm can now speed through this process in just two hours. Embracing digital design has also made it easier to cost-effectively create custom interiors and exteriors using CAD-led manufacturing.
Why Artec 3D?: Artec Leo precisely picks up fine details, Ray II captures open spaces, and Artec Studio seamlessly fuses resulting data as part of an unbeatably efficient workflow.
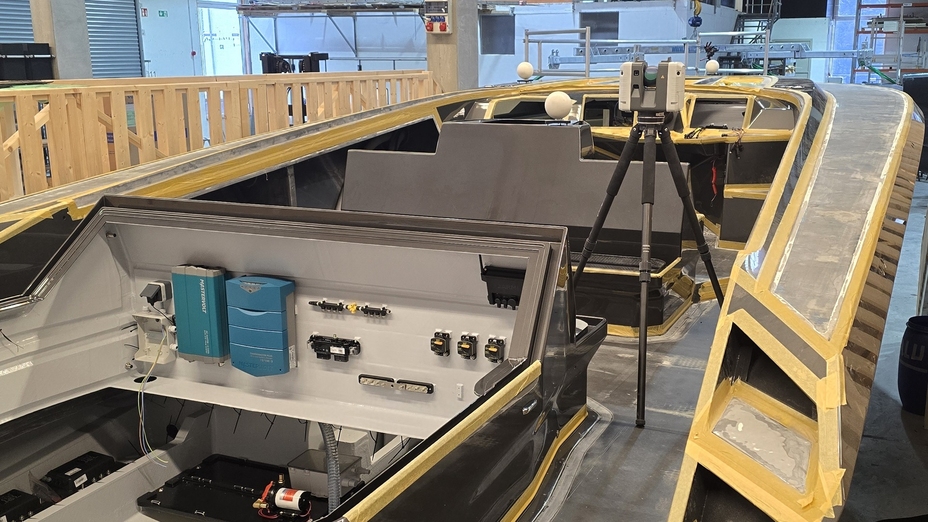
Artec Ray II 3D scanning onboard a client’s boat. Image courtesy of Blaupause Bootsbau
Once considered an indispensable combination of engineering and craftsmanship – even a form of art in some quarters – the business of boat building has changed beyond recognition.
Gone are the days of small wooden boats built on planks or stitched together via skin-on-frame techniques, where crafts would be restored using traditional fittings and finishing.
In the highly competitive modern maintenance, repair, and overhaul (MRO) space, cost and margin are key. This has increasingly seen pleasure boats made from stronger, cheaper fiberglass, and triggered service providers to pursue efficiency as a top priority.
In an effort to improve quality and cut lead times, automation has also become the order of the day. However, refit and repair jobs still require the accurate measurement of complex, tricky-to-capture surfaces, so they can either be replaced or built off. Striking this balance between profit and perfection is no mean feat, but Blaupause Bootsbau now seems to have nailed it.
Basing refits on rapid, accurate Artec Leo and Artec Ray II scans has allowed the relative MRO newcomer to cut lead times by up to two-thirds, and steal a march on many industry rivals.
Upgrading to take on the “big boys”
Since CEO Martin Dittmer co-founded Blaupause Bootsbau in 2021, its suite of pleasure boat installation, overhaul, and weather-damage repair services have taken the market by storm.
But it was not always equipped to achieve this success. When he first acquired the company’s HQ, he realized the legacy equipment he’d inherited required modernization. Capturing curved surfaces – already an issue for his other business Surface & Deck Solutions – was viewed as a particular problem, with digital manufacturing seen as the logical, cost-efficient solution.
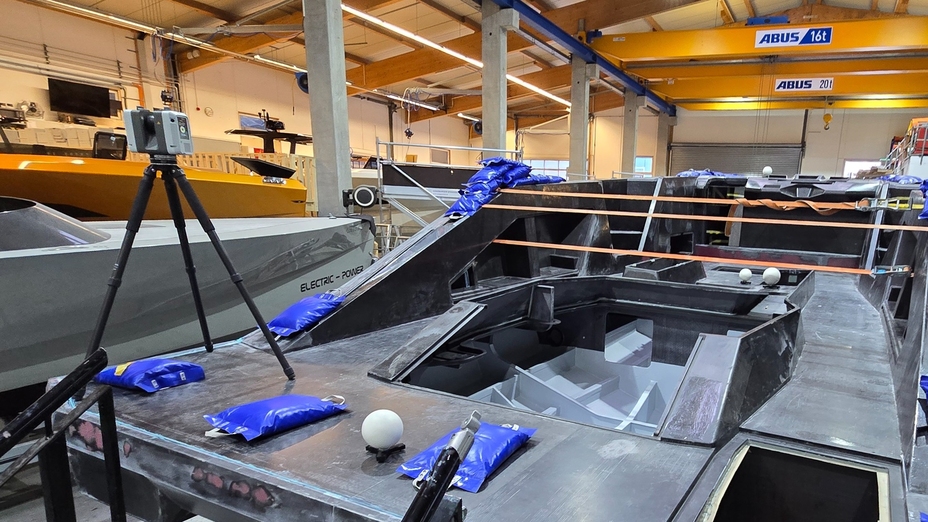
A boat deck being 3D scanned with Artec Ray II. Image courtesy of Blaupause Bootsbau
Initially, Martin tried modernizing yacht measurement with single-point lasers. However, these required data to be captured and aligned point-by-point, in a lengthy, labor-intensive manner. With lead times stretching up to six hours per project, he upgraded to a third-party scanner. But this too lacked the combined speed, accuracy, and flexibility for complete 3D data capture.
Having done some “fishing” to find the right tool for the job, Martin conceded that “if he wanted to play with the big boys, he’d need some big guns.” That’s when he called Knut Lehmann, CEO of Artec Ambassador KLIB, who demoed Artec Leo and Artec Ray II, before delivering the training necessary to get the most out of the technology.
From the moment he first saw them, Martin knew they had the potential to turbocharge his workflow. While Leo’s iPhone-like click-to-scan functionality clearly made it easy to use, Ray II’s seamless setup and range turned the idea of high-speed area capture into reality. Since getting the devices, this has been borne out in projects with rapid, exceptionally accurate results.
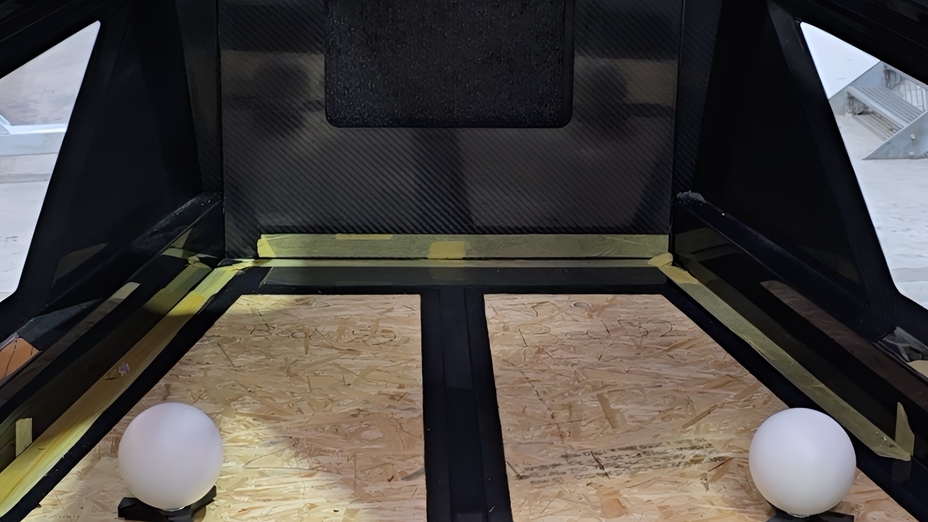
The inside of a client’s boat being prepared for 3D scanning (with reference spheres). Image courtesy of Blaupause Bootsbau
“Before, if I measured some decking or a small cockpit, I would need five or six hours. With Leo, I can scan those in ten minutes. That’s a huge time advantage,” Martin explained. “With digital twins, it’s also much easier to use CNC machining – a highly precise, accurate technology.”
“On the one hand, it’s sad that classic craftsmanship is dying. But on the other, our costs are rising, so we have to get more effective – and measurement is key to this.”
High-speed digital renovation
Once Martin has captured all the data needed, it’s vital that he’s able to rapidly turn this into a detailed 3D mesh. He says Artec Studio offers a “super intuitive” means of achieving this, with Autopilot automating many manual steps, and picking the best data algorithms on his behalf.
Artec Studio includes many reverse engineering essentials, but Martin prefers to export mesh data to Quicksurface, a low-cost scan-to-CAD software. There, it’s possible to extract primitives, which can be used as 2D templates for customization and CNC machining. Despite having only recently adopted this workflow, he says it’s already proving transformative for his business.
For example, when Storm Babet caused a huge amount of damage to boats in the Baltic Sea, Blaupause Bootsbau was able to help. Using Artec 3D scans of the unharmed side – whether it be the port or starboard – Martin says they were able to create templates that acted as ‘sticking plasters,’ filling in missing areas to get a complete picture for hull repairs.
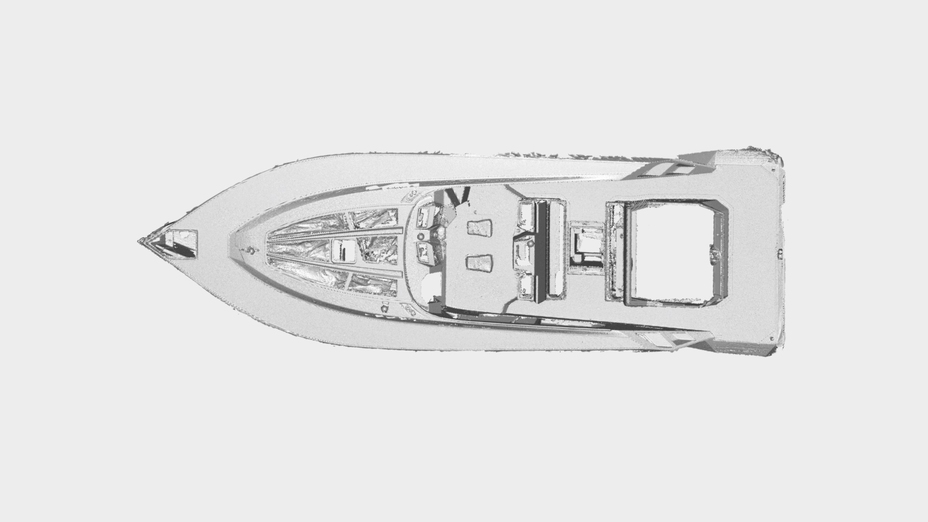
A boat model captured with Artec 3D scanning. Image courtesy of Blaupause Bootsbau
“Boat interiors are three dimensional, they always have curves and ‘ball’ shapes rather than sharp edges. Because everything has a shape, it can be difficult to measure,” Martin added. “But now we can completely renovate pleasure vessels – doing everything from electrical installation to actually installing interiors onboard yachts.”
“Artec 3D scanning allows us to capture and review data from 50 or 100 km away before making something. This helps us find any issues and tells customers we are reliable.”
Next up: Classic boat scanning?
With business booming – Blaupause Bootsbau had some 250 small boats in its last winter stock – Martin is now eyeing an expansion into even faster, higher-precision 3D data capture.
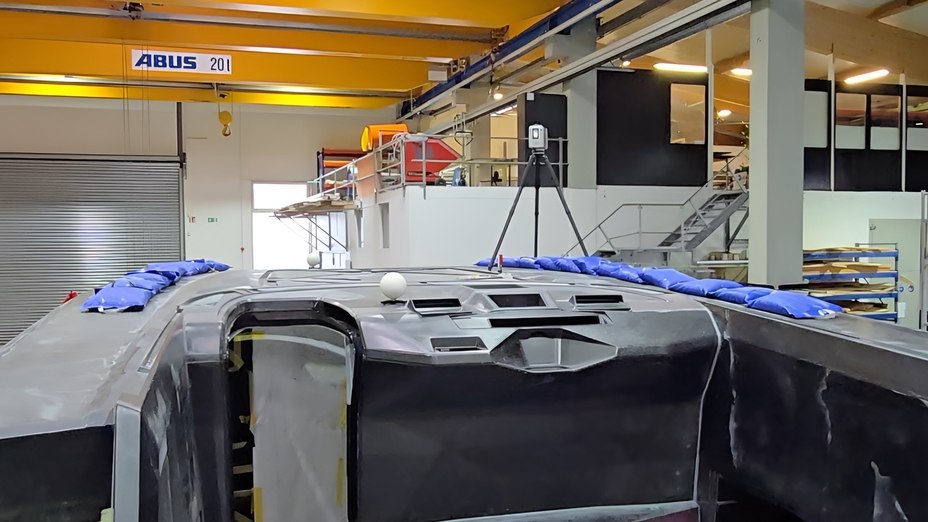
Ray II 3D scanning inside Blaupause’s MRO facility. Image courtesy of Blaupause Bootsbau
Many of the older yachts it renovates feature small legacy parts. While Leo is capable of digitizing these, Martin says he may start capturing them with Artec Spider II, a better-suited high-precision device that picks up fine details with 0.05mm accuracy for reverse engineering.
That said, some projects allow for minor deviations, so he “doesn’t mind if measurements are a millimeter out,” as it’s all about digitizing quickly. In this regard, Leo & Ray II continue to offer an unparalleled level of speed and accuracy, which addresses most MRO capture needs.
“Artec Leo works in pretty much every application, we use it every day,” Martin concluded. “It’s such a powerful tool, it has helped us get over our biggest issue: creating digital twins. Digital measurement is only going to become more interesting for reverse engineering as we continue to integrate it into our daily routine.”
Scanners behind the story
Try out the world's leading handheld 3D scanners.