非破壊検査(NDT)とは
製造業においては、非破壊検査、あるいはNDTという言葉を普通に耳にします。しかし、実際には何を意味するのでしょう。NDTは破壊の不要な形で製品の特性を査定し評価するどのような工程をも表す、あらゆる状況に対応できる用語です。この記事では、NDTにより最善の成果を挙げることに繋がると考えられるワークフロー、用途、及び技術について見ていきます。

画像元:Zetec NDT
非破壊評価、非破壊試験、もしくは非破壊調査としても知られている非破壊検査は、航空宇宙や防衛から重工業に至るまであらゆる場所で利用されています。同様の目的を果たす多くの種類の技術を表す、広範囲な対象を含む用語であると言えます。
本質的には、NDTは迅速で正確に製品を査定し、高いレベルの品質、安定性、及び適合性を確保することが要となります。いずれの過程を選ぶとしても、そのすべては次の二つの主要な基準を満たす必要があります。それは、対象物の稼働の中断を最小限に抑えること、そして、損傷を与えないことです。
製品が破損し、廃棄処分となることを回避することは持続可能性、及びコストの面から明らかに役立ちますが、NDTの利点については後ほど更に深く掘り下げていきます。ここでは、NDTの多くの工程を定義し、もう一つの選択肢である破壊試験と比較することが最も適切と言えるでしょう。
キーポイント
NDTの本質は、損傷を与えずにオブジェクトや物品の特性を分析し、その再利用や再試験を可能とすることです。
破壊検査vs.非破壊検査
破壊検査中、試料となる製品は圧縮試験機やクランプ、その他の機械により(文字通り)破壊点まで圧力をかけられます。その目的の多くは、単純明快です。非検査物の限界を見極め、引張強度や耐衝撃性のような主要な特性を明らかにすることです。
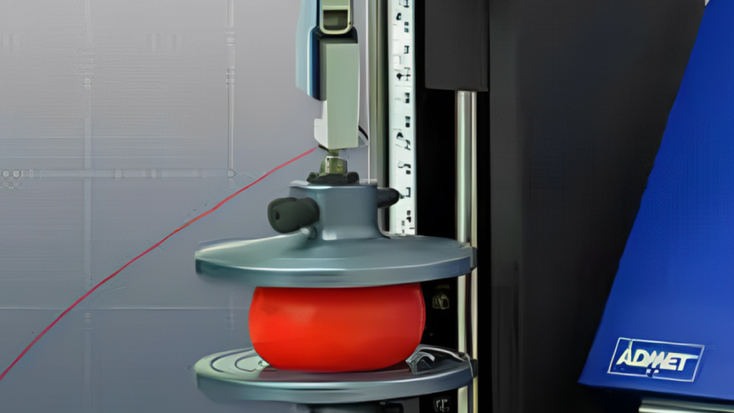
画像元:OnestopNDT
例えば、マクロ切断試験(macro-sectioning)、引張試験、及び三点曲げ試験などの過程では、材料の特性、柔軟性、及び信頼性が検査されると同時に、潜在する弱点も明らかになります。しかし、製品の再利用は不可能となり、重要な部品検査には不適当となります。
その一方で、非破壊検査、NDTは対象物に全く損傷を加えない形での分析が可能です。3Dスキャニングのような測定技術による非接触性の手段での構造部品の完全性の評価は、早い段階での欠陥検出、及び計画保全を可能とします。この水準の先進的計画は、部品の欠陥により最終的に生じるコスト及び不稼働時間を低減します。
非破壊検査の利点
もちろん、破壊検査が非破壊検査よりも好まれる、特定の状況も存在します。しかし、非破壊検査の手法の方が経済的な面でより適する、更なる数の事例があるのです。試供体を絶えず破壊していると、再利用した場合よりも必然的に高額の経費が掛かります。再製造にも時間を要するため、破壊検査はより長期にわたる、より労働集約型の過程となります。
その上、監視に関する事例もあります。橋梁検査のような用途では、基礎構造の強さの経時的な追跡、及び劣化速度の監視が役立ちます。同様に、製品が試験中に破壊されると、繰り返し衝撃診断は不可能となります。このことにより、非破壊検査の破壊を回避する特質が際立つこととなりますが、同手法は早い段階での脆弱性の特定及び対処を可能とします。
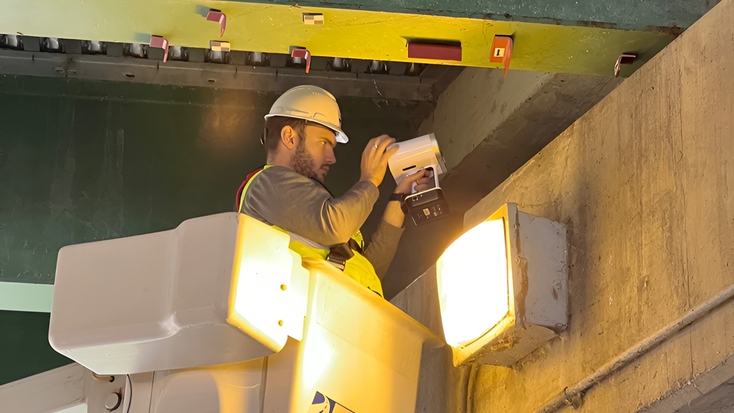
キーポイント
製品やビルドの経時的な監視により、欠陥の即時の特定や悪化する前の調整が可能となります。
最後に、利便性です。NDTは『その場で(in situ)』実行されることが多いのですが、これは製品の試験時の移動の必要が無く、製造工程を継続することができるという意味です。DTは専用の現場には無い試験機材が必要となることも生じるため、実践することがかなり非現実的になり得ます。
全般的に見て、破壊検査の相応しい場面はあるものの、非破壊検査はより高速で、コストも安く、より便利で非破壊的であると同時に、レベル一つ上の長期にわたる分析をも実現します。以上が、非破壊検査を採用すべき理由となります。では次に、利用可能である非破壊検査の異なる試験技術について見ていきましょう。
非破壊検査の手法
目視試験
一般的には予備段階と考えられている目視試験(Visual NDT)は、基本的には表面の欠陥を肉眼、もしくは鏡、ボアスコープ、あるいはビデオ内視鏡のような機材によって探査する過程です。
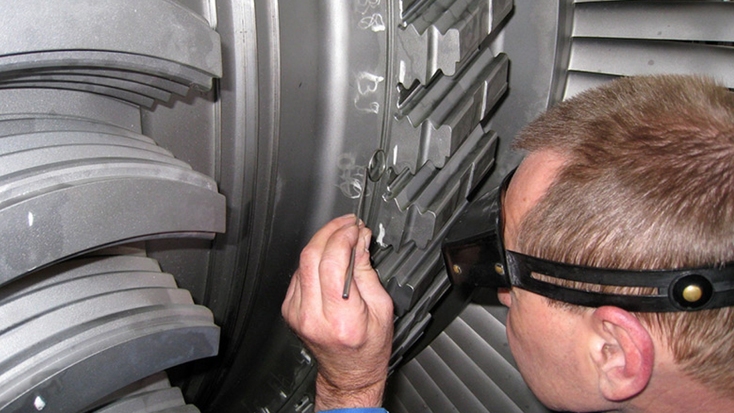
画像元:TÜV Rheinland
目視試験の利用により明らかになる一般的な問題点には、腐食、疲労、及び亀裂などがあり、いずれも構造上の完全性に影響する場合があります。そのため、溶接時の部品の融合状況の診断に特に便利です。目視試験は使用不可能な部品に試験を行うことで時間を無駄にしたりしないよう、『常識』に基づく確認を行うことにも用いられます。
非破壊検査の最も利用しやすい形態の一つである目視検査は、数えきれない産業分野において製造工程の初期段階で利用されます。試験用工具も安価なことが多く、製品に損傷も与えず、その簡便性により、簡単に採用することが可能です。しかし、工程はかなり主観的なものになり兼ねず、結果は状況により変化することがあります。 更なる一貫性、及び信頼性のためには、表面下分析(sub-surface analysis)が必要となる場合があります。
キーポイント
目視検査は少々初歩的に見えますが、多くの場合、多段階を有する検査パイプラインの第一段階となります。
超音波探傷試験
高周波を使用しての材料や物品の特性及び欠陥の分析、そして寸法の測定が可能である超音波探傷試験(Ultrasonic NDT)、いわゆるUT工程は高度に正確な上、多目的として知られているため、内部の異常の特定、及び完全性の立証に理想的な手法となっています。
一般には、この技術の透過性能により、一面のみが確認可能であるような全体が良く見えない製品の検査においても、高速で正確な発見が実現します。また、特定の状況下においてより良い結果をもたらす、別の種類の超音波探傷試験もあります。例えば、せん断波、及び位相配列は表面に並行な欠陥を複数の角度から発見します。
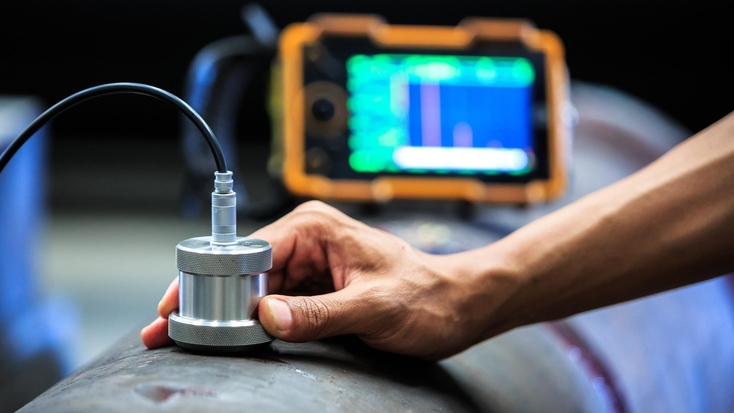
画像元:IUT de Bordeaux
超音波厚さ試験は衝撃波を部品に送り、戻ってくるまでの時間を測定する作業を伴います。厚さは腐食を評価する主要な基準となることが多いため、パイプラインの漏れが頻繁な課題となる石油ガスなどの領域で一般に採用されます。対象物が液体の中に浸してある場合では波伝達は強化され、精度が大幅に向上することもあります。しかし、『超音波浸漬』は一般に、最も複雑な部類の水面下の分析用のみに利用されています。
放射線透過試験
放射線透過試験(Radiography NDT)も内部構造の分析用の非破壊検査の方法ですが、超音波の代わりにX線並びにガンマ線を使用した製品の欠陥の特定を行います。
実際には、この過程では製品を放射線源と検出器の間に設置します。放射線が部品に照射されると、浸透、分散、及び吸収の度合いにより、製造業の方が厚さや密度に偏差がある箇所を見出すことができるようになります。もちろん、放射線を利用した試験はその技術の特質により厳しく規制されているため、遮蔽、保護用設備、及び高技能を有する業務員の採用によりリスクを抑えることは、すべて安全のために不可欠です。
とは言え、当技術自体は石油ガスなどの産業分野で圧力容器や航空機に対し十分に試行されており、航空機については、部品の飛行準備完了の確認に利用可能です。ただ、その携帯性、及び時間を要する特徴により、利用は制限されています。放射線透過試験は薄い層状の部品に対しても有効性が比較的低くなりますが、需要の多い領域では普及しているようです。
キーポイント
X線及びガンマ線によって、需要の多い産業分野向けにおいて製造された部品の内部を製造業の方が深く調べることを可能とする、超音波探傷試験の代用手段が利用できます。
渦電流探傷試験
渦電流探傷試験(Eddy Current NDT)は、非破壊検査に電磁気力を役立てます。これは、部品に直接パルス波を放射する代わりに、供試体の表面の隣りに通電コイルを設置し、周りに電磁場を生成することを意味します。この電磁場内では、受信コイルの使用によって局部的な電流、いわゆる『渦電流』との相互作用の観察が可能となります。
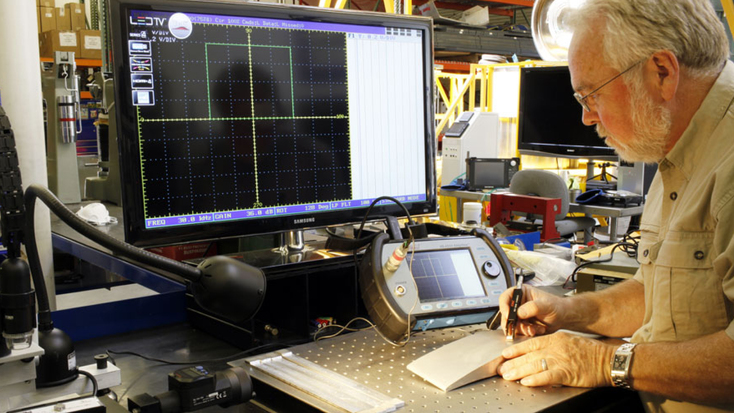
画像元:IndiaMART
電流変動(current fluctuations)及び位相変動(phase fluctuations)は、伝導率、透磁率の変化、そして欠陥の存在を潜在的に明らかにします。交流電流の周波数の調整は、特定の深さでの問題点の発見に役立ちます。例えば、高周波は対象物の表面近くの欠陥の発見に利用可能です。より奥深くの欠陥にはこの逆も成り立ちますが、低周波の精査は感受性が弱いため、鋭さと届く距離を上手く両立させるバランスが存在します。
この浸透率の可変性の度合いは、供試体の表面に平行である非導電の部品や、領域内の欠陥の発見が不可能である点などの他の問題により増加します。しかし、当試験は準備も速く簡単で、単一パスで利用可能な結果をもたらします。また、対象物の内部の中を深く調べることもできるため、複雑に設計された製品の検査に最適となっています。
磁粉探傷試験
電流を基にした非破壊検査には、もう一つの形態があります。それが、磁粉探傷試験(Magnetic Particle NDT、MT)です。渦電流探傷試験と同様に、磁粉探傷試験では電流が流れている表面の欠陥の検出を行いますが、その代わり、鉄、ニッケル、コバルトなどの強磁性の材料のみに適用できます。
他の試験方法と比較して、磁粉探傷試験は数多くの利点を持っています。携帯性が高く、安価で準備も素早くできるだけでなく、上塗りを施した材料であっても、浅い表面レベルでの細かい亀裂の検知に適しています。しかし、サイズや形状、材料、及び磁場配向に制限があります。同様に、製品の奥深くに存在する欠陥の発見には力が及ばない場合があり、大量の電流により対処しようとすると、部分的な焼けに繋がる恐れもあります。
キーポイント
渦電流探傷試験、及び磁粉探傷試験は、製品に潜在する問題点を明らかにするために電流内の損傷の測定を行う、二つの異なる方法です。
アコースティック・エミッション
非破壊検査は非破壊ではありますが、非接触であるとは限りません。その過程で供試体にセンサーを取り付ける必要のあるアコースティック・エミッション(Acoustic Emission NDT)を例に取りましょう。部品の中にはその上で音波が放射され、センサーは受信した『応力波』すべてを検出します。以上の波の波長は高圧、もしくは高荷重を示し、完全性によりその強度は向上します。
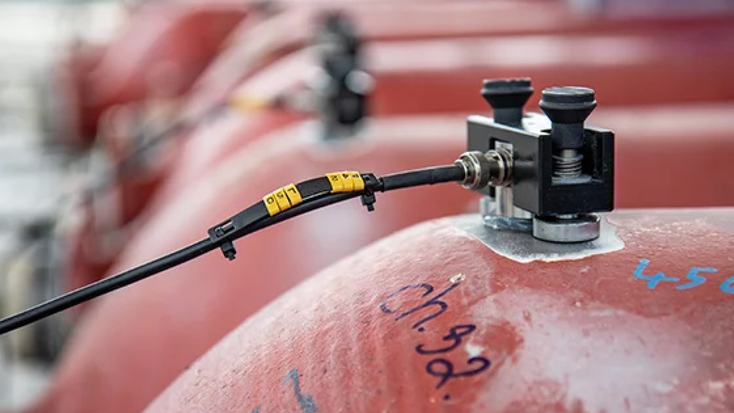
画像元:Shutterstock
アコースティック・エミッションでは単に部品に振動を与えるだけなので、この手法では機器の稼働を中断させる必要は生じません。製品は使用中、もしくは開発途上での試験によっても検査をすることが可能です。また、極めて多目的に利用でき、腐食から繊維破損までのあらゆる事象を検知することができ、厳しい環境下での遠距離からの検査も可能です。
これに対し、アコースティック・エミッションは静的な欠陥検出、並びに発見に限定されます。経時的に発達した欠陥の診断、及び修復のための更なる分析が必要となることも多く生じます。
浸透探傷試験
実際には、浸透探傷試験(Dye Penetrant NDT)では孔を持たない供試体の表面に液体染料が施され、染料は内部に存在する可能性のある穴や割れに浸透していきます。続く検査の中で欠陥を目立たせるため、様々な色を持つ現像液も利用できます。
多孔質、弾性、もしくは海綿状の部品は通常、この手法では検査ができません。浸透探傷試験は従来、鋼や鉄の部品の診断に利用されていましたが、可塑性樹脂、ガラス、及びセラミックへと、新たな用途への導入が継続的に起こっています。 低コスト性、簡素性、並びに隠れた溝状の部分を発見できる性能により、この試験過程は特に鍛造、鋳造、及び溶接の検査において普及するようになりました。
しかし、利用可能な結果を得るためには、前もっての洗浄が不可欠です。浸透剤は有害な化学薬品が原料であることも多く、この非破壊検査手法を手間や経費のかかるものとしています。
キーポイント
浸透探傷試験のような手法は非接触性ですが、検査中に欠陥を迅速に、簡単に特定することが可能です。
リークテスト
リークテスト(Leak Testing NDT、漏れ試験)はある程度、その名前から皆様が想像されるような形で機能する非破壊検査の一つの形態です。対象の装置にはリークテストの間、外部が損傷していないか、そして期待通りの生産量をあげているかを確認するために力が加えられ、圧力・吸引が行われます。興味深いことに、この過程は『その場で』実行され、視覚的な検査を容易なものとする指示薬の液体が加えられます。
この技法自体は、かなり多様なものでもあります。圧力の確認には単なる泡から放射性ガスまであらゆるものが利用可能であるため、食品包装工場、電子機器工場、あるいは石油ガス施設など、漏れがある可能性のある箇所なら何処へでも適用が可能です。もちろん、特定の試験用ガスを利用する場合、表面に施される液体による汚染の可能性があるため、多くの安全面での問題点を考慮すべきとなりますが、結果の信頼性は向上します。
3Dスキャニング
従来の非破壊検査の手法に比べ、3Dスキャニングは表面下の形状のキャプチャには向いていませんが、非常に柔軟性が高く、正確で高精度であり、このすべての点は検査には非常に重要です。Artec Leoのようなワイヤレスでターゲット不要のスキャナは完全に非接触性で高い機動性も持ち合わせているため、どんな場所でも利用可能で、ケーブルも不要な上、汚染の恐れもありません。
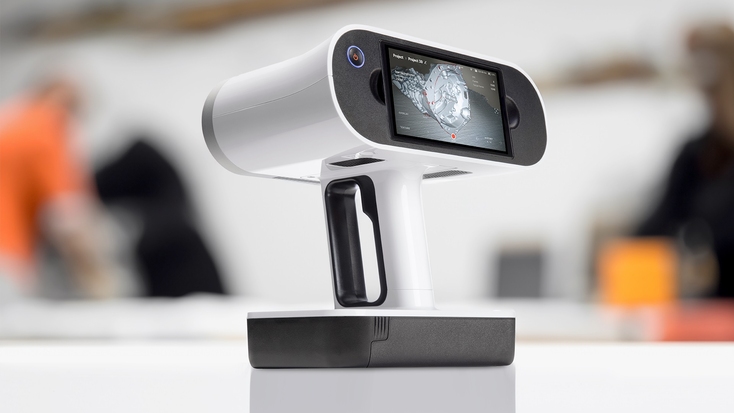
最高で数ミクロンの精度を持ち、スキャン範囲も数百メートルに及ぶ3Dスキャニングは用途の規模にも左右されません。 極めて小さいパーツやより大きな構造物であっても、それぞれのニーズに合ったスキャニング技術が存在します。100%完全なデータセットが必要な場合には、完璧な3Dモデルを数分のうちに作成できる内蔵ディスプレイを有した全自動の機器も用意されています。
実際、適合したハイエンドのソフトウェアが無ければ、3Dスキャナを持っている意味はありません。幸いにも、Artec Studioのようなプログラムは進化を続けており、データ品質のキャプチャの向上と追加された機能による新たな用途の発掘の両方を可能としています。例えば、HDモードは細い線や形状の複雑なサーフェスの驚くべき解像度でのキャプチャを可能とします。内蔵の計測・分析ツールも、デジタル化と検査を一つのプラットフォームでまとめた形での実行を実現の方向へ次第に近づけています。

キーポイント
3Dスキャニングでは非接触型データキャプチャ、拡張性、高精度、超高速性が独自に融合された形で機能し、この手法を産業分野での検査への利用に理想的なものとしています。
用途
石油ガス
石油ガス産業においては、パイプラインの破損は極めて普通に起こります。大事なのは、更なる損傷、環境問題、及び処理能力の断絶の可能性を最小限に抑えるために、できる限り速く復旧を行うことです。非破壊検査は亀裂や腐食を早急、正確、そして早期に発見することを可能とするため、この場合に非常に重要な役割を果たします。
Team, Inc.は破損した導管そのもの周辺のジオメトリのキャプチャに、Artec Leoをご利用になっています。同社のエンジニアの方々はその上で遠距離から特別注文のパイプクランプを製作し、現地での迅速な修復のために利用されています。
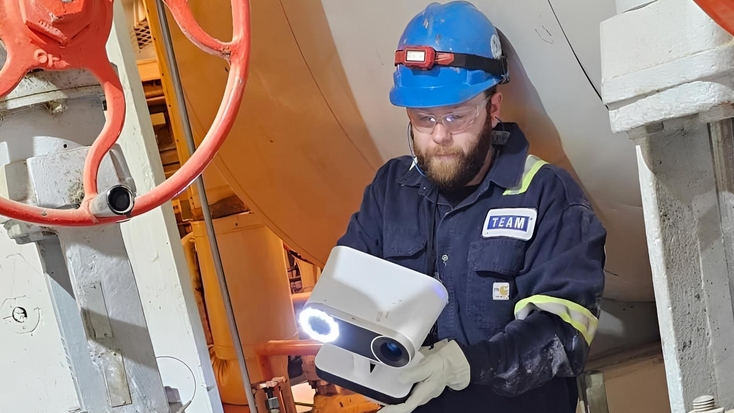
建設
非破壊検査のことを考慮する際には真っ先に頭に浮かぶ用途ではないかもしれませんが、建設業、及び土木工学は大規模な検査の好例です。道路や橋梁、及びトンネルのような生活の基礎となる設備の問題点の特定及び対処は、公共の安全において必須となります。
幸運にも、GoMeasure3D社のような企業が既にそのような業務に携わっています。長距離LiDARスキャナのArtec Ray IIとArtec Leoのご併用により、同社の担当班の方々はアメリカリッチモンド市にある高さ二十五フィートの防水壁の検査を可能とする方法を実践されました。Voestalpine社も同様の線路の検査用ワークフローをご利用になり、この事例では機能停止を防ぐための膨大な数の線路の欠陥が明らかになりました。
キーポイント
非破壊検査は道路や橋梁、及びトンネルのような公共インフラストラクチャーの状態の監視に最適です。
自動車
自動車産業においては非破壊検査は少し違った形で利用されていますが、それでも車両が工場から出荷された時点で安全で信頼性のあることを確認するには不可欠となっています。車のフレーム及びシャシーは溶接により製造、修理、改造されることがよくあり、その接着の状態には確認が必要です。
自動車の製造ライン全般においても、非破壊検査は品質管理のために様々な段階で利用されています。この用途には、エンジンの部品のような鋳造で作成されるパーツにおける欠陥の発見、タイヤや懸架装置が道路で走る準備ができているかを確認する綿密な調査などが含まれます。
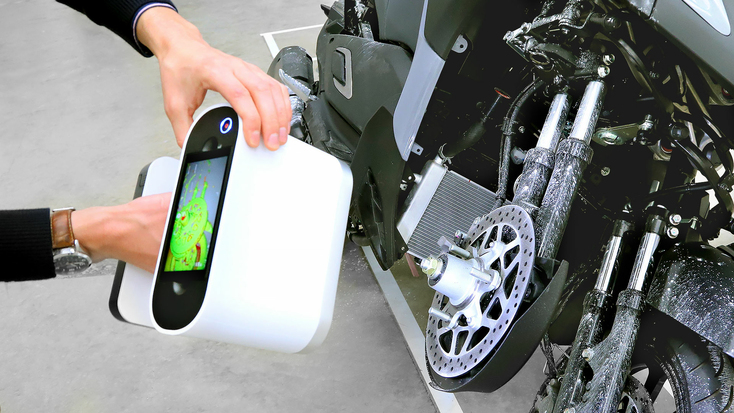
航空宇宙
用途が民間、軍事のいずれであっても、すべての航空宇宙分野の部品は、その耐飛行性の証明のために要求の厳しい業界基準に適合する必要があります。翼、機体、着陸装置などの構成要素には大きな圧力や気温変動に持ちこたえる性能が必要です。そのような場合、ミリメートル単位以下の偏差でさえも重大な結果に繋がる恐れがあります。
だからこそ、製造業者の方の中には、検査やリバースエンジニアリングのために3Dスキャニングのような技術に頼る方がいらっしゃるのです。例えば、3DMakerWorld社は注文を受けたパーツの作成を行おうとしていた顧客の方のために、実験的航空機サドラーバンパイアのの3Dモデルを製作されました。
製造
非破壊検査は品質検査において製造業全般で非常によく利用されており、我々が考える用途の中ではほぼ間違いなく、最も普及していると言えます。鋳造、鍛造、及び溶接はすべて、工場の生産現場で利用される前に検査が必要です。外部から持ち込まれる機械加工部品、塗料、及び原材料に至るまで、仕様に合致することを確認するためには検査が必要です。
そのため、特定の個々の製造業への非破壊検査の導入へ着手することが難しい場合もありますが、前述したような手法の多くは広く利用されています。例を一つ挙げると、Element社は予備の採掘用部品の検査用に、実績のある高精度のArtec Evaを配備しています。
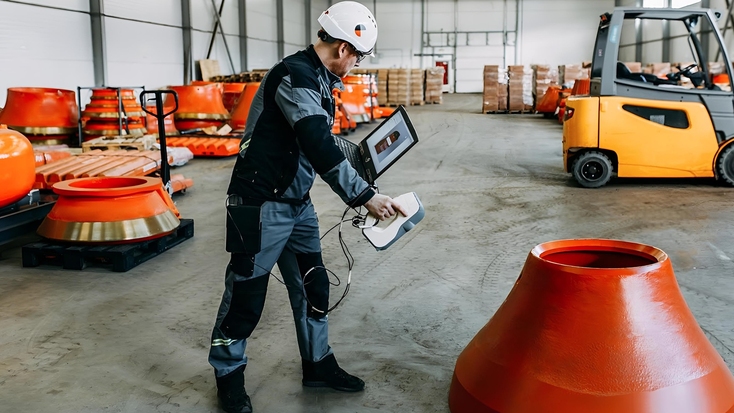
キーポイント
多くの製造業者の方々は、ミリメートル単位以下の精度を持つ3Dスキャニングを従来の非破壊検査方法の代わりとして既にご利用になっています。
エネルギー
非破壊検査の極めて重要な用途の最後を締めくくるのは、電力産業分野でのものです。巨大なタービン翼や発電機のローターのことを思い浮かべてください。その多くは亀裂を生じやすいのです。発電所は、定期的な維持管理の必要な管網が多く利用されている場所でもあります。非破壊検査は、このような領域などで常にすべてが安全で正常に機能するためには必要不可欠なのです。