Customizing prosthetics for patients in remote areas of Rwanda with Artec Leo
Challenge: Finding a faster, less invasive way of measuring patients’ limbs in difficult-to-access areas of Rwanda, and fitting them with custom prosthetics.
Solution: Artec Leo, Artec Studio, PROTEOR OrtenShape, 3D printing
Result: A digitized workflow in which prosthetics can be sized, 3D printed, and fitted in a single day – 23 patients already have transfemoral (above knee) devices, and there are plans for hundreds more.
Why Artec 3D?: Artec Leo’s wireless, all-in-one design makes it perfect for measuring patients outside clinical settings with high accuracy, in a way that avoids intrusive plaster casting.

Artec 3D scanning expert Mikhail Korolev showing Handicap International medical staff how to use Artec Leo. Photo by Artec 3D.
Around the globe, around 30 million people need prosthetics or orthotics. However, the World Health Organization (WHO) estimates that 90% of low-income countries don’t have access to the technologies needed to treat these patients, and restore comfort, confidence, and mobility.
Many of those affected live in the developing world, in places like Rwanda, where the scars of the 1994 genocide are still healing, and the healthcare system struggles to meet demand. One of the main issues facing medical practitioners there is transporting patients, of which a large number inhabit isolated areas, to clinics, where they can be given appropriate treatment.
Having overcome similar challenges in neighboring Uganda, NGO Handicap International began formulating a plan two years ago, to bring healthcare directly to Rwandan amputees. Instead of moving people to and from camps or rehabilitation centers for measuring and fitting, this would see end-use prosthetics rapidly 3D printed and attached in a matter of minutes.
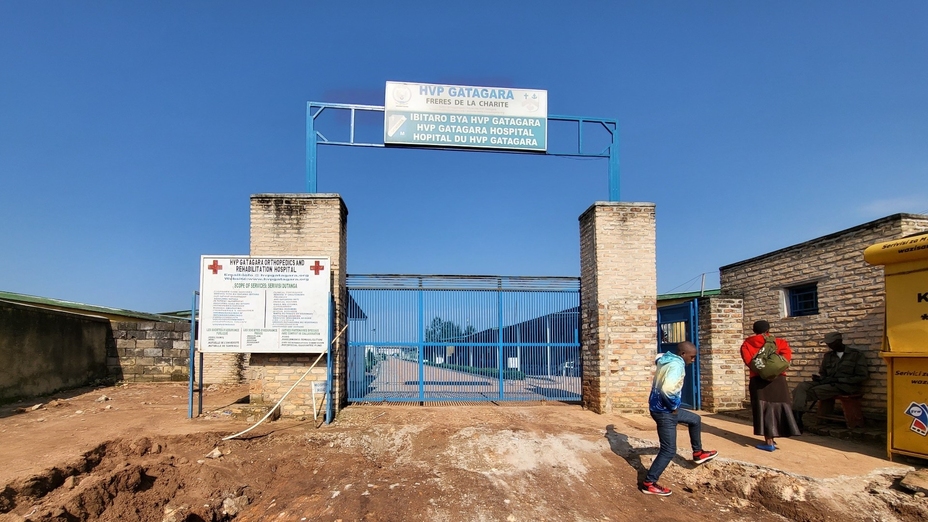
HVP Gatagara – the facility where the Handicap International project is taking place. Photo by Artec 3D.
However, Handicap International still needed to find a faster means of measuring patients that unlocked the full advantages of digital manufacturing. That’s why its team has started working with Artec 3D. Not only has the 3D scanning leader shipped multiple Artec Leo 3D scanners to Handicap International, it has sent experts to train staff, so they can fully harness the technology.
Getting up to speed with Artec Leo
As part of the project, made possible with the backing of Luxembourg’s Directorate for Development Cooperation and Humanitarian Affairs, Artec 3D engineers flew over to provide training in early 2024. Even though the Handicap International team hadn’t used 3D scanning before, Leo’s wireless nature and built-in display made it quick and easy to master.
After five short days, the team found they could rapidly capture all the data needed and pass a troubleshooting test to prove they were ready to start customizing prosthetics.
“When they used Leo for the first time, they thought they had to be slow and steady. But after just a few days they realized they could use it like a painting brush to ‘paint’ 3D models,” explained Artec 3D project expert Jerry Klein. “They could start to scan immediately, and I saw it in their eyes, they were so impressed with how easy it was!”
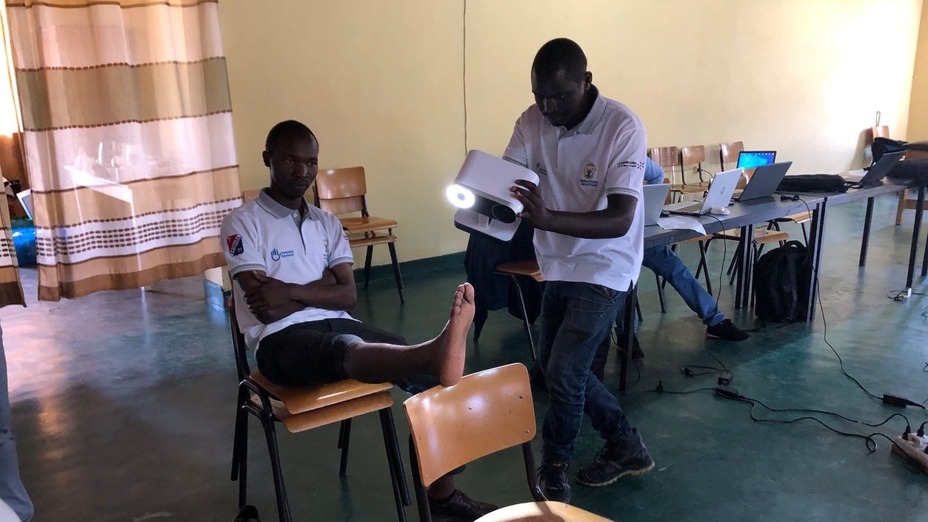
Handicap International medical staff practicing lower leg capture with the Artec Leo 3D scanner. Photo by Artec 3D.
Robert Clement Hakorimana, Technical Manager of the project, reserved particular praise for Leo’s real-time tracking and incredible 0.1mm accuracy. In fact, during trials, he could see virtually no deviation between scan and tape-based measurements, and was left stunned by the quality of resulting models “that looked exactly like real limbs.”
Compared to a previous two-day process of manually making, modifying, and shipping plaster casts for manufacture, 3D printing has proven much simpler, cutting lead times in half. Going digital has also made measurement easier for patients, leading Hakorimana to call contact-free 3D scanning “better at respecting privacy,” particularly when capturing sensitive areas.
3D printing transfemoral prosthetics
Since this initial training session, the project has gone from strength to strength, with the team establishing in-house 3D printing capabilities and starting to treat patients in-need. For their first batch of prosthetics, the medical staff have chosen to tailor transfemoral devices – those designed to restore limbs amputated above the knee joint.
To make these prosthetics, they started by capturing patients’ residual limbs and creating a watertight 3D model inside Artec Studio. After removing surface artifacts using the software’s smart Defeature brush, they moved on to hole-filling, and eventually mesh simplification (to reduce poly-count and make models easier to work with in other programs).
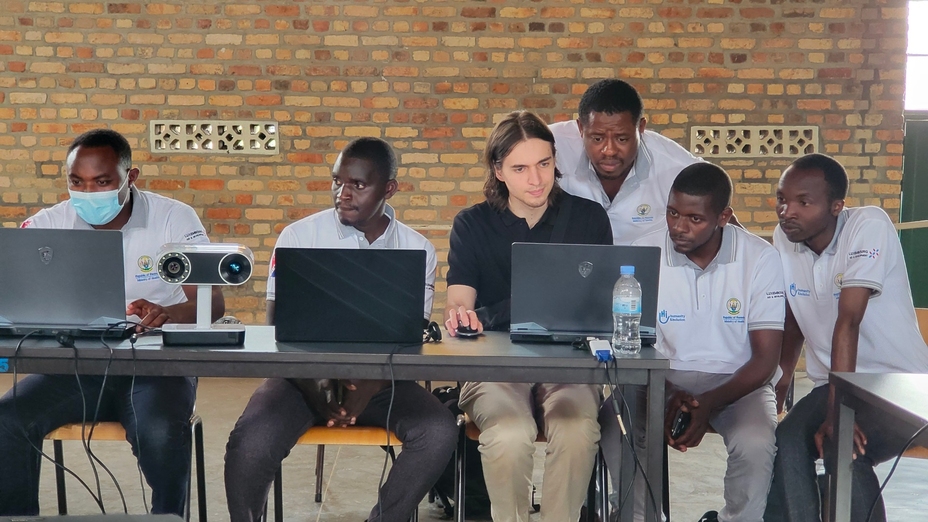
Artec 3D scanning expert Mikhail Korolev and the Handicap International team editing their 3D scan data in Artec Studio. Photo by Artec 3D.
Klein and his Artec colleagues also showed the team how to create molds by adding a cube geometry and removing anatomy scans of arms or feet from the solid shape. But, in this case, it was only necessary to check measurements with point-to-point deviation mapping, and export their polished model to the OrtenShape software for conversion into a 3D printable prosthetic.
Leveraging this free-to-use medical design software, the team are able to adjust the geometry of devices, so they better fit individual anatomies. Where patients have large concentrations of soft tissue, for example, they can remove prosthetic material. Adding material around bony areas like joints, on the other hand, helps prevent painful rubbing during movement.
Altogether, limb capture and device design take less than two hours, while 3D printing can be carried out overnight, so each morning a fresh batch of products are ready for patient fitting.
“We 3D print transfemoral sockets day and night, so they’re ready to go in the morning,” added Hakorimana. “As our design features a built-in connector, you can fit devices immediately – there’s no need for drilling, the shape is already there. Once the print is ready, we can connect the knee joint and give patients a prosthetic in just 30 minutes.”
Aiming to help more patients
Handicap International’s team has already changed the lives of 23 patients with prosthetics that have restored their ability to walk and carry out daily activities unaided. But they’re not stopping there. They continue to improve upon their prosthetic design, and the NGO is working on a way of ‘mirroring’ the appearance of amputees’ healthy limbs for ultra-lifelike prosthetics.
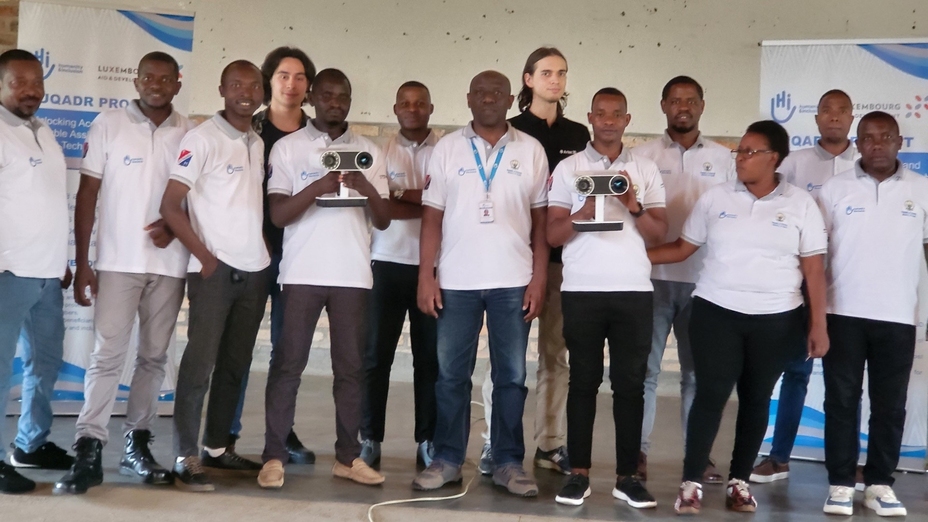
Artec 3D scanning experts Jerry Klein (fourth left) and Mikhail Korolev (sixth right) with the Handicap International. Photo by Artec 3D.
With OrtenShape supporting other prosthetics and orthoses, including ankle, foot, knee, and back braces, Hakorimana and his colleagues are also planning to expand into new areas. More broadly, Artec 3D scanning provides such a catch-all solution, it’s now hoped that local health authorities will pick up the technology, and start making medical devices of their own.
“This technology covers all our prosthetic and orthotic needs,” concluded Hakorimana. “Already, we have invited people from different hospitals to get them using this technology. We’ve also notified the Ministry of Health, so they can make it their own, and help disseminate it across the country.”
Ultimately, the goal is to provide at least 300 patients with much needed prostheses, and the project could serve as a benchmark for what 3D scanning can achieve in the field. In the years to come, the initiative is expected to allow Handicap International to expand the reach of its charity work, so it can more easily aid those living in remote places around the world.
Scanners behind the story
Try out the world's leading handheld 3D scanners.