What is NDT?
In manufacturing, it’s common to hear the phrase non-destructive testing or ‘NDT.’ But what does it actually mean? NDT is a catch-all term that describes any process of measuring or evaluating the properties of a product without having to damage it. In this article, we take a look at potential workflows, applications, and technologies for achieving the best NDT results.

Image source: Zetec NDT
Also known as non-destructive evaluation, examination, or inspection, non-destructive testing is used everywhere from aerospace and defense to heavy industry. It’s very much a blanket term that describes numerous technologies, all of which serve a similar purpose.
In essence, NDT is all about measuring products with speed and accuracy to ensure a high level of quality, stability, and compliance. Whichever process you choose, it must meet two key criteria: it has to minimize disruption to the object’s operation and it must not cause damage.
Avoiding product damage and wastage has clear benefits in terms of sustainability and costs. But we’ll go deeper into the advantages of NDT shortly. At this point, it’s probably best to start by defining NDT’s many processes by comparing them to the alternative: destructive testing.
Key point
NDT is all about analyzing the properties of an object or material without causing damage – so they can be reused or retested.
Destructive testing vs non-destructive testing
During destructive testing, sample products are pushed (literally) to breaking point using stressors, clamps, and other machinery. The goal is often simple: to discover the limits of specimens and ascertain key characteristics like tensile strength and impact resistance.
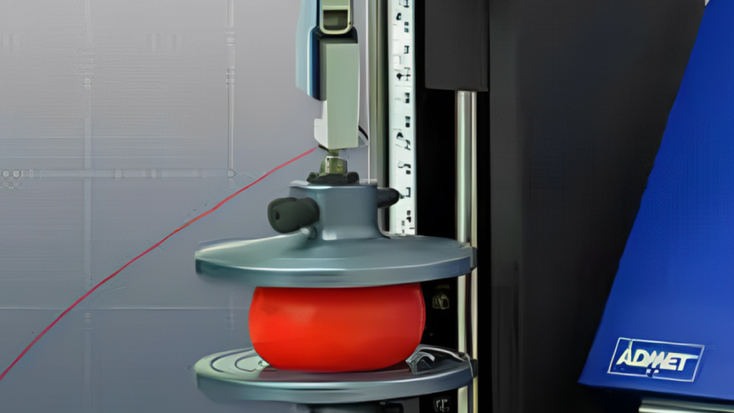
Image source: OnestopNDT
Processes like macro-sectioning, tensile testing, and 3-point bend testing, for instance, test material properties, flexibility, and reliability, while uncovering potential weaknesses. However, they also render products unusable, making them unsuitable for critical component testing.
On the flipside, non-destructive testing or ‘NDT’ makes it possible to analyze objects without damaging them at all. Assessing the integrity of structural parts with non-contact measurement techniques like 3D scanning allows for earlier defect detection and planned maintenance. This level of advanced planning ultimately reduces the costs and downtime caused by part failures.
Advantages of non-destructive testing
Of course, there are certain situations where DT is preferable to NDT. But there are many more cases where non-destructive testing methods are just better economically. Constantly destroying samples is inevitably more expensive than reusing them. Remanufacturing also takes time, making destructive testing a lengthier, more labor-intensive process.
Then there are monitoring use cases. In applications like bridge inspection, it’s helpful to track the strength of infrastructure over time and monitor its rate of deterioration. Similarly, repeat impact assessment isn’t possible if products are destroyed during testing. This highlights the preventative nature of NDT – it allows vulnerabilities to be detected and tackled early on.
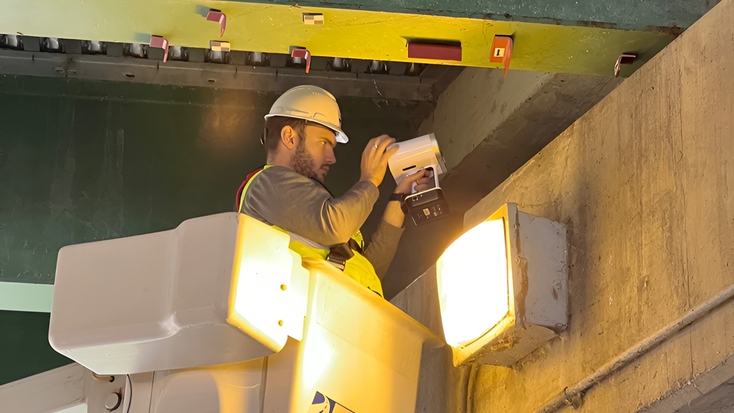
Key point
Monitoring a product or build over time allows faults to be identified in real time and rectified before they worsen.
Lastly, there’s convenience. NDT can often be carried out in situ, meaning that products don’t need to be removed for testing, and manufacturing processes can keep on going. DT may even require specialized off-site testing equipment, so it can be a lot less practical to implement.
Overall, destructive testing has its place. But non-destructive testing is faster, cheaper, more convenient, and less disruptive, while delivering next-level long-term analysis. So, that covers why you should adopt NDT. Let’s move on to the different testing technologies available.
Non-destructive testing methods
Visual NDT
Generally seen as a preliminary step, visual NDT is basically the process of looking for surface imperfections, either with the naked eye or equipment like mirrors, borescopes, or videoscopes.
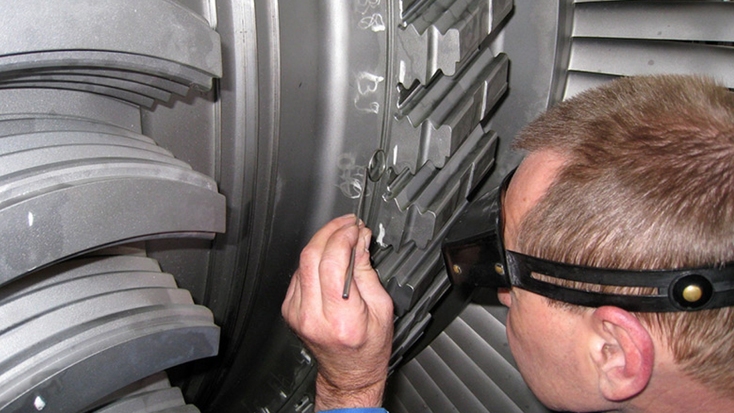
Image source: TÜV Rheinland
Common issues uncovered using visual NDT include corrosion, fatigue, and cracking – which can impact structural integrity. This makes the technique particularly useful for evaluating how parts have been fused together with welding. Visual NDT can also be used for ‘common sense’ checking, to ensure that no time is wasted subjecting unusable parts to further testing.
As one of the most accessible forms of NDT, visual checks are used in the early stages of manufacturing across countless industries. Tools are often relatively cheap, they don’t cause product damage, and their simplicity makes them easy to adopt. However, the process can get quite subjective, and results may change depending on conditions. For greater consistency and reliability, sub-surface analysis may be required.
Key point
Visual checks may seem a little rudimentary, but they’re often just the first stage in a multi-step inspection pipeline.
Ultrasonic NDT
Using high-frequency waves, it’s possible to analyze properties, detect flaws, and measure the dimensions of materials and objects. This ultrasonic NDT or ‘UT’ process is known to be highly precise and versatile, making it ideal for identifying internal anomalies and verifying integrity.
In general, the technology’s penetrative power also allows for fast, accurate detection, even when inspecting obscured products where only one side is accessible. There are also different variations of ultrasonic NDT that deliver better results in certain circumstances. Sheer waves and phased arrays, for example, detect flaws parallel to the surface and at multiple angles.
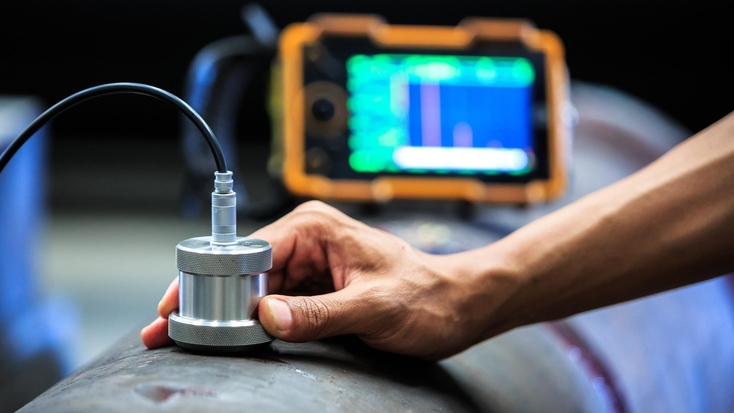
Image source: IUT de Bordeaux
Ultrasonic thickness testing involves sending a shockwave through a component and measuring how long it takes to return. Thickness is often a key measure of corrosion, so this is commonly applied in areas like oil & gas, where pipeline leakage is a frequent challenge. In cases where objects are submersed in a liquid, wave transmission can also be enhanced to boost accuracy. But ‘ultrasonic immersion’ is generally saved for the most complex, underwater analyses.
Radiography NDT
Radiographic testing is also an NDT method for analyzing internal structures, only it involves identifying product flaws using X-rays and gamma rays rather than ultrasound.
In practice, this process sees a product placed between a radiation source and detector. When radiation is fired at a component, the level of penetration, scattering, and absorption tells manufacturers where there are deviations in thickness and density. Of course, radiographic testing is highly regulated due to the nature of the technology. So limiting any risk with shielding, protective equipment, and the employment of highly qualified staff is all vital to safety.
That said, the technology itself is tried and tested in industries like oil & gas for pressure vessels, or aviation, where it can be used to ensure the flight-readiness of aircraft parts. Its portability and time-consuming nature do limit its applications. Radiography is also less effective with thin-layered parts. But the technology seems to thrive in the most demanding areas.
Key point
X-rays and gamma rays offer an alternative to ultrasonic NDT that allows manufacturers to see deep inside parts made for demanding industries.
Eddy current NDT
Eddy current testing harnesses electromagnetism for non-destructive testing. Instead of firing wave pulses directly into parts, this means setting up an energized coil next to a test surface and generating an electromagnetic field around it. Inside the field, interactions with localized electric currents or ‘eddy currents’ can be monitored using a separate receiver coil.
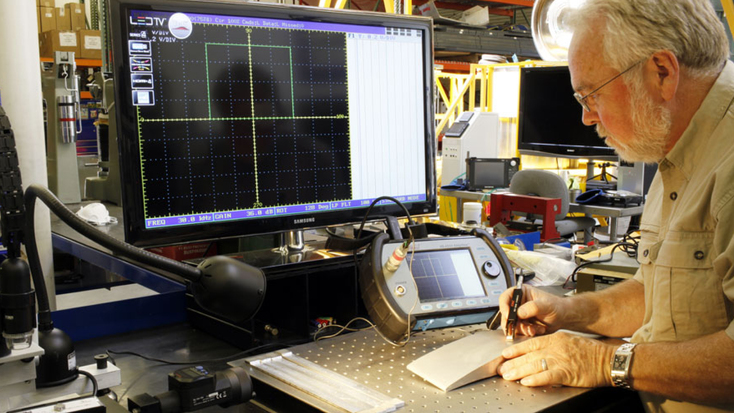
Image source: IndiaMART
Current and phase fluctuations indicate changes in conductivity, magnetic permeability, and potentially the presence of defects. Adjusting the frequency of the alternating current can help detect issues at certain depths. Higher frequencies, for instance, can be used to find defects near object surfaces. The reverse is true for deeper defects, but lower-frequency scans are also less sensitive, so there’s a balance to be struck between sharpness and reach.
This variable level of penetration is compounded by other issues, such as its inability to detect defects in non-conductive parts, or areas running parallel to sample object surfaces. But it is fast, easy to set up, and delivers usable results in a single pass. It can also peer deep inside objects’ interiors, making it ideal for the inspection of complex designs.
Magnetic particle NDT
There’s also another form of electric current-based NDT: magnetic particle testing or ‘MT.’ Similarly to eddy current NDT, MT sees surfaces charged with currents for defect detection, only it works with ferromagnetic materials instead like iron, nickel, and cobalt.
Compared to other testing techniques, magnetic particle NDT has numerous advantages. Not only is it highly portable, cheap, and quick to set up, it’s great for picking up fine cracks at shallow surface levels, even when working with coated materials. However, there are limitations around size, shape, material, and field orientation. Likewise, defects deep inside products can be beyond reach – and using large currents to address this can lead to part burning.
Key point
Eddy current and magnetic particle NDT offer two different ways of measuring disruptions within electric currents to uncover potential product issues.
Acoustic emission NDT
NDT may be non-destructive, but it’s not always non-contact. Just take acoustic emission, a process that requires the mounting of sensors onto sample objects. Acoustic waves are then emitted into the part, with sensors detecting any ‘stress waves’ received back. The wavelengths of these indicate high pressures or loads and increase in intensity depending on integrity.
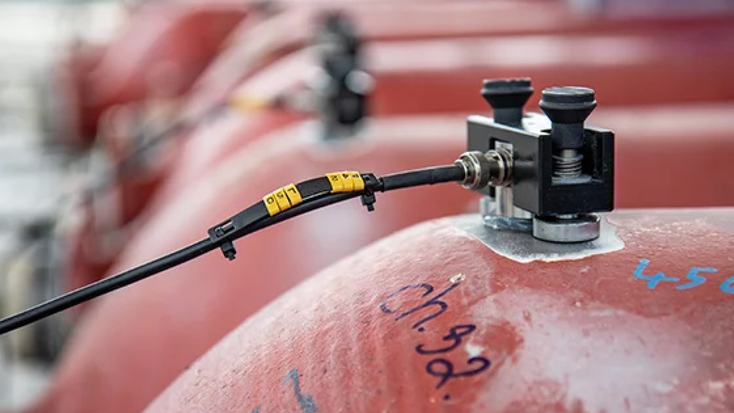
Image source: Shutterstock
As acoustic emission NDT merely involves sending tremors through parts, the technique itself doesn’t require users to halt operations. Products can be tested during usage or even through developmental testing. It’s also super versatile, detecting everything from corrosion to fiber breakages, and it can be carried out remotely within harsh environments.
On the other hand, acoustic emission is limited to static defect detection and location. Further analysis is often needed to diagnose and rectify faults that develop over time.
Dye penetrant NDT
In effect, dye penetrant testing sees non-porous samples coated with a removable liquid dye, which seeps into any pores and cracks that may have emerged inside. A variety of colorful developer fluids can then be used to highlight defects during the subsequent inspection.
Porous, elastic, or sponge-like parts generally won’t work with this approach. Traditionally, it has been used to assess steel or iron parts, but dye development continues to unlock applications around plastic resins, glass, and ceramics. The process’ low cost, simplicity, and ability to find hidden channels has made it particularly popular in forging, casting, and welding inspection.
However, pre-cleaning is essential to achieving usable results. Penetrants are often made with hazardous chemicals as well, meaning that this NDT technique can be high-maintenance.
Key point
Techniques like dye penetrant NDT aren’t non-contact, but they do make defects quick and easy to identify during inspection.
Leak testing NDT
To a certain extent, leak testing is a form of NDT that works exactly how you’d think. During leak testing, force is applied to pressure and vacuum systems to find out if their exterior has been compromised, and if they’re running to a desired capacity. Interestingly, the process can also be carried out in situ, with indicator fluid being added for easy visual inspection.
The methodology itself is quite flexible as well. Anything from simple bubbles to radioactive gases can be used to check pressure, so it’s adaptable to wherever the leak might be, whether this is inside a food packaging factory, electronics plant, or an oil & gas facility. Of course, using certain test gases brings a raft of safety issues into consideration, but they do deliver more reliable results (due to the potential for contamination with liquid coatings).
3D scanning
Compared to traditional NDT methods, 3D scanning is less effective at capturing sub-surface geometries, but it’s also incredibly flexible, accurate, and precise – all invaluable assets for inspection. Wireless, target-free scanners like Artec Leo are completely non-contact and highly maneuverable, so they can be deployed anywhere, without cables or risk of contamination.
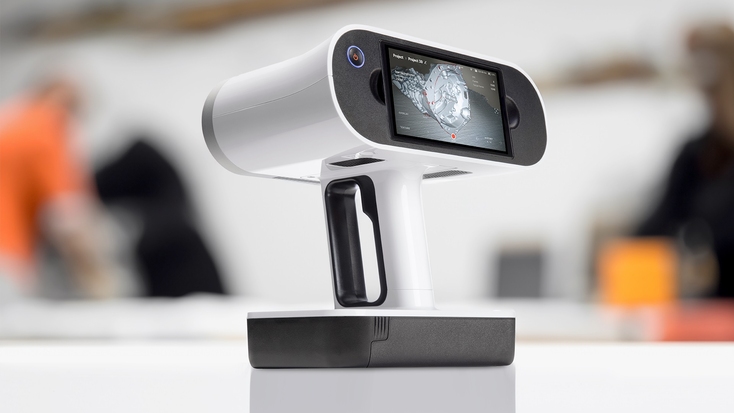
With a peak accuracy of just a few microns and a range of hundreds of meters, 3D scanning doesn’t limit application scale either. Whether you’re inspecting tiny parts or larger structures, there’s a scanning technology out there for you. If you need 100% datasets, there are even point-and-shoot devices with built-in displays that create complete 3D models in minutes.
No 3D scanner is worth having without a high-end software to match. Thankfully, programs like Artec Studio continue to take steps forward, improving both data quality capture and allowing for new applications with added functionalities. HD Mode, for example, makes it possible to pick up fine lines and tricky surfaces in stunning resolution. Built-in measurement and analysis tools are also increasingly bringing digitization and inspection together on a single platform.

Key point
3D scanning offers a unique blend of non-contact data capture, scalability, high accuracy, and rapid speed – making it ideal for industrial inspection.
Applications
Oil & gas
In the oil & gas industry, pipeline breaches are fairly commonplace. What matters is getting them fixed as quickly as possible to minimize the potential for further damage, environmental issues, and throughput disruption. NDT plays a critical role here, allowing for cracks and corrosion to be detected quickly, accurately, and early on.
Team, Inc. uses Artec Leo to capture the geometry around burst piping itself. Its engineers then remotely develop custom pipe clamps and deploy them to site for rapid repairs.
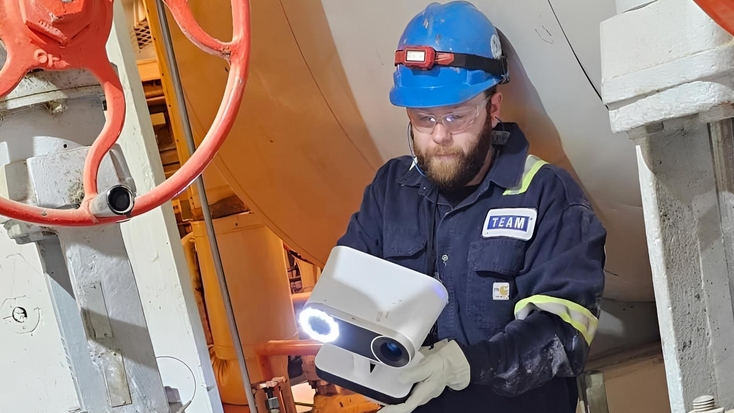
Construction
It may not be the first application that comes to mind when you think of NDT, but construction and civil engineering are perfect examples of inspection at scale. Identifying and addressing issues with infrastructure like roads, bridges, and tunnels is critical to public safety.
Fortunately, the likes of GoMeasure3D are already on the case. Using Artec Leo alongside the long-range LiDAR scanner Artec Ray II, its team have demonstrated how it’s possible to inspect a 25-foot floodwall in Richmond, USA. Voestalpine also uses a similar workflow for railway inspection, where it uncovers defects on vast swathes of railway line to prevent failures.
Key point
NDT is perfect for monitoring the condition of public infrastructure like roads, walls, bridges, and railways.
Automotive
In automotive, non-destructive testing is applied a little differently. But it’s still a vital part of ensuring that vehicles are safe and reliable once they leave the factory. Car frames and chassis are often made, repaired, and modified using welding – and these bonds require checking.
Across automotive production lines, NDT is also used at various points for quality control. This could be in the detecting of defects in parts made via casting like engine components, or the in-depth examination of tire or suspension systems to ensure they’re road ready.
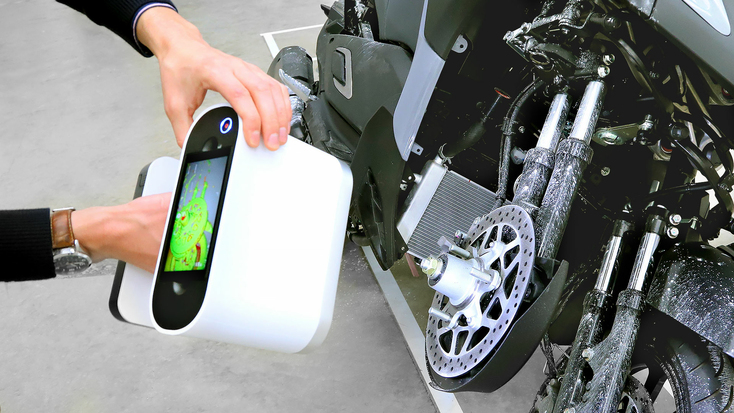
Aerospace
Whether we’re talking about civil or military applications, all aerospace parts need to meet demanding industry standards to prove their flight-worthiness. Wings, fuselages, landing gear – these elements and more need to be capable of withstanding huge pressure and temperature changes. In such cases, even submillimeter deviations can have huge consequences.
That’s why some manufacturers are turning to technologies like 3D scanning for inspection and reverse engineering. 3DMakerWorld, for example, has created a 3D model of the Sadler Vampire experimental aircraft for a customer seeking to make spare parts on demand.
Manufacturing
Arguably the most widespread application on our shortlist, NDT is hugely popular across manufacturing in quality control. Castings, forgings, and weldings all require inspection before they can be deployed on the factory floor. Machined parts, coatings, and even raw materials brought in from elsewhere also need to be checked to ensure they’re up to specification.
As such, it can be difficult to put your finger on a specific, unique production NDT application, but many of the approaches mentioned above are widely used. To name one example, Element deploys the time-tested, high-accuracy Artec Eva for the inspection of spare mining parts.
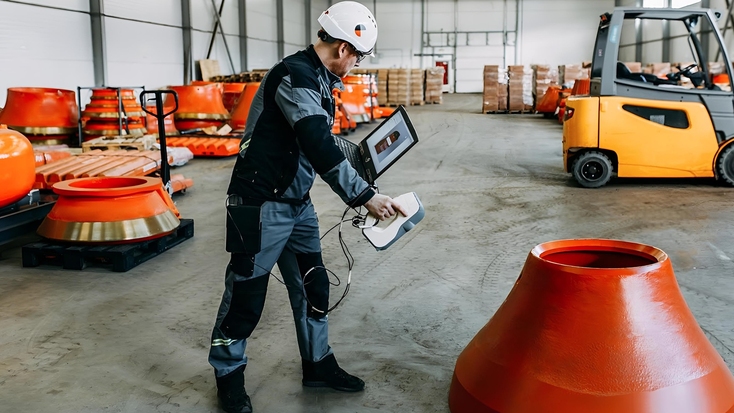
Key point
Many manufacturers already use submillimeter-accurate 3D scanning as an alternative to traditional NDT techniques.
Energy
Our final heavy-duty application of NDT lies in the power generation industry. Think massive turbine blades or generator rotors, many of which are susceptible to cracking. Power plants are also a hotspot for pipe networks that require constant maintenance. Non-destructive testing is essential in these areas and more – for keeping everything safe and in good working order.