Artec Eva helps furniture maker reduce development time by weeks and save thousands of dollars
The Goal: To scan their prototype, then take the 3D model and digitally fine-tune it before sending it to the factory electronically.
Tool Used: Artec Eva
A furniture manufacturer outsources 3D scanning to Artec to boost productivity, save time and cut costs.
MU Form Furniture Design is an Oakland-based company that designs, manufactures and distributes furniture products for the modern home and business. The company is never short of orders, since good and original design is sought after by architects and interior designers.
The main material MU Form works with is high quality bent ply, which is one of the most widely used materials in this industry due to its ability to create a variety of shapes for chairs, stools and tables.
The company’s specialists seek to create great designs that pose a challenge for other manufacturers to copy or replicate.
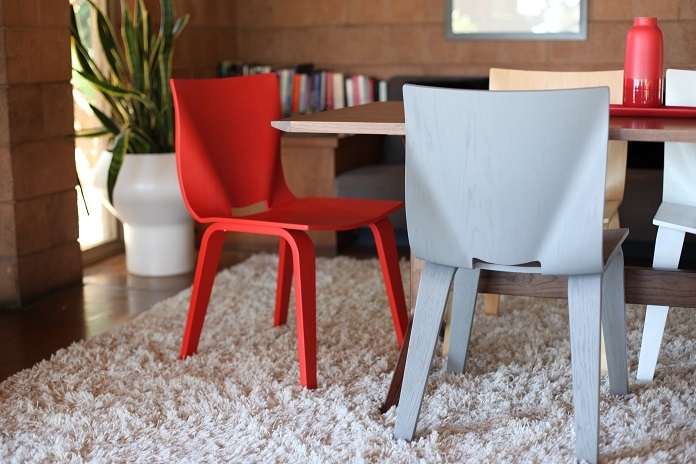
The V Dining Chair in red and grey, designed by MU Form’s Po Shun Leong.
“Our designers are tasked to develop furniture designs that require a significant amount of trial and error by developing physical prototypes of chairs and stools,” says Mark Leong, CEO of MU Form.
To produce a new original piece of furniture, MU Form would normally ship a physical prototype model to a factory overseas so they reverse engineer the model by using a router duplicator to create a wood mold.
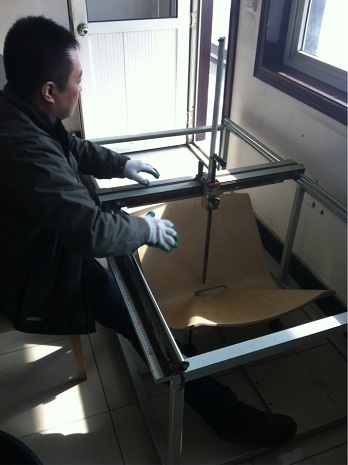
The previous method for capturing the V Chair’s dimensions for production.
“While this method worked to get us started in making a somewhat accurate representation of the chair or stool prototype, it didn’t allow us to efficiently fine-tune some of the curvatures and surfaces that we knew needed to be fixed for the final production furniture,” says Mark.
For example, surfaces that were meant to be absolutely flat could not be adjusted for the mold in the initial stages. Instead, some manual work needed to be done on the mold, which would sometimes lead to inaccuracies in the final production pieces. Additionally, this method did not provide for mirroring the furniture, which would ensure accurate symmetry.
“While the results allowed us to get our furniture into production, it fell short in terms of our expectations for quality and consistency,” says Mark.
The company has recently started to outsource 3D model making services to Artec’s office in Palo Alto, CA.
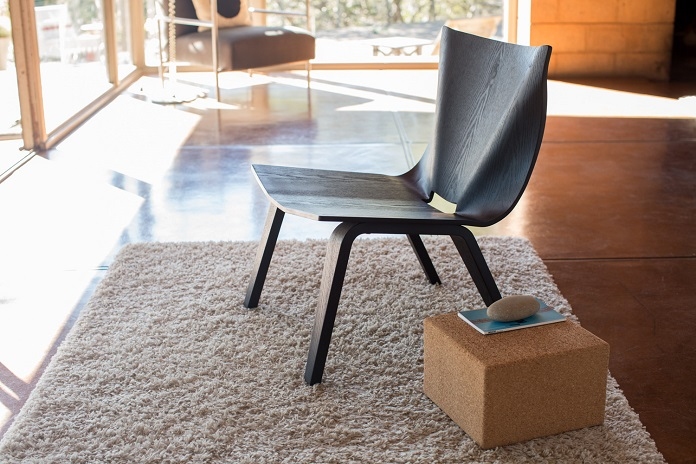
The V Lounge Chair in black, designed by MU Form’s Po Shun Leong.
This is what the workflow is like now: the furniture designer develops the physical prototype of a furniture piece. To reverse-engineer the piece, the prototype is 3D scanned with Artec Eva. The raw point data is then used to create contours in Rhino 3D, in particular to accurately model every nuance in curvatures and radii.
Flat surfaces can be recreated in the program. For a symmetrical piece, the model is mirrored. The result is a final model that has been minimally altered to remove the prototype’s defects.
The 3D model is then emailed to the factory which creates an accurate CNC metal mold directly from the file. The company also uses 3D model renders for patent processing and to show upcoming products to potential clients.
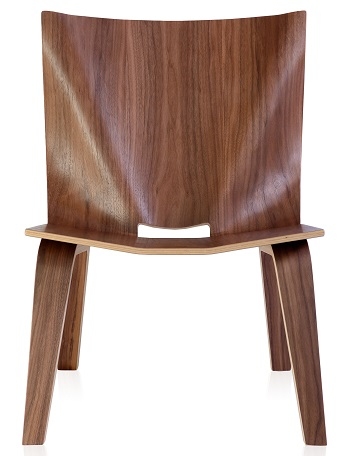
The V Lounge Chair in walnut.
The prototype of the V Chair has been 3D digitized by Artec’s Rachel Yalisove. Let’s hear from her:
“The scanning process was very quick, taking no more than 10 or 15 minutes. In general, it was a very easy scan. The chair is wood with a matte finish, and some grain lines helped Eva stay on track. I captured the front, back, edges and handle in separate scans, then snapped them together with the align tool.
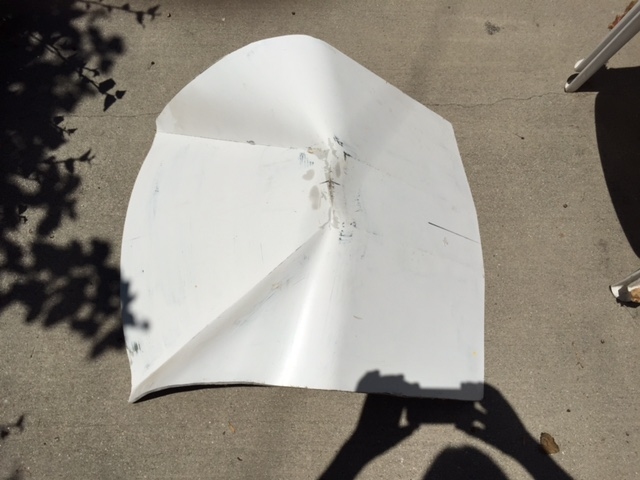
The prototype of the V Chair, 3D scanned with Artec Eva.
“I just had to make sure to pay close attention to the edges as to collect enough data for a crisp contour. The scanner worked fine with these areas. It helped to position the chair on a textured floor or up against a wall to maintain tracking.
“Processing took less than an hour. After aligning the data together, we used Registrations, Outliers Removal, and Smooth Fusion algorithms, which worked really well. We were able to sift our data down to .1 quality accuracy very quickly. The seat was 1.7 million polys / 89.2 Mb. Each leg was about 550 k polys / 30 Mb. We exported the files in STL format and emailed them to the client via a download link.”
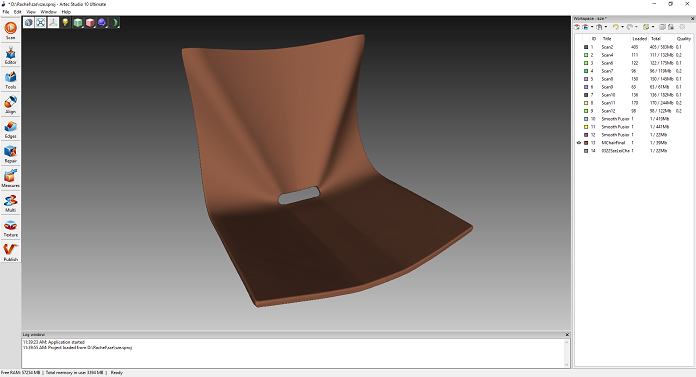
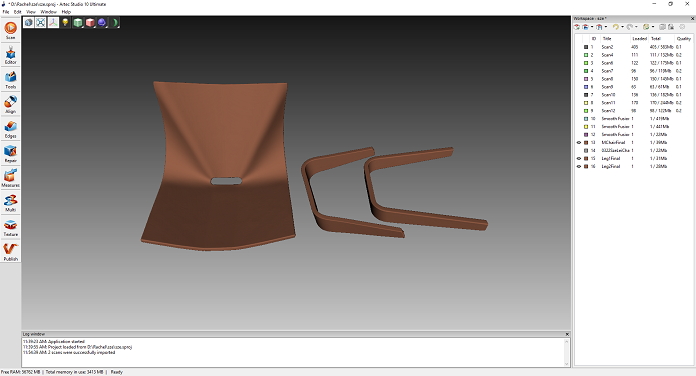
The 3D model of the V Chair in Artec Studio.
The use of Artec scanners has helped MU Form significantly increase the quality and consistency of their furniture, while at the same time boosting productivity, saving development time and reducing development and production costs.
“It has allowed us to digitally fine-tune our furniture in digital space so that the mold factory can make a metal mold via CNC (as opposed to a wood mold) from a digital representation of the chair or stool in a much shorter time frame than the previous process of sending the prototype and developing the mold by hand,” says Mark. “A CNC metal mold allows for much higher quality production furniture to be made.”
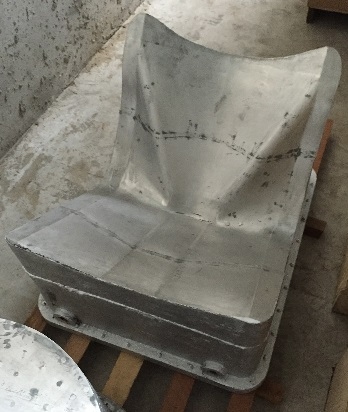
The metal mold for the V Chair, obtained using the new method.
The time frame for creating a mold has been slashed from 60-90 days to 20 days, and savings are estimated to reach 10-15%.
Mark says that he is most excited about precision: “The precision of reverse-engineering the prototypes and having the ability to fine-tune digital models allows us to move toward a totally new level of quality and consistency for our furniture.”
Mark adds that MU Form plans to continue working with Artec to make other furniture pieces, including tables, chaise lounges, and other larger pieces.
Scanners behind the story
Try out the world's leading handheld 3D scanners.