‘Cloning’ Oscar-winner Jamie Foxx with Artec 3D scanning for a Netflix hit
Challenge: Making a full-body double of Hollywood superstar Jamie Foxx for Netflix film They Cloned Tyrone to deadline, without subjecting the actor to invasive, time-consuming lifecasting.
Solution: Artec Eva, Artec Space Spider, Artec Studio, ZBrush
Result: A clone indistinguishable from Foxx himself, right down to tiny facial features like pores, wrinkles, and birthmarks, which seamlessly takes the actor’s place in several of the movie’s scenes.
Why Artec 3D?: Artec Eva & Space Spider are so easy to use, newcomers can get to grips with them in under two hours. While silicone lifecasting takes many hours to finish – even with 4-6 people on the job – Artec 3D scanning captures complete, lifelike full-body scans in minutes.
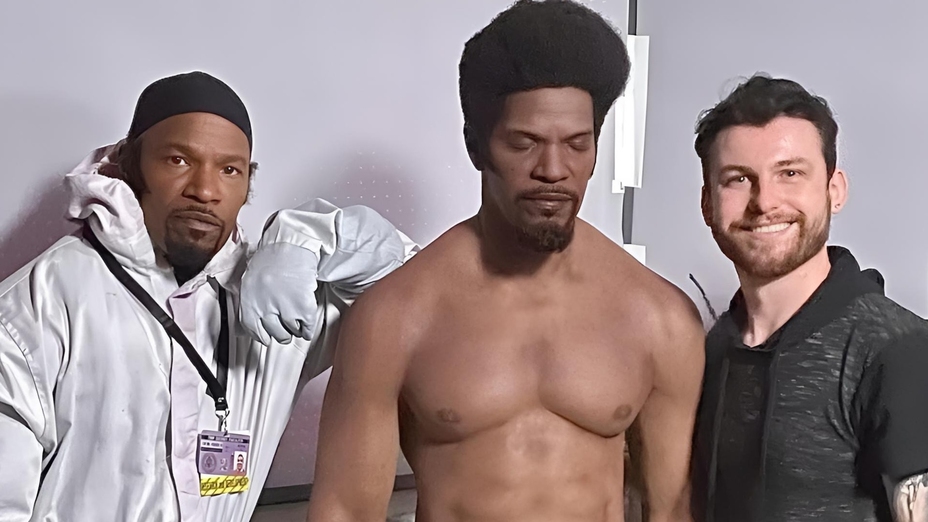
The real Jamie Foxx (left) posing with his clone (center) and Blue Whale Studios Shop Supervisor Anthony Canonica (right) during shooting. Image courtesy of Blue Whale Studios
Movie & TV visual effects have come on in leaps and bounds over the years. While the industry still relies on tried-and-true techniques to change an actor’s appearance using silicone or foam latex prosthetics, technological advances continue to unlock new possibilities, and allow directors to better realize their creative visions.
Take twinning: a fun concept at the heart of many Hollywood blockbusters. From Will Smith in Gemini Man to Tom Hardy’s portrayal of the Kray twins in Legend, the big screen continues to be filled with films that revolve around twins of A-listers, made using digital trickery.
But what if you need to create a physical, full-body double that’s a complete one-for-one replica, for situations like dangerous stunts or scenes where actors appear alongside themselves?
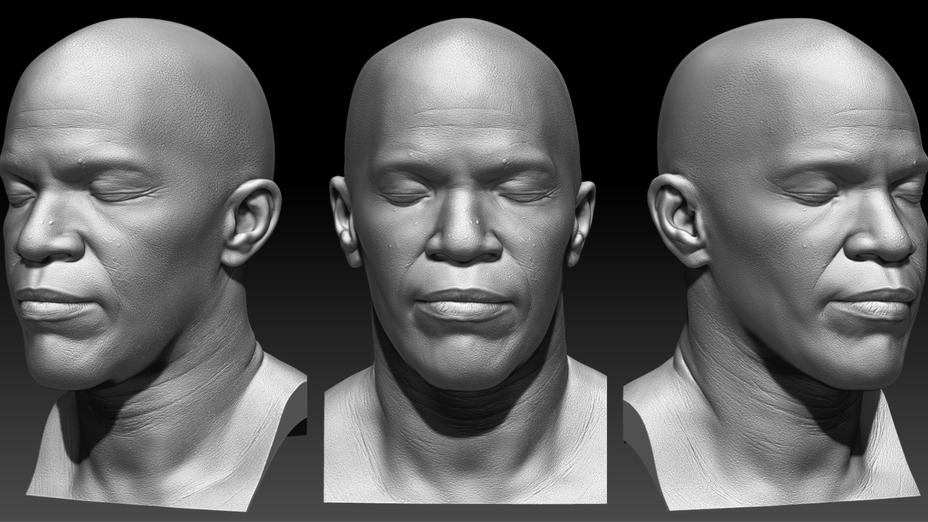
A digital model of Hollywood icon Jamie Foxx’s face – captured with Artec 3D scanning. Image courtesy of Blue Whale Studios
Ordinarily, these would be made by lifecasting an actor, a process that sees them immersed in silicone to create the impressions required for duplication. However, the process is pretty invasive, uncomfortable, and requires many hours of labor. With studios working to tight deadlines amid intense competition, there’s also a constant drive for innovation in this area – and that’s exactly what’s happening at Blue Whale Studios.
Using Artec 3D scanning, the specialty makeup, prop, and costume maker can now turn up at sets, quickly capture actors’ anatomies in high detail, and create ‘clones’ on demand.
Digitizing Jamie Foxx at his LA home
When Blue Whale got the nod to create multiple ‘clones’ of actors Jamie Foxx and John Boyega, several clone ‘children,’ and extensive old-age makeup effects for They Cloned Tyrone, they were faced with a huge challenge. One of the first major obstacles they faced was getting Foxx’s full likeness, as he was reluctant to undergo silicone casting.
This was understandable when you consider the project’s timing. It was one of Blue Whale’s first big jobs since Covid-19 restrictions eased, so social distancing was still on people’s minds.
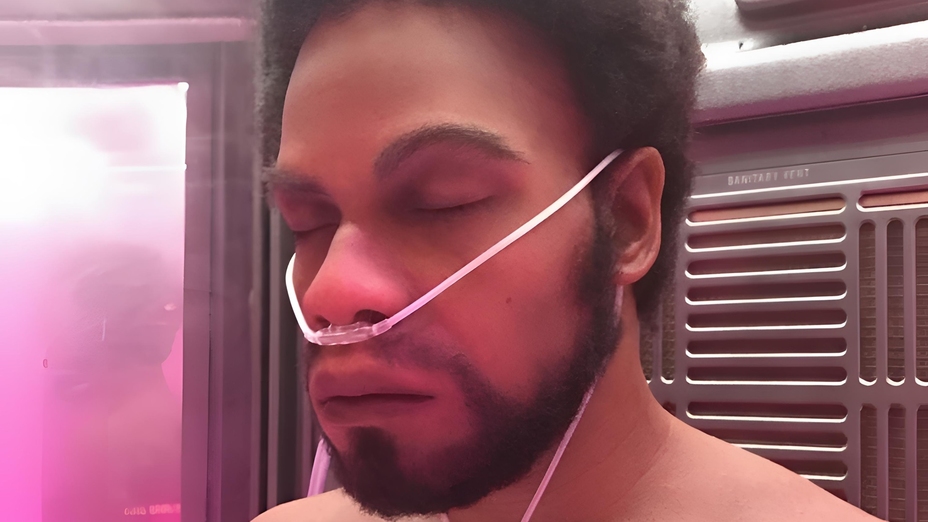
A 3D-scan-based clone of John Boyega in They Cloned Tyrone. Image courtesy of Blue Whale Studios
Seeking a non-contact alternative, the firm initially considered getting a photogrammetry booth, but a lack of portability meant the idea was a non-starter. That’s why the team reached out to Artec 3D Ambassador Digitize Designs, who gave them a live-action demo of the handheld, versatile Artec Eva & Artec Space Spider. Without any editing, demo scans already looked incredible, leaving Blue Whale in no doubt about the scanners’ VFX suitability.
“Straight away, when I got the call from Jonah, I knew this would be the perfect project for a high-resolution scanner like Space Spider,” said Digitize Designs 3D scanning expert Bo Helmrich. “To demonstrate just how easily it creates true-to-life models, I scanned my partner right there and then. I shared the results and without any touching up whatsoever, the scan looked amazing!”
Soon after acquiring the devices, Blue Whale’s Emmy-nominated founder Jonah Levy flew them out to Foxx’s LA home to digitize the star in his living room. Despite never having used 3D scanning in practice, Levy found he could immediately digitize the actor’s body with the fast Eva, then pick up fine facial details using the high-resolution Space Spider.
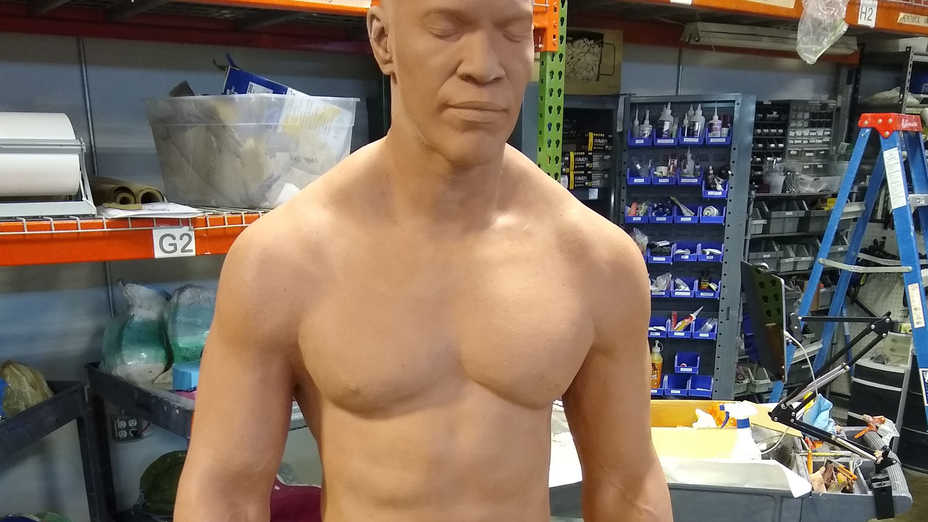
Jamie Foxx’s clone replicated in clay, before Blue Whale artists had provided the finishing touches. Image courtesy of Blue Whale Studios
Powered by Artec Studio, Artec 3D’s data capture and processing software, both benefit from 3D Radar, an intuitive mode that helped him stay in the optimal capture zone. Levy’s efforts were further aided by real-time feedback provided on-screen, which allowed him to capture all the data needed and more, in what turned out to be a very time-limited encounter.
“I come from a traditional sculpting background, so initially it was a challenge,” admitted Levy. “But it turned out great. For him [Foxx], not having to go under silicone and plaster bandages made it easy. Near the end, we also got word that somebody in his crew was Covid-positive, so he got into his car and split. I said, ‘I guess we’re done, it’s a good job we got all the data!’”
“Now we have a better flow. But for it to go so well in the preliminary stages was great, and we ended up with this amazing end-product.”
Creating an incredibly detailed clone
After data capture, Levy sent scans to Blue Whale’s lead digital artist Eric Jarman, who could immediately start using Artec Studio’s editing tools to remove outliers and create a watertight mesh. This near-perfect twin was the ideal starting point for sculpting on 3D design software ZBrush, where he says it was a case of “greasing the skids and getting the model over the line.”
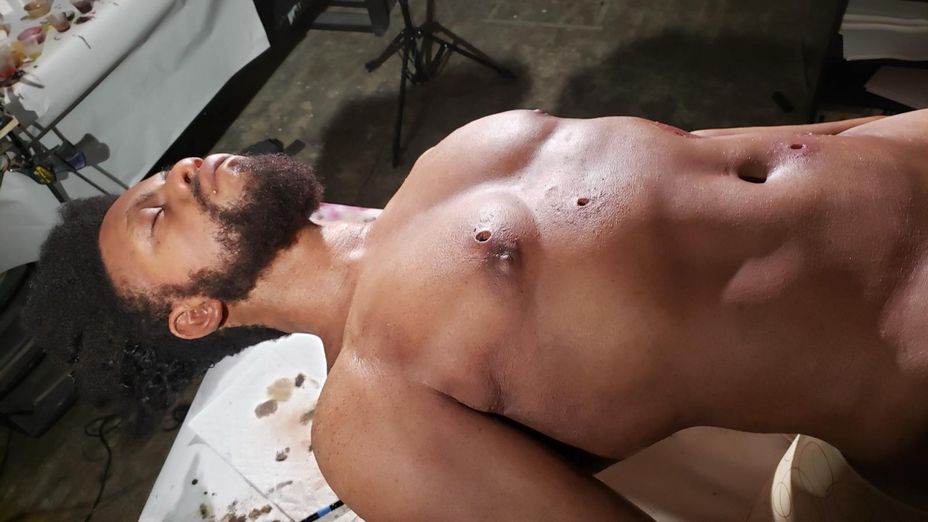
(Spoilers) an ‘injured’ clone of the film’s lead actor, John Boyega. Image courtesy of Blue Whale Studios
Once polished, Jarman sent this file to 3D printer manufacturer Massivit, who created a working model for molding and clay casting. From there, the studio’s sculptors could apply the finishing touches, including multi-layered ultra-realistic painting techniques that made it appear lifelike on-camera, before molding and turning it into a silicone clone complete with hair meticulously punched by the late Denis Lebaer.
This process yielded a replica so realistic, it could even take Foxx’s place at different points in the movie inside a cryogenic tube. Also used to create mockups for approval, Jarman says Artec 3D scanning has streamlined the studio’s production workflow, superseded actor casting, and opened new routes to innovation.
“Artec 3D scanning just integrates so well into our existing workflow,” added Jarman. “Having these tools where we can immediately jump into a digital space, bring it all into ZBrush, and start designing things is so much faster. Traditionally, we’d take a lifecast and do a plaster casting of that. Now we can just go straight to source, it’s incredibly efficient and much more comfortable for our talent.”
Comparing clones made with lifecasting and 3D scanning is like “night and day,” adds Levy, with the latter featuring natural gravity-held skin, higher pore texture, and “exquisite detail.”
Keeping up with Hollywood trends
With the film getting overwhelmingly positive reviews, clearly, viewers are fans of Blue Whale’s Makeup FX too. But the studio isn’t stopping there, it’s already integrating scanning into the design of facial prosthetics, props, molded-then-scaled hand models, and 3D-printed molds.
Since it first adopted the technology, Artec Studio has also taken a huge step forward, bringing in workflow-enhancing features, which the firm intends to integrate with the help of Digitize Designs. For instance, instead of manually combining Eva & Space Spider scans, it’s now possible to fuse them in a single step and build models with the highest-resolution data from each.
More broadly, VFX techniques are constantly evolving to deliver greater realism at ever-lower costs and lead times. That’s why Levy insists that studios “have to find ways to adapt, expand our skills, and be willing to take on new technology.” Otherwise, he says they face being “left in the dust” by competitors, just like industry forerunners who stuck with wax and cotton prosthetics.
“We’re working against the best sculptors in the world – but they do things in an analog fashion,” concluded Levy. “So, it becomes a question of ‘can I do this faster, more efficiently, and cost-effectively with 3D scanning?’ On all three fronts, it’s a definite yes. I don’t see how else we could achieve the same results. It has been an absolute game-changer.”
Adopting Artec 3D scanning is enabling Blue Whale to stay ahead of the curve, do away with ‘artist’s eye’ clay sculpting, and bring clones with unprecedented realism to the big screen.
Scanners behind the story
Try out the world's leading handheld 3D scanners.