How Israel’s A.B. Engineering uses Artec Leo for custom vehicle armoring
Challenge: While working under tight deadlines, to quickly and accurately 3D scan stripped-down vehicles in order to build the precise CAD models needed for creating custom armoring for a wide range of cars, vans, trucks, and buses.
Solution: Artec Leo, Artec Studio, Dassault Systemes CATIA V5
Result: Now, with the Artec Leo, in just two hours, a stripped-down car, van, or truck can be scanned with submillimeter accuracy, from bumper to bumper. No sprays or targets required. Five hours of processing, and the scans are ready for CAD. The client’s previous 3D scanner demanded sprays, thousands of targets, and an entire week to scan such vehicles, plus an additional week to process the scans for CAD.
Why Artec 3D? Being 100% wireless and laptop-free, Leo can be taken out for scanning projects at a moment’s notice. Easy enough for beginners, yet powerful enough for metrology engineers, Leo gives clients that edge to complete projects faster, with greater accuracy, thus reducing costs while making it possible to take on 200%-300% more work without any sacrifice in quality.
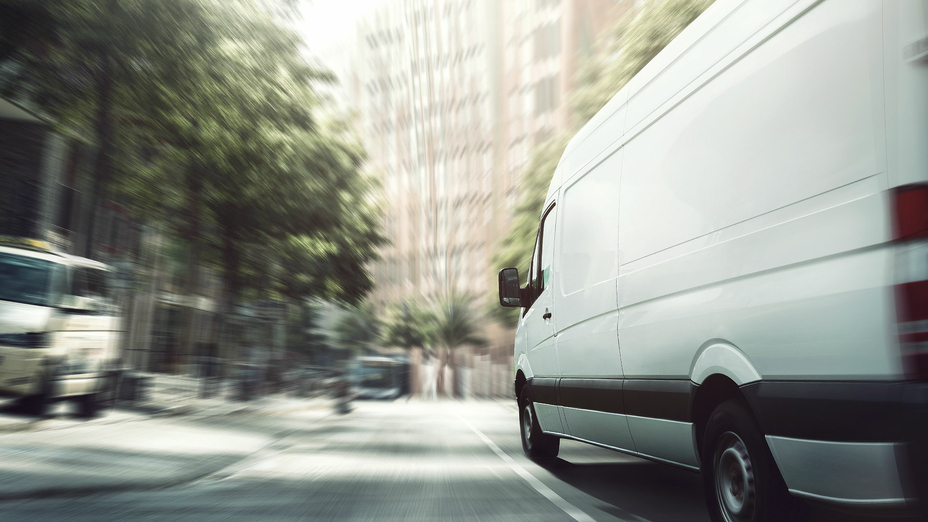
As the minivan filled with children and their parents rounded the corner, the two gunmen were waiting. Stepping out from behind parked cars, they leveled their AK-103s and opened fire, strafing the fast-approaching vehicle with controlled 3-4-round bursts.
But the driver wasn’t stopping. In seconds the gunmen’s weapons were empty and the bullet-pocked minivan sped away, its windows shattered yet intact, all the occupants inside shaken but unharmed.
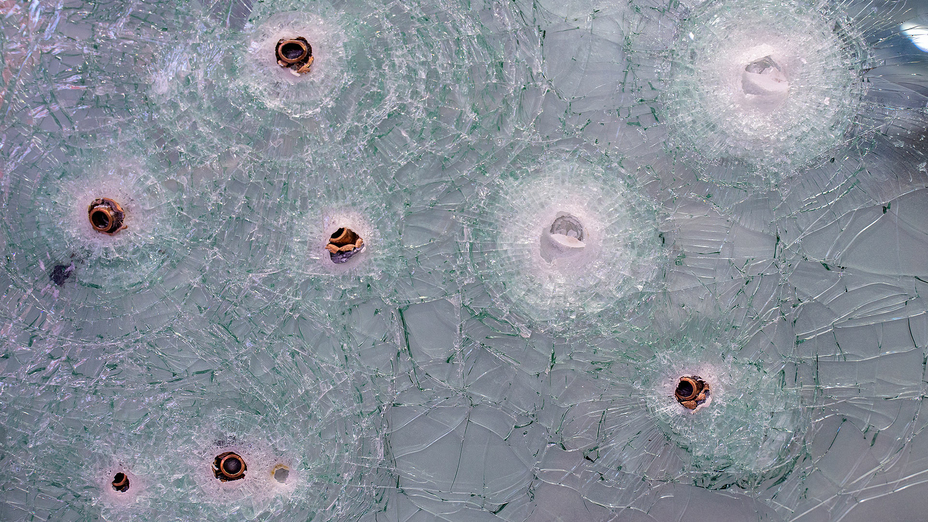
Bullet-resistant glass
Armored vehicles: not just for popes and presidents
Around the world, from Ukraine to the Middle East and beyond, the need for armored vehicles has never been greater. Not only for militaries, governments, and the ultra-wealthy, but for humanitarian agencies and groups, to safely transport passengers through even the most dangerous of areas.
The best of these bullet-resistant vehicles are discretely armored with various composites, steels, and ceramics, enough to stop a range of ballistic threats, from .22 to .50 caliber, depending upon the armor level chosen for each individual vehicle.
The goal is to achieve maximum protection while adding a minimum of weight.
Think of armoring like making a custom-tailored suit for a vehicle, albeit one worn on the inside. It must fit as snugly as possible, for a few reasons.
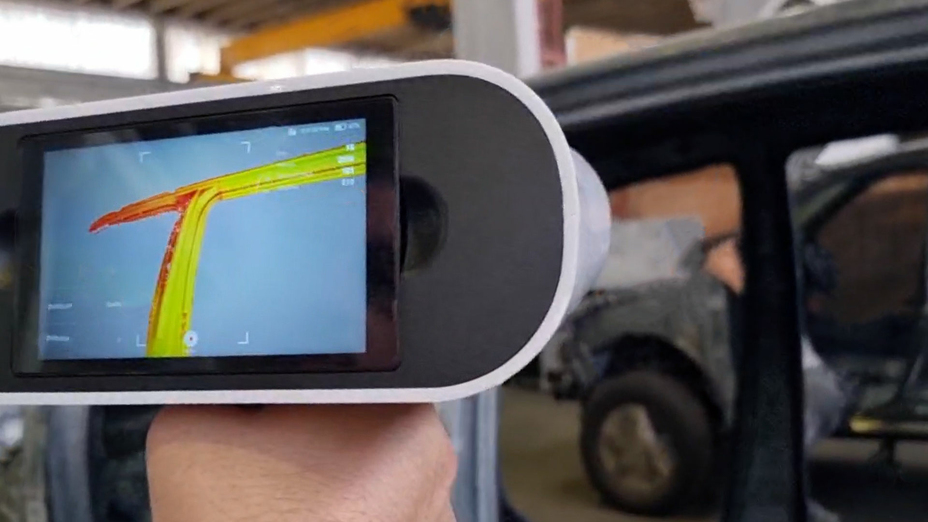
Artec Leo 3D scanning the frame of a 2022 Toyota Hi-Lux. Image courtesy of A.B. Engineering
Sometimes you need to be able to reinstall OEM interior parts in their original locations, with minimal changes for obvious cost reasons. And, if called for, the vehicle must look inconspicuous to a person (armed gunman) at a checkpoint talking to the driver.
Then, once everything’s in place, the occupants shouldn’t feel any loss of free space. And, finally, the armoring should be undetectable from the outside, so that even well-trained eyes will fail to distinguish such protected cars, vans, and buses from ordinary, unmodified vehicles.
Such “stealth requests” are made by clients on a mission-specific, car-by-car basis, with requirements that state at what viewing distance the vehicle should look run-of-the-mill. These distances can range from as far as 160 feet (50 meters) all the way to up-close-and-personal, standing right next to the vehicle itself.
In order to accomplish such a challenging feat, the vehicle must first be stripped down to its most basic frame and elements, and from there, measured as accurately as possible, every single square millimeter.
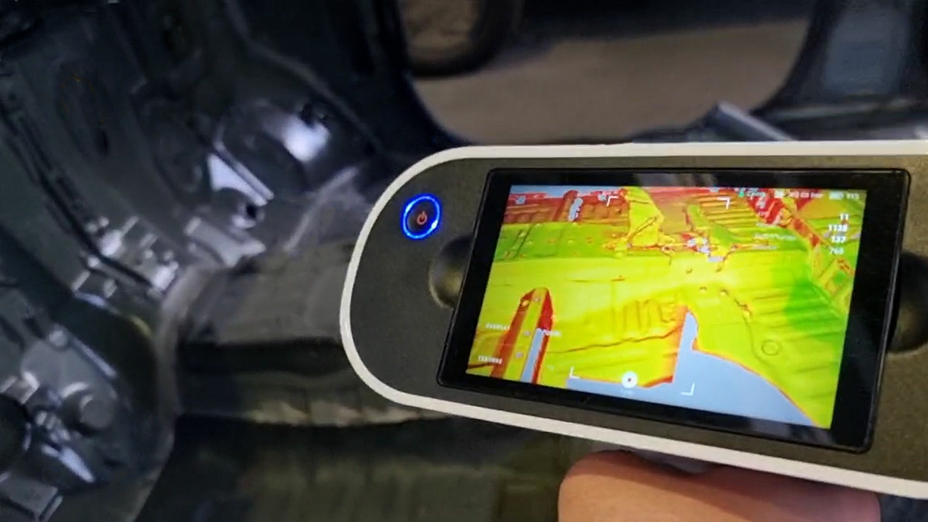
Artec Leo 3D scanning the frame of the Toyota Hi-Lux. Image courtesy of A.B. Engineering
Then, in the following stages, all the custom armor elements can be designed in CAD and manufactured under strict conditions so that once they’re installed and the OEM parts are put back into place, few to no gaps exist between the armoring, the doors, and any other potentially vulnerable sections of the vehicle.
Whenever this isn’t possible, new custom interior trim is created to flawlessly mimic the OEM interior trim, yet with more room allocated for the armor.
It’s a process that can take from 1-2 months for a small vehicle, such as a Toyota J79 truck, all the way up to 4+ months for a large, complex SUV, e.g. a Chevy Suburban.
Vehicle armoring via 3D scanning
One such vehicle armoring specialist with a well-deserved reputation in the industry is Israel’s A.B. Engineering Ltd., a mechanical engineering company working with leading aerospace and defense firms since 2012. At the very foundation of their comprehensive armoring workflow is 3D scanning.
According to the firm’s founder and CEO, Irakly (Ika) Baitish, “When it comes to armoring a vehicle for maximal protection of its occupants, as well as the engine, drivetrain, and other essential parts that keep the vehicle rolling so it can escape from the danger zone, it’s absolutely important to start off with precise measurements.”
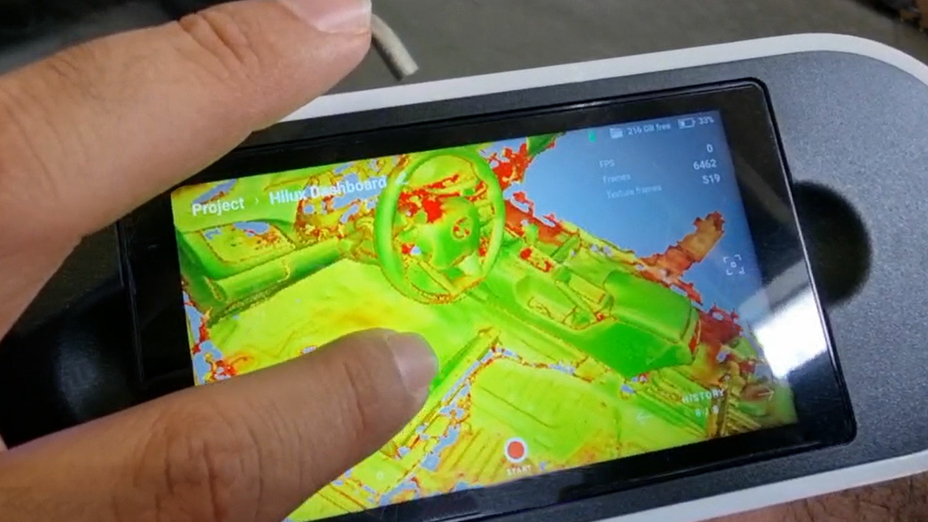
Reviewing a 3D scan of the Hi-Lux on Leo’s touchscreen display. Image courtesy of A.B. Engineering
He continued, “This is why we chose 3D scanning as our measurement medium of choice, because with it, we can obtain the exact dimensions of the entire vehicle, including the areas that are normally tricky to measure manually, such as the firewall, the section that separates the driver from the engine compartment.”
Once the 3D scans of the vehicle have been processed, they export the scans into their CAD system, Dassault Systemes CATIA V5.
There, they use the scans as reference models for designing the soon-to-be-manufactured ballistic panels and other armoring components, then virtually install them in the vehicle, to ensure that their final results will mean seamless, no-gap protection from bumper to bumper after the armoring is installed in the weeks ahead.
Finding just the right 3D scanner
But not all 3D scanners are alike. At first, Ika and his team were using a well-known, high-end portable 3D scanner for their work, one that required large numbers of targets and copious amounts of spray, as well as a laptop, a few cables, and a 220V power supply.
An example of a typical project at the time was when they were scanning the stripped-down cab and chassis of a Skoda Kodiaq that needed armoring.
After applying more than 3,000 stickers and the necessary volumes of spray, it took them a full two weeks to scan, and the resulting data wasn’t nearly as clean as what they needed.
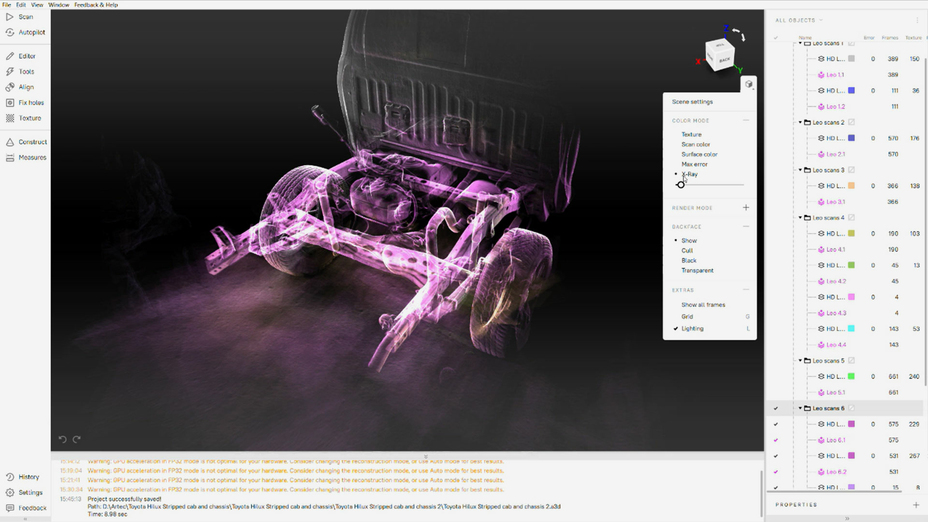
Artec Studio screenshot: X-ray mode view of Leo scan of the rear of the Hi-Lux. Image courtesy of A.B. Engineering
Before they could confidently stitch together the scans and create a highly precise 3D model for CAD, another week of cleaning the data and manual re-measurements ensued.
One of the teammates (the one who pulled the shortest straw) was in charge of peeling off the 3,000+ targets from the vehicle and then cleaning it. Unfortunately, some of the stickers left residue on the interior trim panels, making them unusable.
Looking at the excessive amount of time and efforts this entailed, Ika understood that their 3D scanner was seriously slowing his team down.
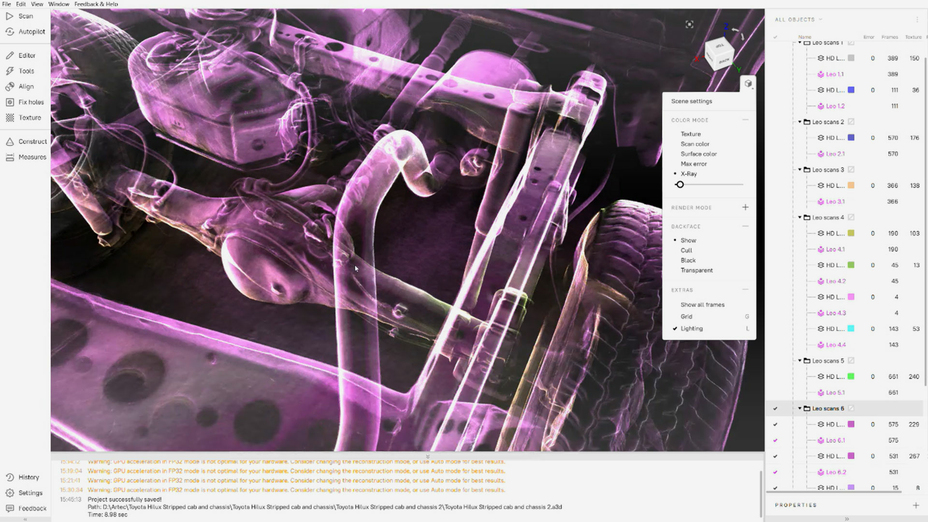
Artec Studio screenshot: X-ray mode view of Leo scan of the rear of the Hi-Lux. Image courtesy of A.B. Engineering
In an industry where project deadlines aren’t flexible, every day and every hour can make all the difference. So, once the project was finished, Ika began fervently searching for a better 3D scanner.
Saying goodbye to weeks of scanning, targets, and spray
Soon he found the Artec 3D website and focused on the Artec Leo, a professional handheld 3D scanner that’s been a favorite for reverse engineering, forensics, healthcare, and other applications for years.
Delivering high-resolution, color 3D scans with submillimeter accuracy, Leo features both a touchscreen display and a built-in battery pack, making it 100% portable, with a high FPS capture rate and large scanning field of view.
Scanning a 2022 Toyota Hi-Lux faster than ever before
To highlight a single example of how A.B. Engineering’s workflow has improved since adopting Leo, one of their recent armoring projects called for scanning the stripped-down cab and chassis of a 2022 Toyota Hi-Lux 4 door truck.
With Leo in hand, Ika and his team went to work capturing the Toyota. Just two hours later, without having to apply either a single target or a squirt of spray, they were completely done with the scanning.
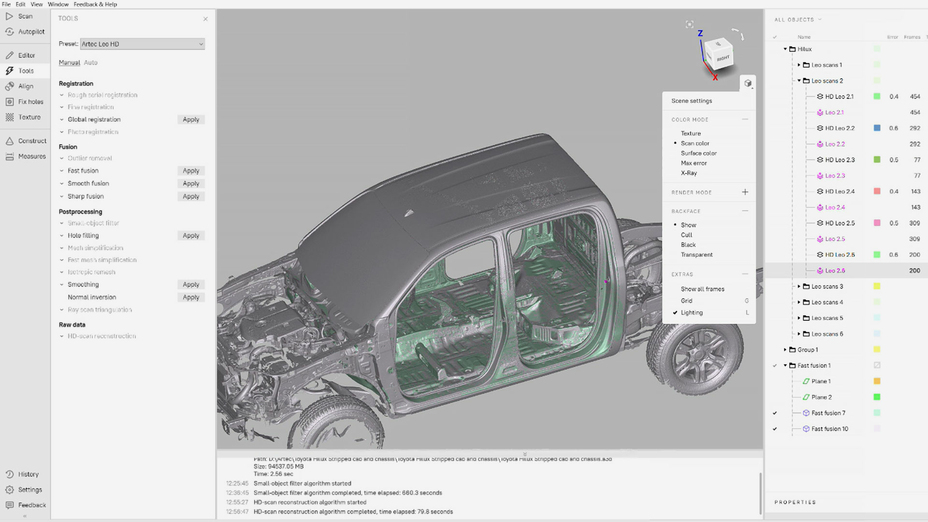
Artec Studio screenshot: combined Leo scans of the Hi-Lux. Image courtesy of A.B. Engineering
From there, it took a mere five hours in Artec Studio software to process the scans and create the STL files that were sent to CAD to design the armoring for the Hi-Lux.
Compared to their previous scanner’s one week of scanning + another week of scan processing to achieve almost the same results, yet with markedly lower quality, the contrast was astonishing.
In Ika’s words, “Looking back to how it used to be, Leo gives us an incredible speed difference. And the data we get with Leo is much cleaner, with no misalignment issues at all.”
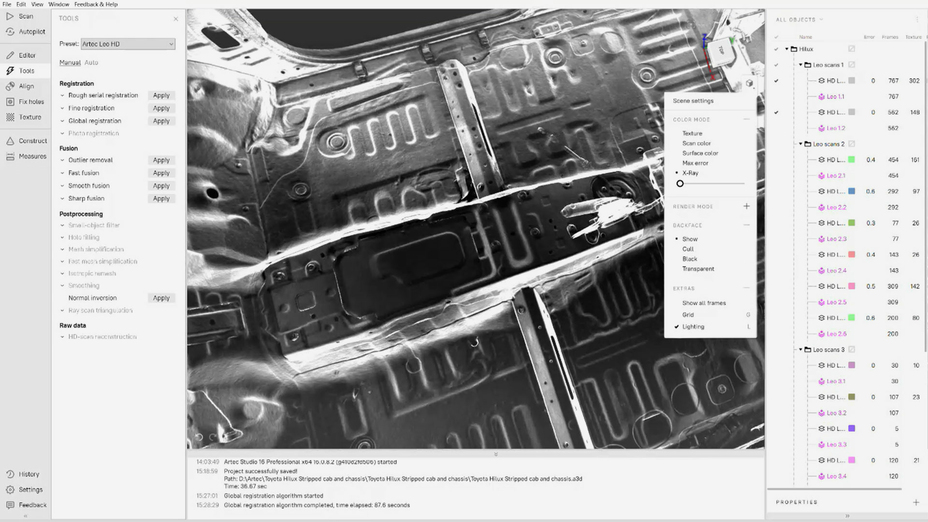
Artec Studio screenshot: X-ray mode view of Leo scan of the interior of the Hi-Lux. Image courtesy of A.B. Engineering
He continued, “Our measuring process has significantly improved both in terms of time and quality. Leo has dramatically changed the quality of our engineering output and the ability to get that extra few percent needed to close ballistic gaps, which can literally save lives.”
“Each and every vehicle demands a custom approach”
For every vehicle they armor, Ika and his team consult with the client, taking into account the degree of ballistics protection needed, intended usage of the vehicle, as well as expectations in regards to timeframes and secondary vehicle upgrades required.
Considering the latter, a typical armoring job can easily add 500-2,000 pounds (230-900 kg) to a vehicle’s total weight. To accommodate such an increase, special heavy-duty brakes, axles, transmissions, and drivetrains are occasionally called for.
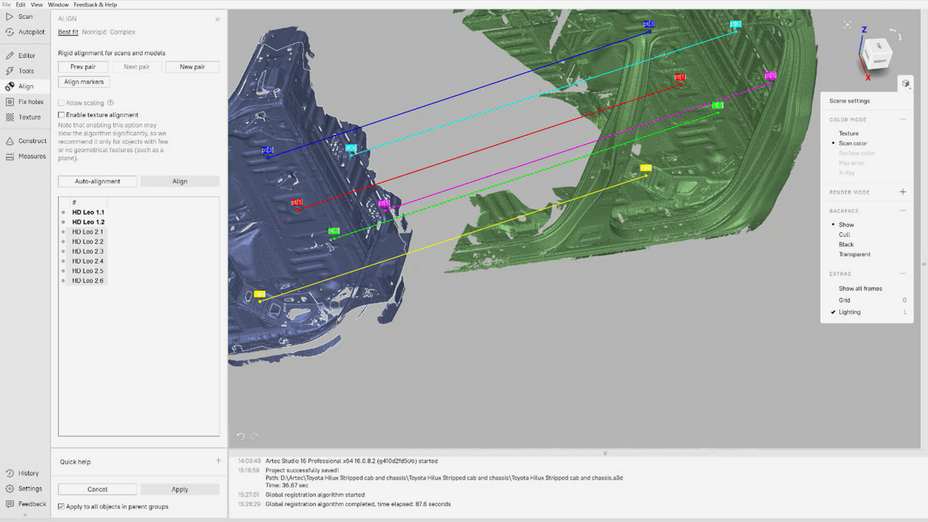
Easily aligning the Leo scans of the Hi-Lux in Artec Studio. Image courtesy of A.B. Engineering
“Since this ‘beefing up’ of the vehicle entails a lot of extra weight being added,” said Ika, “this places even greater pressure on us to optimize the armoring for the lowest weight with the highest degrees of defensive coverage.”
He continued, “Now that we have Leo, achieving this kind of peak result is that much faster and easier.”
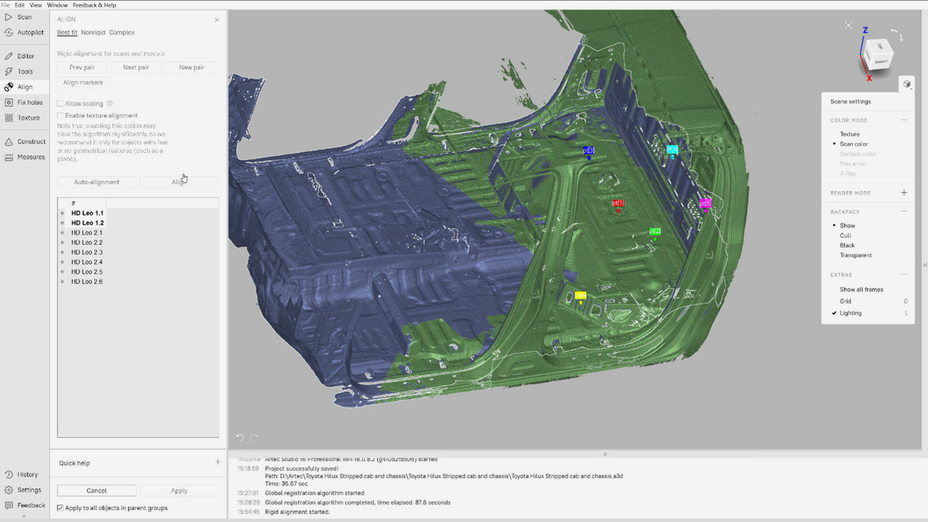
With just a few clicks, the scans of the Hi-Lux are aligned in Artec Studio. Image courtesy of A.B. Engineering
Testing their work on the live-fire range
Ika and his team stand firmly behind their work, regardless of project size or complexity, and Leo allows them to do so all the more confidently. A recent demonstration of the quality of their armoring speaks for itself.
One of their vehicles, a heavy armored truck, was taken out to a live-fire test facility, where more than 800 rounds of all calibers (up to .50) from a variety of weapons were fired at the vehicle, with zero penetrations.
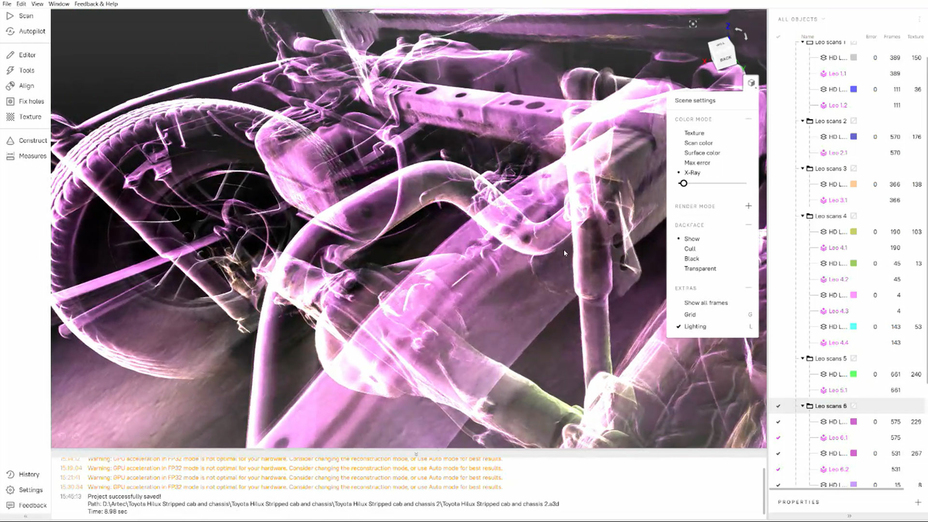
Artec Studio X-ray mode view of Leo scans of the rear of the Hi-Lux. Image courtesy of A.B. Engineering
Whereas another armored vehicle, one from a competitive firm, was subjected to a similar barrage of bullets from the same weapons. It suffered hundreds of penetrations, well past the point where, if that had been a real-life scenario, the occupants would’ve had zero chance of survival.
Have Leo, will travel: armoring cars, trucks, buses, and planes
For years now, A.B. Engineering’s team of experienced engineers and technicians have fulfilled a broad spectrum of armoring projects, from simple to complex, for a wide variety of vehicles, aircraft, and other objects.
“Because Leo is easy to take along with us, we’re hopping on a plane and flying wherever our next project takes us. When we get there, we know we’ll be finished faster than ever, and all the data will be right there on Leo’s SD card, clean and ready to go,” said Ika.
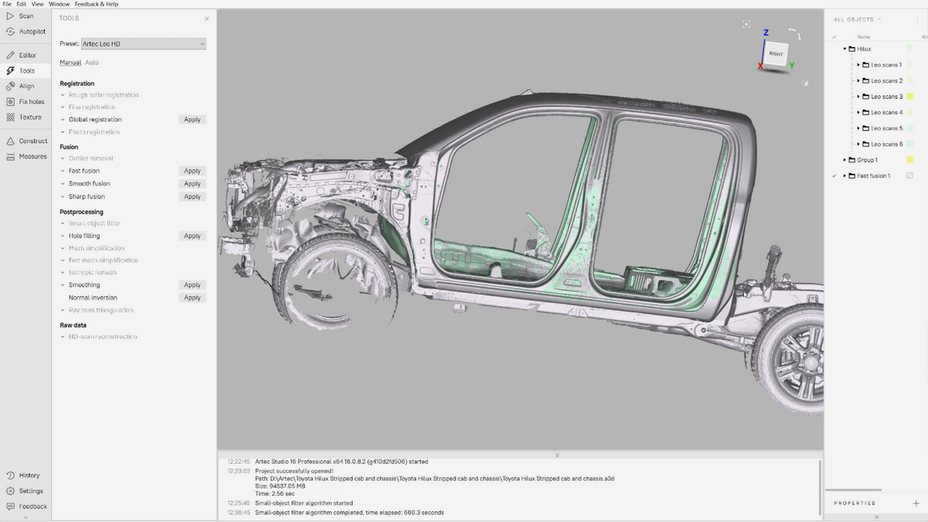
Ready for CAD: Artec Studio screenshot of the combined Leo scans of the Hi-Lux. Image courtesy of A.B. Engineering
He continued, “Just having the ability to bring only the scanner without even a laptop to the field anywhere in the world is a huge bonus, and the option to scan without targets is another massive benefit since we don’t need to prep the object we’re scanning. And this also means we leave no traces of the scanning process, which can be critical sometimes.”
A steady flow of clients and referrals year-round
From a business perspective, Leo has enabled Ika and his team to be far more competitive. Today, with Leo in hand, every project that includes 3D scanning takes 2 weeks’ less engineering time than before. This allows the company to pass along lower prices directly to their clients, resulting in a steady flow of clients and referrals year-round.
Ika explained, “Before we adopted Leo, the 3D scanning would take up 20-30 percent of the total cost for the client, because of all the time it demanded. But with Leo, the scanning is just 5 to 10 percent of the project cost. So, in some cases we’re able to charge 20 percent less than a competitor who’s using a less-advanced 3D scanner, like the one we used to have.”
Scanners behind the story
Try out the world's leading handheld 3D scanners.