What is CAD?
Computer-aided design or ‘CAD’ programs provide users with a platform on which they can design, edit, and analyze products in 2D or 3D. In many industries, CAD digitized the design process decades ago, consigning manual drafting to the history books. But, with digitized design being so well established, the basics behind it aren’t always well-covered. Advanced technologies like 3D scanning are also making inroads as a way of using existing products as a starting point and avoiding having to design from scratch. To help you get up to speed, let’s take a look at the basics of computer-aided design systems, who invented them, how they work, where they’re used, and how to get on top of emerging trends.
Who invented CAD?
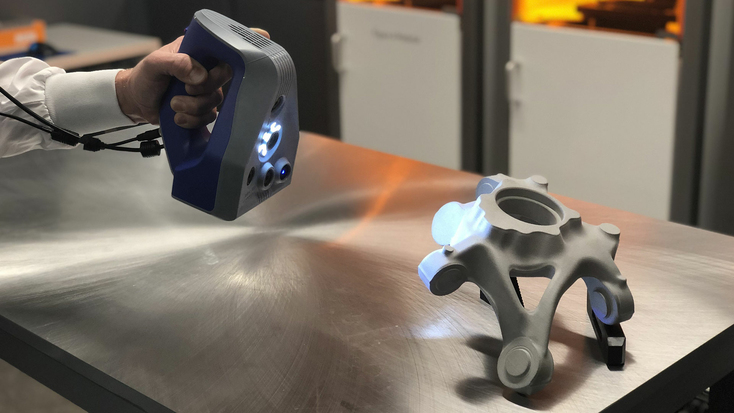
Artec 3D scanning captures with sufficient accuracy for complex CAD design
Computer-aided design is such a cutting-edge and prevalent product iteration tool, you’d be forgiven for thinking it was invented recently. On the contrary, Dr. Patrick Hanratty laid its foundations with ‘PRONTO,’ the first commercial numerical control system, way back in 1957.
Six years later, Ivan Sutherland took things a step further with SketchPad, a breakthrough machine that allowed for the first human-computer interactions. While Sutherland’s device only supported basic elements like arcs and line segments, it allowed mechanical designs to be drawn on-screen like never before, making it a precursor to future CAD systems.
Not long after, firms began to launch their own CAD programs. With code supplied by Hanratty, McDonnell Douglas introduced a computer software for part layout and geometry in 1967. While the company has since disappeared, merging with Boeing, its MicroGDS CAD platform has proven so successful it continues to be used today.
Key point
Despite being around for decades, CAD is still king in product design, and it continues to benefit from new features that bring greater integration with advanced 3D technologies.
Over the decades, CAD has remained a hot topic of research. At Computervision, one of the industry’s main early players, Dr. Ken Versprille developed NURBS (non-uniform rational b-splines) in 1975. Now a 3D modeling mainstay, the feature allows for the creation of complex CAD models with curved surfaces.
Since then, advances like parametric modeling, first commercialized by CREO, have changed the way CAD is utilized – allowing models to be tweaked based on preset parameters. If some features need modifying, for instance, simply adjusting a model’s parameters in initial sketches is enough to recalculate and reshape it entirely.
More recently, CAD technology has also continued converging with 3D printing and 3D scanning, and new features are constantly bringing the technologies closer together.
What is CAD: the key principles
Before we get into the key features of CAD and how best to utilize them, it’s worth clarifying what we mean by ‘CAD software.’ Essentially, that’s all the software programs that provide a digital blank canvas where designs can either be created or dragged, dropped, and edited.
These work differently to scan-to-CAD offerings like 3D scan capture and data processing platform Artec Studio. At its core, scan-to-CAD is the process of 3D scanning an object, then converting it into a model that can be used, modified, and improved upon in other platforms. We’ll cover the workflow later, but for now, it’s worth noting how it allows designers to avoid the need to start from scratch.
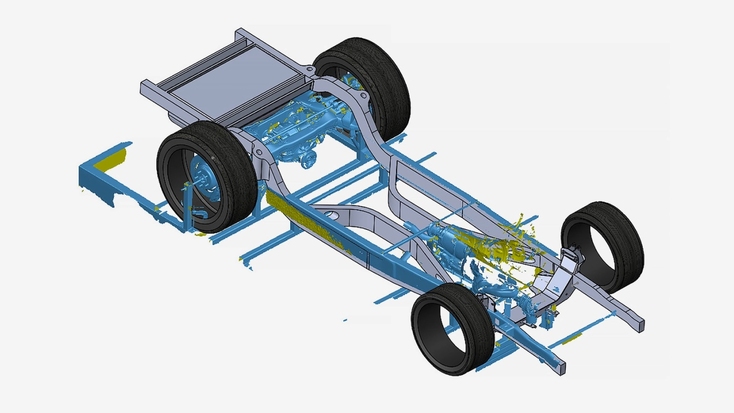
CAD software is utilized across industries for product design and iteration
Then we have computer-aided manufacturing and engineering (CAM/CAE). CAM software is designed to generate the optimal toolpath for machine tools, while CAE relates to simulation for product testing and iteration. As they rely on high-quality digital models, both are intrinsically tied to CAD, so they’re also worth keeping in mind.
Now, even when we narrow things down to CAD software, feature sets can differ drastically between packages, with some being more advanced, and others targeting a specific industry. That said, they all include CAD tools that allow users to craft products from basic shapes, layers, and blocks, by aligning, duplicating, and placing them at exact distances.
Key point
All CAD software – basic or advanced – allows users to create entirely new 3D designs, or import and edit existing ones.
Compared to paid-for platforms, freewares tend to be more stripped-back, with interfaces that don’t change based on what’s happening in the workspace. However, not all free CAD software is feature-light. For example, FreeCAD has the tools needed to carry out complex boolean operations, and many professional programs also offer free versions.
Where you may want to consider upgrading, is if you’re an engineer. Take Autodesk Inventor – with the program’s rendering, simulation, and machine design tools, you can ‘embed’ manufacturing information into models. It also includes finite element analysis (FEA) features that allow you to assess how end-products will perform in certain conditions.
Solid, wireframe & surface modeling
Broadly, the different types of CAD can be broken down into solid, wireframe, and surface modeling. Though other approaches warrant mentioning, most fit into these three categories.
Solid modeling is ideal for assembling primitive shapes like lines, arches, spheres, and cubes into complex models, while maintaining a calculable object volume. This allows designers to constantly validate builds and ensure they can be viably manufactured.
By contrast, wireframe modeling only depicts a model’s edge and corner surfaces, enabling them to be crafted with greater subtlety. On a technical level, this is achieved by representing models as vertices linked by ‘faces,’ which can be modified to change their position and create curved surfaces on an object’s exterior.
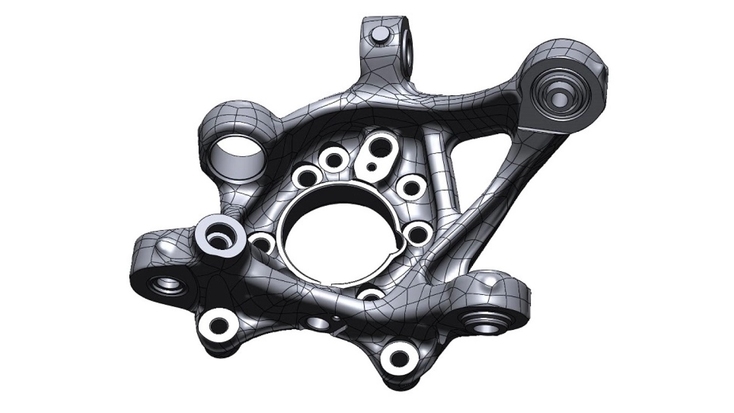
Advances in CAD technology continue to remove design limitations
Lastly, with surface modeling, users can build models via a series of guiding lines or control points. These are then connected to form surfaces by CAD platforms, which calculate the smoothest way of doing so. As you can imagine, this method’s seamless, flowing surface focus makes it ideal for automotive and aerospace modeling – where airflow is key.
Key point
Continued innovation is bringing CAD and 3D scanning closer together and steadily making ‘scan-to-CAD’ easier to achieve.
Other approaches, such as generative design, are threatening to take human error out of the equation altogether. Designers can now charge AI with overcoming design issues, whether these relate to weight, cost, or performance, and it will come up with a solution. All they need to do is enter the parameters they’re working to and algorithms do the rest.
AI isn’t the only advanced technology making waves in CAD. With 3D scanning, it’s now possible to not just automate design steps but eliminate some altogether by digitizing existing products and using them as a basis for future physical prototypes.
Where does 3D scanning fit in?
When it comes to digitizing previous designs, 3D scanning is ideal, as it allows them to be captured in seconds and turned into baselines for iteration.
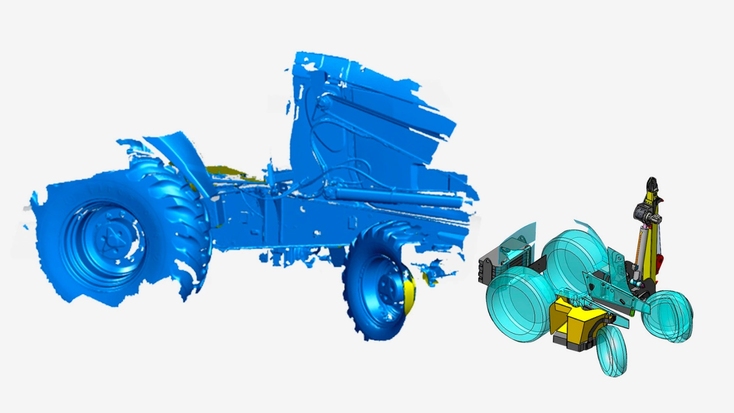
Flexible handheld Artec 3D scanners can capture objects of all shapes and sizes
This makes it much faster than drawing from scratch, physically or via CAD. Of course, doing so can have implications if you don’t own a design, but where firms revamp proprietary products, the process offers a way of expediting prototyping and cutting costs.
Key point
With 3D scanning, product designs can be digitized in seconds, eliminating the entire initial design stage.
Likewise, when it comes to on-demand manufacturing, digitization allows inventory to be managed virtually. Creating CAD versions of old parts stores their designs for future use and allows them to be produced with modern technologies like 3D printing, which can improve their properties.
Where initial electronic files exist, they can be compared to models on many 3D CAD programs, providing users with the ability to identify product defects before launch. Creating objects with freeform surfaces is also easier with 3D scanning than manual design – this is particularly useful for those making custom consumer or healthcare products.
How to get from scan to CAD
So, that’s how 3D scanning fits into 3D CAD design. But what happens once you’ve captured the data you need? Can you just start editing scans on CAD software?
Well, not immediately. First, scans need to be transformed into solid 3D models, and this workflow continues to get easier thanks to advances in the ‘scan-to-CAD’ programs that serve as a bridge between mesh and model.
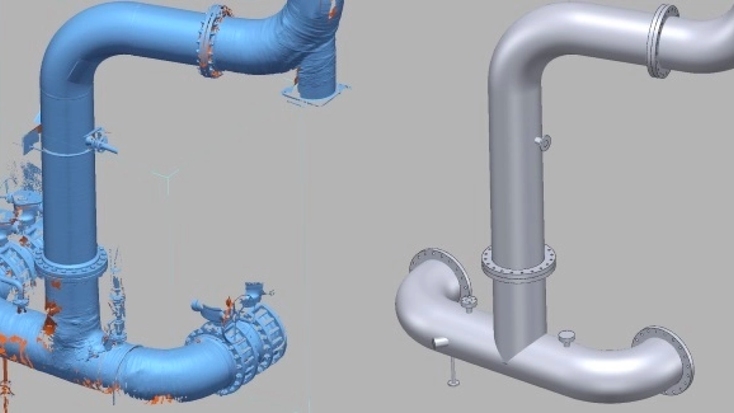
Getting from scan to CAD takes a few steps, but the results speak for themselves
A great platform on which to start this workflow, Artec Studio streamlines scan data capture and processing, simplifying some steps to a single click. Geometry and texture tracking algorithms ensure engineers capture parts in high detail, while the platform’s growing Boolean operations toolkit can be used to enhance meshes e.g. by thickening surfaces likely to break.
Artec Studio gives you everything needed to prepare your mesh and carry out essential reverse engineering tasks. On the platform, you can move & offset faces to make modifications, add polish with chamfer and fillet tools, and create new shapes by adding, subtracting, or intersecting primitives with other models, all in one place.
Programs like Geomagic for SOLIDWORKS expedite the process of turning this highly polished mesh into a CAD model. Plugging directly into your SOLIDWORKS workspace, the add-on gives you the feature extraction tools needed to create solid, editable models from scan data. If you want to quickly, easily, and accurately fix or edit an existing design in a familiar interface, the program represents an ideal Artec Studio companion.
For intensive reverse engineering, leading software Geomagic Design X comes with a more comprehensive scan-to-CAD toolset. With exact surfacing, it’s possible to reconstruct complex freeform shapes, then deploy the platform’s patching feature to instantly add surface bodies, which closely follow object contours and curves.
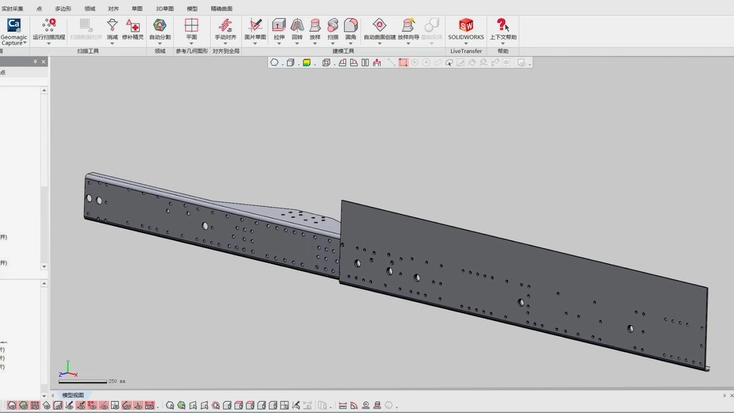
Geomagic develops some of the industry’s leading scan-to-CAD platforms
When it comes to 2D & 3D sketching, Design X offers the perfect basis for rapid scan-based engineering. Auto Sketch can be used to accelerate geometry extraction, and configured to automatically fit shapes to polyline entities, in a way that meets desired parameters. Other tools like Loft and Sweep also make it easy to blend sections into seamless surfaces.
More broadly, there’s now a significant overlap between CAD and scan-to-CAD programs, with many traditional design platforms integrating 3D scan-friendly functionalities. Let’s take a look at some of the most popular, what they offer, and where they’re best used.
Popular CAD software
AutoCAD
Standard version: $1,955 per year
Windows, Mac
- Flexible, industry-agnostic
- Large support/user base
- Tricky to master UI
AutoCAD has the highest install base of any engineering-grade CAD program, and for good reason. It’s packed with features that help architects and mechanical engineers design faster and more efficiently, including those that automate the process of comparing engineering drawings and allow for the creation of custom workspaces.
The CAD software’s comprehensive offering pairs 2D drafting, drawing, and annotation tools with those for designing 3D solid, surface, and mesh models. When it comes to achieving photorealistic renderings, its feature set is also strong, boasting tools for adding lighting or shading effects, and ‘floating’ around them, facilitating product presentations.
AutoCAD also integrates cloud-sharing functionality for collaboration and a feature-rich UI. Though the latter is not particularly user friendly, those who do persevere with it, are rewarded with powerful professional-grade tools for hand drafting and any future editing tasks.
SOLIDWORKS
Available on request
Windows
- Engineering-grade features
- Easy to export CAD files for 3D printing
- Pricier than rival platforms
- Can be CPU intensive
Already mentioned further up, SOLIDWORKS has a vast array of CAD tools for sketching complex surfaces. Over the years, developer Dassault Systèmes has expanded its feature set, launching add-ons, integrating it with other programs, and enhancing its design, simulation, and manufacturing analysis tools, while introducing cloud-sharing.
Additionally, the CAD software’s in-built 3D printer database streamlines model preparation and export for manufacturing, making it a popular choice among the 3D printing community. Where SOLIDWORKS falls down is its value proposition for personal users. If you’re only toying with the technology, it can be difficult to justify a yearly multi-thousand dollar spend.
But, if you’re a professional user working to satisfy a particular business case, its extensive mesh editing toolkit is ideal for reverse engineering, rapid prototyping, industrial design, analysis, and more.
Fusion 360
From $545 per year
Windows, Mac
- Relatively cheap design and engineering tool access
- Can be upgraded with add-ons
- Speed is network-dependent
Fusion 360 does things a little differently to its main rivals, in that it requires regular cloud syncing. Therefore, if you have ambitions of keeping valuable designs off the Internet, it may be best to look elsewhere. Where the platform excels is its balance of usability and affordability, and it has a strong suite of tools for design and creating technical drawings.
More broadly, Autodesk also markets so many design platforms, you’re bound to find one that meets your modeling needs – including CAD software like Autodesk Inventor – which includes more advanced design and analysis tools.
Solid Edge
From $82 per month
Windows
- Lower-cost drafting edition
- Generative design analysis
- Accessible UI
- Light on 3D modeling tools
Seeking a more industrial-grade solution? Siemens’ Solid Edge platform could be it. Pairing basic part and assembly drafting features with an array of design, simulation, manufacturing, and data analysis tools, Solid Edge is ideal for production environments.
Though not essential, as Artec Studio has a comprehensive mesh-tidying CAD toolset, Solid Edge does pack its own drafting innovations, including generative design analytics for identifying topology optimization opportunities. As with other options on this list, Solid Edge also features excellent 3D printing integration, making it easy to utilize for rapid prototyping.
Elsewhere, Siemens offers an entry-level version aimed at design and drafting users, so they won’t have to pay for features they’ll never use. However, this does come at the cost of some functionality, with the platform feeling a little light compared to alternatives like Siemens’ own NX CAD/CAM/CAE software.
Key point
Integration with AI, cloud computing, and 3D scanning is accelerating product design on many CAD platforms.
Beyond this handful of popular programs, there are plenty of others, and not just prosumer engineering platforms either. CAD software like FreeCAD and TinkerCAD offers hobbyist designers and makers all the essentials needed to model for 3D printing, while SketchUp and Blender are more geared towards sketching and rendering.
Check out our best CAD & scan-to-CAD software article to find out more.
Industry-specific CAD applications
Product design
Even though iteration is necessary to ensuring product quality across a range of industries, many of these applications share a common thread: a reliance on CAD. In some areas, initial designs may still be outlined via traditional drafting, but the long, drawn-out iterative sketching processes that delayed the product launches of the past, have largely been shelved.
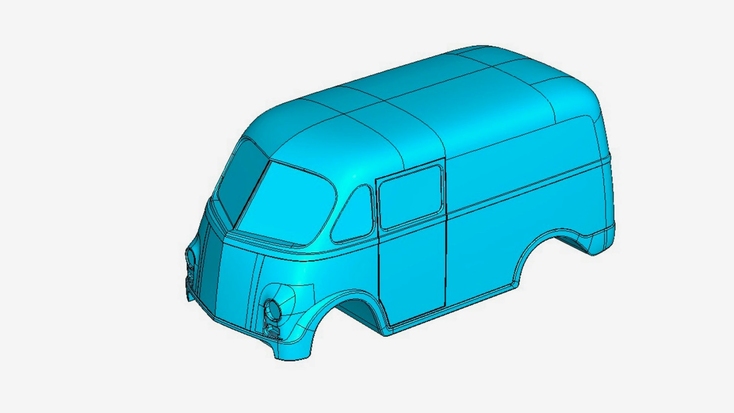
CAD design is even taking over in automotive – where sketching has traditionally flourished
Beyond prototyping speed, the introduction of CAD has helped overcome issues around the misinterpretation and sharing of scaled diagrams. Design digitization and the ubiquity of CAD have also unlocked previously unthinkable levels of automation and collaboration.
The arrival of CAD hasn’t just changed the way products are designed either, it has opened up entirely new avenues. Before, previewing an early design would require a mock-up to be made and shipped. Now, businesses like luxury furnishings firm Sherrill Furniture are able to digitize furniture with 3D scanning in minutes, and use this data to create dozens of CGI lounge items for customization and 3D visualization each week.
This has been made possible by the lightning-fast 35 million pts/s Artec Leo. Featuring click-to-scan functionality and sub-millimeter 3D scanning capabilities, Leo makes capturing intricate, texture-rich items like furniture in crowded showrooms quick and easy – it also unlocks applications elsewhere, as we’ll explore next.
Engineering
CAE is where CAD really comes in handy for mechanical engineers – as a means of analyzing the performance of mechanical parts and assemblies before they go into production. Similarly to product prototyping, this saves manufacturers from having to make wasteful mock-ups as they can simulate how they’ll work instead.
However, engineering requires a completely different simulation toolset. Autodesk has recognized this with Inventor: a platform that pairs hand-drafting essentials with static and modal stress analysis tools for testing if products can withstand set loads.
Key point
CAD allows engineers to ensure parts and assemblies meet application requirements before they ever enter production.
Elsewhere, Siemens offers the Simcenter FLOEFD CAD-embedded computational fluid dynamics (CFD) software. With CFD simulation, it’s possible to predict how fluids like air and water will flow around a model – and by extension – how they can be channeled to make it more aerodynamic. This is particularly important in areas like competitive cycling, where minimizing air resistance is key to finishing first.
Using data captured with Leo and the ultra-precise Artec Space Spider, UK sim firm Vorteq has taken this approach to the next level, building the world’s fastest racing bike. While Leo’s speed and wireless portability accelerated capture for comparative analysis, it was the sheer detail picked up by the 0.1mm-resolution Space Spider that allowed the forces going through the bike’s frame to be modeled using CFD.
With other functionalities like multibody dynamic analysis (for examining how connected bodies behave) also making their way into many platforms, detailed engineering clearly remains one of the most exciting areas in CAD design.
Automotive
In automotive, the artistry behind hand-drawn car designs remains very much alive, only CAD modeling has brought it into the 21st century. The process still tends to begin with sketches, but engineers have begun turning these into virtual designs by digitally drafting them on CAD platforms and using the resulting models to create life-sized prototypes for testing.
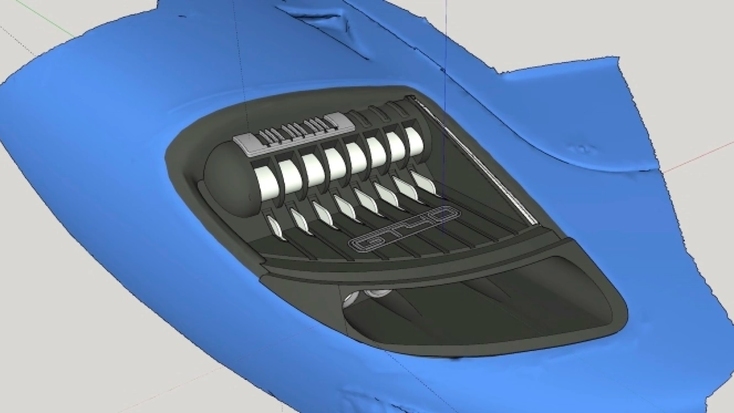
Many tuning firms capture existing models, then digitally design desired upgrades
Digitizing conceptual designs adds precision to the process, enabling users to ensure they fit and operate as intended. It also yields models that can be fed into simulations to identify how a part or assembly will perform under load. Whether this be an aerodynamic or physical load, the results can be used to analyze design safety and performance.
With 3D scanning, it’s now possible to reverse engineer such models from real-world objects with such speed and accuracy, they can be used for product iteration. In the past, the SNAG Racing Rallye team has managed to use the highly flexible Artec Eva – a time-tested solution for digitizing medium-sized textured parts – for this very purpose.
Switching from paper modeling to 3D scanning for designing rally car upgrades has allowed them to make strength, speed, and maneuverability gains, while achieving lower production costs and lead times.
Architecture
While CAD is utilized to design architecture of all shapes and sizes, this is usually achieved with dedicated software, rather than mainstream ones. As is the case with product sketching, digitizing building design and project management has made it possible to iteratively make changes (in this case client-requested ones), without civil engineers having to start afresh.
More often called building information modeling (BIM) than CAD, the process also allows architects to preview how building plans will look once borne out. Popular software packages like ArchiCAD even enable users to generate photo-realistic visuals well before a shovel breaks ground, to help interior designers, and for marketing properties in advance.
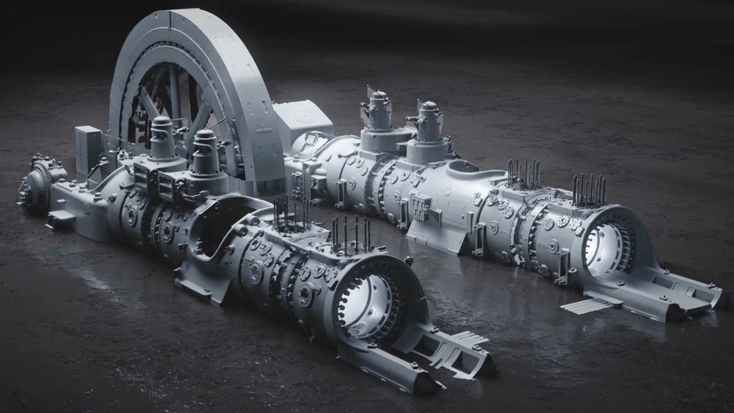
Long-range 3D scanning allows you to digitize facilities and drive on-site efficiency
With there being so many stakeholders in construction, BIM is an important site planning tool as well. Essentially, BIM modeling has seven collaboration levels, with the first being 2D drawings, and the last seeing these turned into a 3D model and shared with all involved. As it facilitates efficient site planning and costing, the latter is seen as the cutting edge.
Dental & medical
CAD is also thriving in dental, although it’s more often used for custom implant manufacturing than purely as a design tool. Dental CAM sees teeth 3D modeled, either via impressions or scans of patients’ mouths, and used as a basis for producing restorations.
Before dental CAD/CAM properly took hold in the 1980s, creating patient-specific crowns, implants, or dentures, would involve several trips to the dentist, after which molds would be sent for production. Now, dentists can manufacture in-house, using 3D scanning to capture smiles with enough precision to develop perfectly fitting dental implants.
Key point
It’s now common to see dentists in-source with CAD/CAM design and create custom implants locally at clinics.
One such practice, the Center for Implant Dentistry, has uncovered a way of combining super accurate full-color Space Spider scans with intraoral ones, to create incredibly realistic teeth models. Not only has this accelerated its implant design process, but allowed patients to preview their new smiles – and the clinic’s approval rates have soared ever since.
Unsurprisingly, given how easy it is to turn CAD output into STL files, 3D printing is also becoming a popular alternative to outsourcing, and there’s much potential in pairing the two technologies to achieve higher-accuracy dental results.
3D printing is starting to take off in healthcare too, where efforts continue to integrate CAD into the standard ‘DICOM’ clinical data format. It’s anticipated that CAD’s further adoption there will make it easier to customize casts and prosthetics, as well as drive surgical planning and drug design forward through biological modeling.
What’s next for CAD?
Wherever you look, whether it be automation, functionality, or usability, CAD output has come a long way, and it continues to be a fertile ground for innovation. As is the case in so many fields, AI can now be used to accelerate more steps in the 3D modeling process.
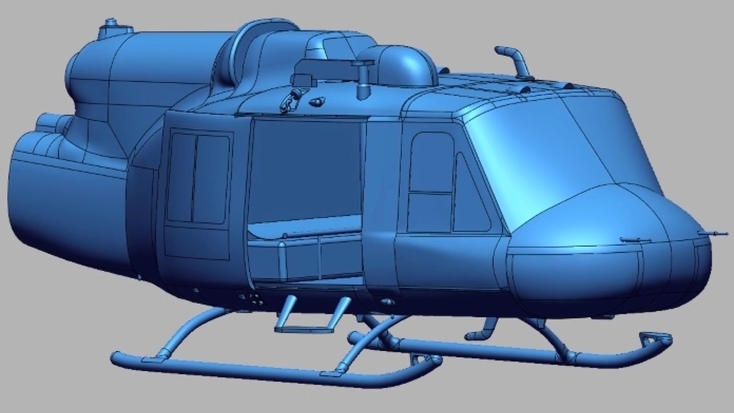
With platforms still advancing in leaps and bounds, the sky’s the limit for CAD design
Platforms like Dream Catcher offer AI-powered suggestions, and this functionality is only likely to become more common as a means of anticipating errors and automating repetitive design tasks. Elsewhere, AR/VR product and 3D visualization features are making it possible to view designs as if users were standing in front of them, while the ongoing roll-out of customization tools continues to make CAD popular among 3D printer users.
Given the hybrid nature of the industry – with some offering cloud-based platforms and others starting to add similar functionalities – it’s also impossible to ignore the rise of cloud-sharing. As more platforms take to the cloud, compatibility is becoming less of an issue, and the potential of Gdoc-style collaborative 3D modeling is emerging as a realistic prospect.
Overall, it’s clear that CAD remains at the center of product design across industries as a faster, digitized way of iterating and bringing goods to market. Greater CAD integration with AI, cloud computing, and 3D scanning will only increase these benefits, further automating, accelerating, and streamlining users’ workflows.
Read this next
More from
the Learning center
If you’re wondering whether you might need a CAD system for your company’s or clients’ design or engineering needs, read on. What may seem like a sizeable investment amidst a dizzying array of choices can prove to be one of the greatest decisions you make, saving you untold volumes or time, energy, and expenses. This article serves as an overview of today’s CAD systems, what types of challenges they help solve, as well as how 3D scanning powerfully enhances CAD workflows, for inspection to reverse engineering and beyond.
Computer Aided Design (CAD) software is used by designers and engineers in different spheres in a whole range of processes. It is a mainstay in the workflows of those working in design, simulation, manufacturing, and many other areas. CAD software is useful not just for providing visual representations of design concepts or drafts, but also for documentation, without which you wouldn’t be able to do things like make patent applications and legally protect designs, or check them for compliance.