Sketch-to-CAD workflow cut from weeks to hours with Artec 3D scanning
Challenge: Building upon existing product designs without having access to original CAD data, whether it has been lost, spoiled, or simply isn’t available in a digital format.
Solution: Artec Leo, Artec Space Spider, Artec Studio, Geomagic Design X
Result: Furniture 3D models that feature all the detail necessary for building off surfaces and creating new parts that fit into assemblies. In one case, digitizing a reclining chair linkage in each of its different settings has allowed US furniture giant Kimball to develop parts that slot into a third-party mechanism, as part of a less-than-24-hour process that used to take two weeks.
Why Artec 3D?: Upgrading from robot arm-mounted 3D scanning to Artec Leo, a wireless, all-in-one device, boosts flexibility and unlocks real-time feedback, so users can capture all key details in a single scan. For peak precision, they can also digitize with Artec Space Spider, merge data with Leo scans in Artec Studio, convert to CAD in Design X, and iterate or 3D print.
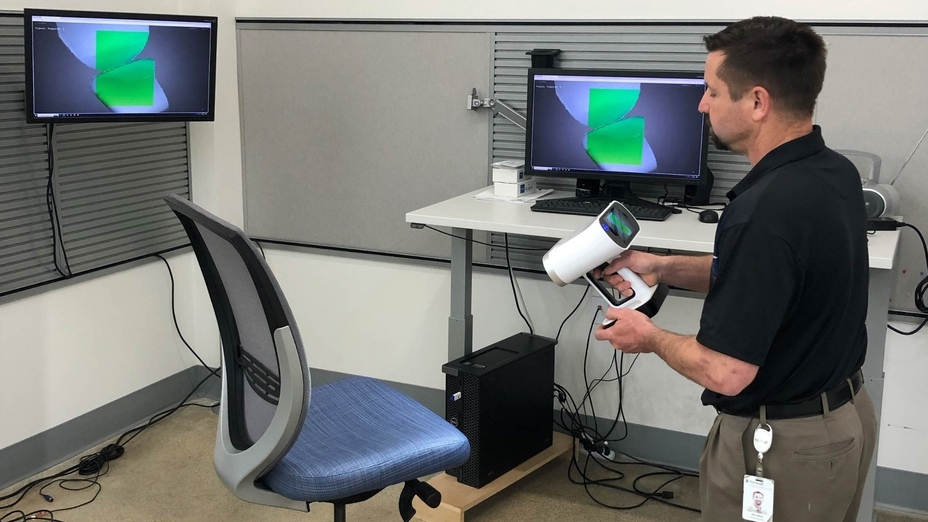
Kimball International’s Alex Mlsna 3D scanning with Artec Leo. Image courtesy of Kimball International
It’s a familiar question for engineers across industries, but it remains a very important one: How do you reverse engineer something when you don’t have its original CAD design data?
This is a particular issue when it comes to heritage parts, some of which predate 3D modeling, meaning they were sketched on paper prone to being scribbled upon or lost altogether. With globalization continuing to make the world a smaller place, manufacturers have also outsourced the production of many parts, in a way that makes seamless design sharing a necessity.
For Kimball International, a workplace, health, education, and hospitality contract furniture manufacturer, these challenges recently came crashing together, threatening to delay a product launch.
During the design of a healthcare recliner, the firm found that it needed to make parts fit around a steel reclining lever assembly created by a third party. This meant that its team needed access to the mechanism’s design files, and while the supplier was happy to share, it did so in the form of a PDF drawing – not the 3D design data required for high-speed iteration.
Accurately digitizing the mechanism in a way that didn’t delay the product launch would require next-level precision, speed, and flexibility. With their existing device not up to the job, the team turned to Artec Leo and Artec Space Spider – and rapidly got a return on their investment.
Slashing lead times with Leo
When Kimball International made its first foray into 3D scanning, it did so with the intention of capturing products without using markers, the application of which is costly and time-consuming. This led its team to adopt a robot arm-mounted laser scanner, and while this captured usable data, the system’s static base limited movement and made it painfully slow.
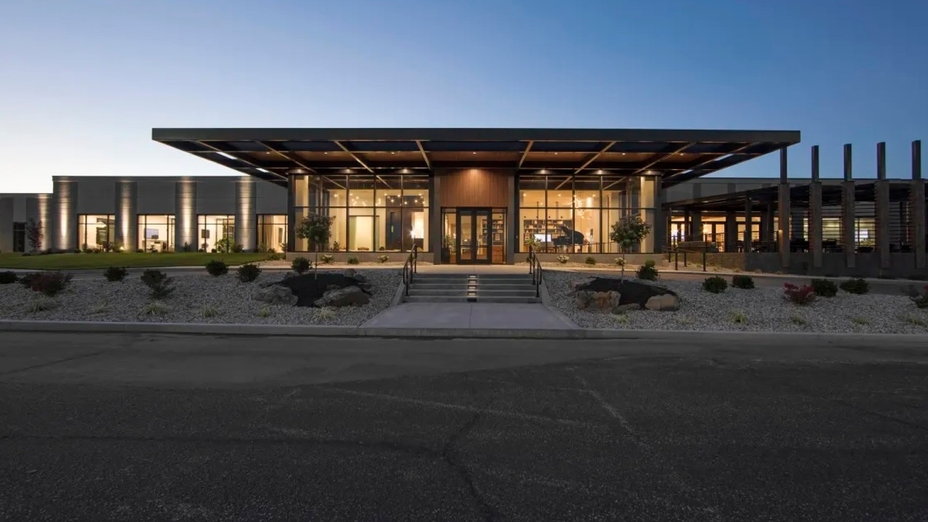
Kimball’s International HQ in Jasper, Indiana. Image courtesy of Kimball International
When they discovered Artec Leo, a completely cable-free device capable of capturing up to 35 million data points per second, they reached out to Digitize Designs right away to upgrade.
Since the Artec Ambassador set the Kimball International team up, they’ve not looked back, meeting all their digitization needs with Artec 3D scanning, and moving arm-scanning into quality control. Not just a speed upgrade, Leo’s advanced tracking and feedback has been key to making efficiency gains – with its medical chair taking under 24 hours to capture and model in full.
“What we really like about Leo is its ability to re-recognize features if you get off-track,” said Kimball International Technical Services Manager, Alex Mlsna. “As it’s wireless, you can also move around and see what you’re scanning in real time. You can even tag it to an IP address, so you see Leo’s display through bigger screens.”
“Initially, we had four meetings with demos, so we’re very picky. But once we saw Artec Leo, it easily beat its three main market competitors to the punch.”
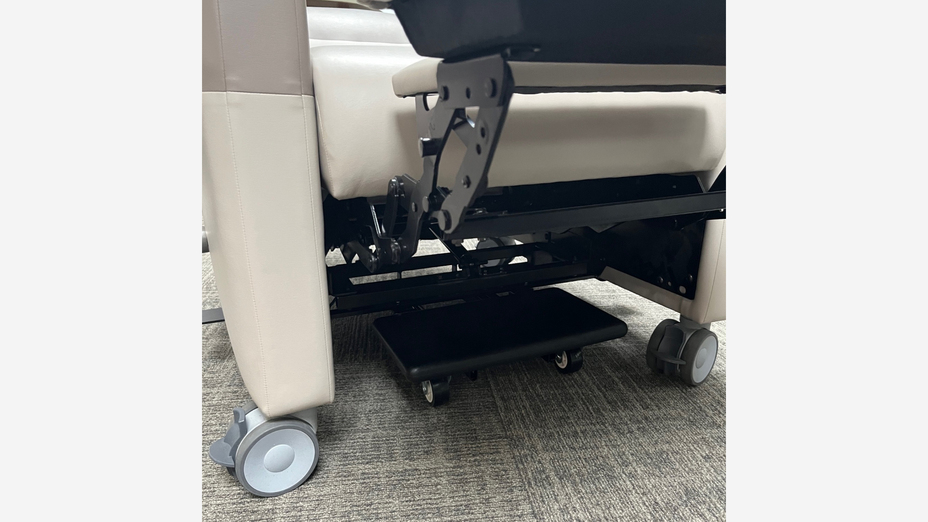
The reclining mechanism on the chair Kimball International 3D scanned. Image courtesy of Kimball International
Kimball International’s facility in Indiana, USA, is also packed with a myriad of other advanced technologies, so it was only a matter of time before talk turned from digitization to 3D printing end-parts.
To achieve this, its design team knew they’d need the most precisely captured data possible. That’s why they also have Artec Space Spider: a metrology-grade, 0.05mm-accuracy device that has allowed them to capture even more detailed, higher-resolution datasets, ideal for 3D modeling and selective laser sintering (SLS) or binder jet 3D printing.
What started out with the 3D printing of factory gauge blocks, fixtures, and replacement tooling has quickly become a key part of Kimball International’s back-of-shop operations. In fact, many prototypes are now 3D printed for durability and structural testing, while the same technology is used to create no fewer than 28 parts of final products sold to customers.
“We knew that we needed something that could capture in even higher resolution and get the smallest fine details, so we snagged a Space Spider,” explained Mlsna. “It has come in handy because we digitize many actual parts, modify them, and then produce them on our 3D machines. There’s not a lot we can’t actually 3D print. Not anything I’ve 3D scanned anyway.”
Getting from Scan-to-CAD
Whether they’ve just used Leo or captured an object with Space Spider too, the Kimball International team’s scan processing workflow starts with global registration, a single-click step on Artec Studio. In cases where they have scans from both devices, this process allows these to be merged into incredibly detailed meshes, made from the highest-resolution data available.
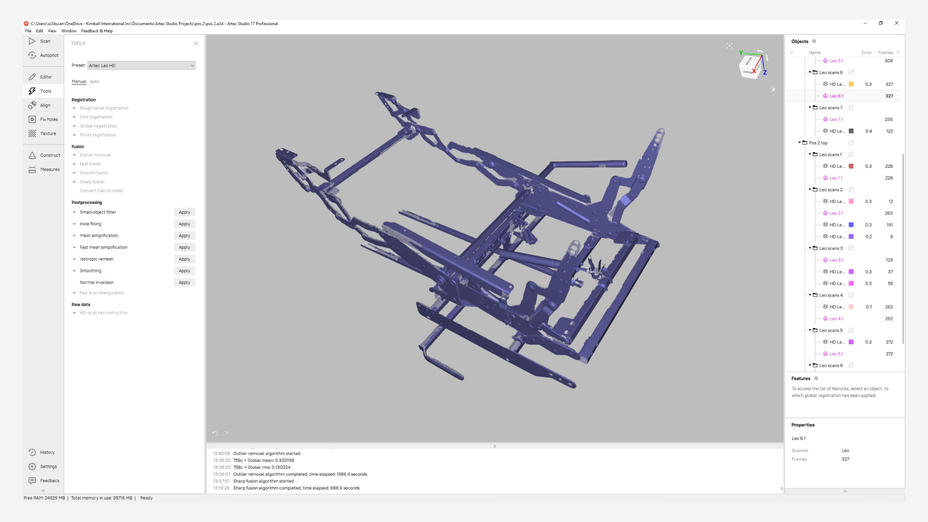
A Kimball reclining medical chair scan on Artec Studio. Image courtesy of Kimball International
To fine-tune these 3D datasets, Mlsna says he previously used Artec Studio’s intuitive Autopilot, which chooses the ideal data processing algorithms on your behalf. As he has got to grips with the software’s nuances, he has increasingly processed data manually, but with there being so little cleanup required it’s usually just a case of sending meshes directly to Geomagic Design X.
The advanced reverse engineering program’s auto-surfacing tools then allow him to create feature-based CAD models and (where necessary) export STL files for 3D printing. While Mlsna had used Design X before, he has been pleasantly surprised by how easy it is to slot Artec 3D scanning into this workflow, and accelerate it – cutting 3D modeling time by 60%.
“Artec Studio does a very good job of post-processing and getting the mesh ready to go into surfacing tools,” said Mlsna. “In the past, I often had to clean stuff up [before export], but now I don’t – which is a real compliment to what Artec does.”
Next up: Modeling manufacturing cells?
With its reclining healthcare chair design having been developed, manufactured, and launched to the marketplace, what next for Kimball’s now 3D scanning-led digitization workflow?
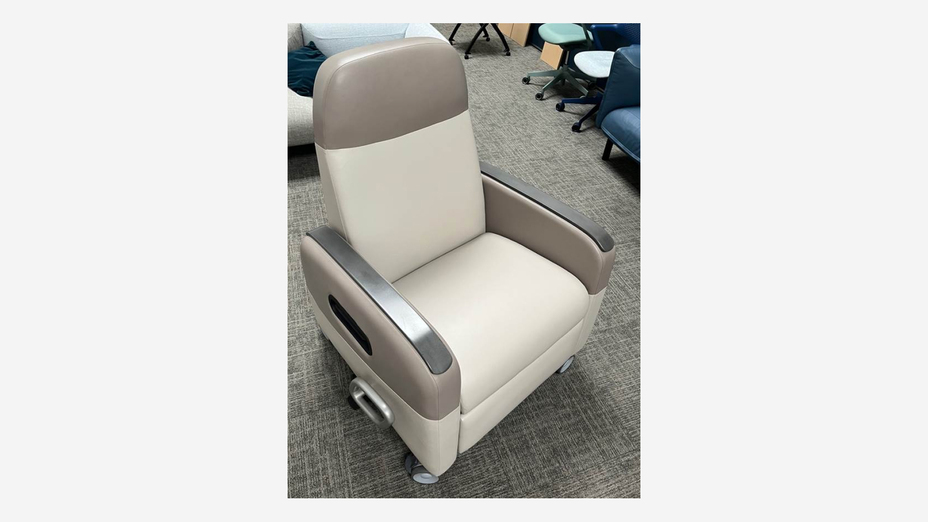
Kimball’s finished reclining healthcare chair. Image courtesy of Kimball International
The company’s product digitization efforts continue to grow, with lifelike 3D representations now featuring in its marketing materials, but it’s also considering expanding into a new area: Workcell design. As this process still tends to rely on 2D CAD layouts, which aren’t great for assessing ergonomics, Mlsna believes it to be another area of opportunity for his firm.
“We haven’t gotten there yet, we could grow into this, but overall Artec 3D scanning has been of great value to us on the output side because we’re not just doing digitization anymore,” concluded Mlsna. “We’re now actually able to help product engineering with something that doesn’t exist from a CAD file standpoint. It’s true reverse engineering.”
Scanners behind the story
Try out the world's leading handheld 3D scanners.