Catesby Projects chasing lap time gains for elite racing teams with Artec 3D scanning
Challenge: Identifying a more efficient means of creating aerodynamic simulation models for vehicles designed to compete in some of the world’s leading motorsport series.
Solution: Artec Leo, Artec Ray II, Artec Studio, Geomagic, HyperMesh
Result: A process through which highly detailed 3D models of motorbikes or open-wheel race cars can be created and then fed into Computational Fluid Dynamics (CFD) software. Once there, these can be used to carry out simulations that help engineers optimize downforce setups faster, in a way that reduces aerodynamic drag, and drives down lap times.
Why Artec 3D? Without getting hold of sensitive CAD data from manufacturers, it would usually be impossible to attain detailed 3D models of race cars or bikes. But by using Artec Leo and Ray II, Catesby Projects is now able to capture these vehicles with outstanding accuracy and pace.
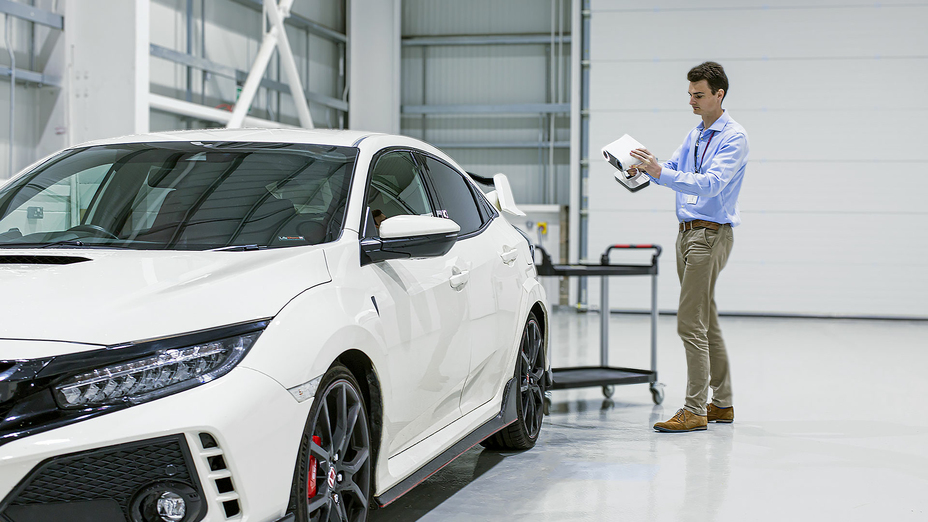
A Catesby Projects engineer 3D scanning a roadcar with Artec Leo
In the world of motorsport, fine margins are often the difference between success and failure. A few tenths of a second may sound like an incredibly finite time period, but lose that each lap to your competitors, and you’ll quickly find your team’s at the back of the field.
So, how do these racing outfits identify ways of reducing lap times? That largely depends on the series we’re talking about. In Formula 1, each team designs and manufactures their car from scratch. While some certainly take inspiration from others, the sport’s competition model makes way for a ‘development race,’ where they compete to find lap time across a season.
In practice, this sees F1 constructors reshape floors, side pods, front wings, rear wings, and other aerodynamic parts, so that cars can glide more efficiently through the air.
However, things work slightly differently in a single-make series. As these championships are fought for in completely identical cars, gains can be harder to find, and instead of engaging in a development race, team engineers have to focus on optimizing setup.
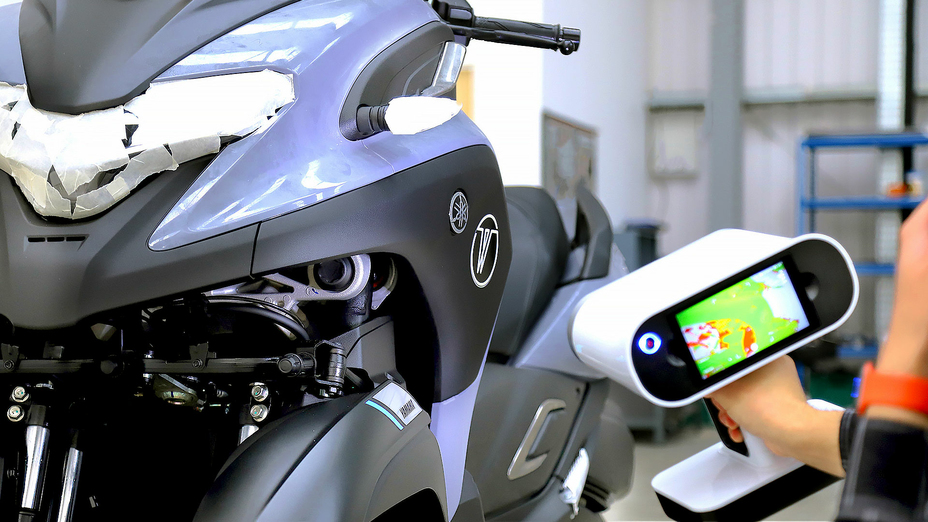
A motorbike in the process of being 3D scanned with Artec Leo
But, the problem with simulation work is that it relies on you having accurate 3D models to test with, and manufacturers don’t often want to hand out the valuable CAD data behind these. This is where Catesby Projects can help. The UK-based aerodynamics and simulation specialist scans such cars and creates R&D-ready 3D models for teams in single and multi-make series alike.
“Let’s say someone has bought a car to enter a series,” explains Jon Paton, a Project Manager at Catesby Projects. “They’re not allowed to change or modify it, but they want to try and get the best setup out of it that they can.”
“We scan it and do computer simulation work to find out what the aerodynamic changes could be. We then help them see if changing the front wing angle or adding a bit more rake (floor angle) would help on specific circuits.”
“3D scanning enables us to do a whole load of simulation work, all virtually without ever having seen the CAD data to make a physical model.”
“No choice” but 3D scanning
Operating as part of wider engineering consultancy group TotalSim, Catesby offers physical and computational testing services that facilitate aero development and validation. Many of these are now enabled by Artec 3D scanning, but that wasn’t always the case.
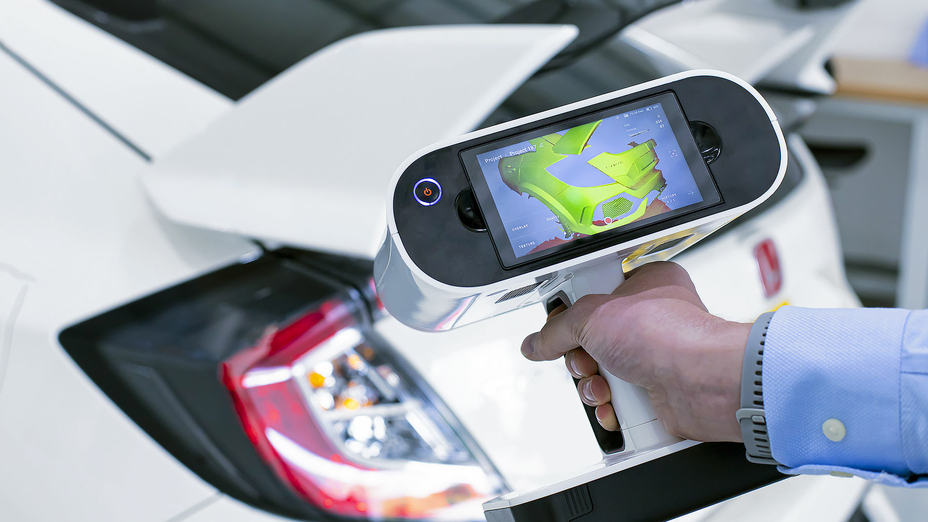
3D scanning using Artec Leo, with captured data appearing on its built-in display
With the manufacturers of single-make championship race vehicles so reluctant to share CAD data, Paton says engineers “effectively have no choice, you need a 3D scanner.”
His firm’s initial efforts actually revolved around using a photogrammetry kit, which provided global accuracy, and an Artec Eva for picking up fine details. After that, the company improved the accuracy and speed of its process further, working with Artec Ambassador Central Scanning to switch to the more advanced Artec Leo and Ray.
“Using these devices, we’d usually be able to scan a race car over a couple of days out on-site. We’d take the car apart and scan the whole thing in around four hours with Ray,” said Paton. “Then we’d gradually disassemble it bit-by-bit, so we can scan every duct, take a wheel off, scan the calipers, pads, and everything else with Leo, before putting it all back together again.”
At first, Ray enabled Catesby to achieve greater accuracy over distance and scale its ambitions – at one point even allowing its team to capture an entire helicopter. But since getting Artec Ray II, Ray’s faster, longer-range successor, they’ve taken their workflow to a whole other level.
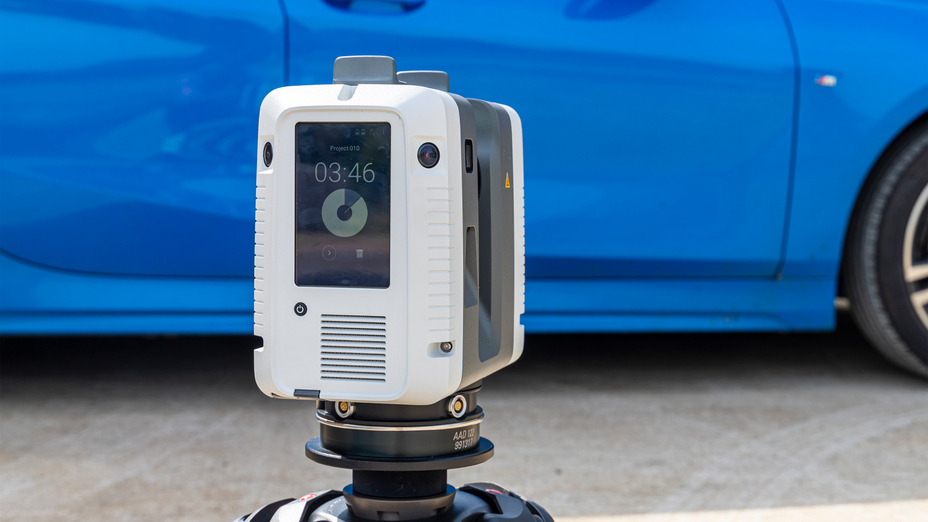
Artec Ray II’s built-in display indicating how much time is left in an automotive scan
Now, with Ray II, they can scan vehicles even more rapidly, before digitizing design-critical areas with the versatile, wireless Leo, and build a model using the highest resolution data from each. According to Junior Design Engineer Tom Parrish, who got his first taste of Leo 3D scanning six months ago when he started with the firm, picking up the device has been a breeze.
“When I first started using it, I remember it being very intuitive,” explained Parrish. “As it’s quite user-friendly and its interface is so good, there are actually a limited number of things that can go wrong. Just to practice with, I scanned a sofa and a chair, and when I first saw a 3D model appear live on the built-in display, it was very cool!”
In its US office, Paton adds that Catesby uses a cheaper, wired scanner too, and as well as bringing cable-free flexibility, he says Artec Leo is comparatively much faster.
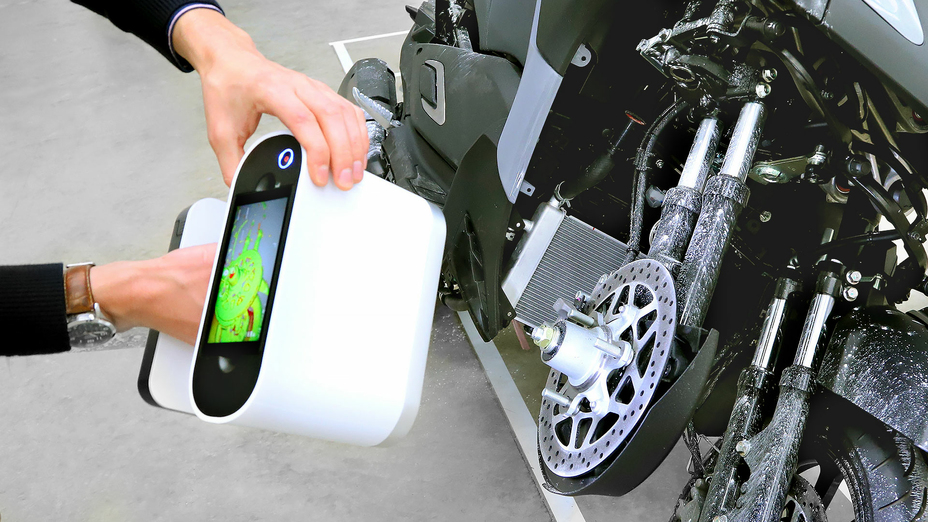
A motorbike being tilted slightly to ensure it can be captured in high detail with Artec Leo
“We do trips to Brazil, France, and Germany, and we can just take Leo, hop on a plane, we scan there for two days, then we hop back.”
Scan-based CFD sim work
Artec Studio is also central to Catesby’s 3D scanning workflow. Once the firm has finished the capture process, it uses the industry-leading software to align and tidy up meshes. Parrish is particularly fond of its alignment tools, which allow you to “lump patches together,” so “even if you’re missing data from one scan, you can align it with another to get a complete model.”
For those wishing to automate scan data processing, Artec Studio comes with its very own Autopilot mode as well, which picks the optimal algorithm for dealing with a given dataset. If desired though, users can get into the settings and tweak them individually.
In Catesby’s case, the latter workflow has proven better suited to its business. In fact, Parrish says the ability to “mess around with different settings” has allowed it to identify a way of “getting smaller objects to align properly and fuse together,” while “dropping the number of polygons in a mesh,” as a means of minimizing the size of exported files.
From Artec Studio, Catesby sends meshes to advanced engineering programs like Geomagic Wrap to prepare them for airflow experimentation. With Wrap N-point alignment, Paton and his colleagues can align multiple scans based on selected points, and where they have CAD data, its deviation analysis toolkit allows them to check for errors.
Once ready, these highly detailed 3D models are run through CFD simulations, which help teams rapidly identify opportunities to optimize race car drag and downforce performance.
“It’s all about helping race engineers set the car up quicker to find performance,” explained Paton. “They could do it physically if they had enough time to test on-track, but they have limited practice sessions, so they want to effectively have a pretty good starting point when they turn up at the track.”
“Each circuit’s different but we can help them with that – if it’s a low-drag circuit versus a high-downforce one, the simulation tools will help them pick the right combination of setup.”
Setting up a “scanning car wash”
With Catesby working with championship-winning race teams, it’s worth asking where it can possibly go next. In automotive, Paton has targeted the creation of a more streamlined “scanning carwash” workflow, in which cars can be fully captured in a single pass.
Already, upgrading to Ray II has slashed exterior digitization lead times by half, while yielding higher quality results that better capture hidden details like undercarriages or wheel arches, and require fewer Leo follow-up scans. With Ray II data processing and fusion also being much faster, its team now aim to create CAD models from scratch in under two days – quickly enough to analyze single-seater setup changes between tests.
However, the company isn’t just interested in cars – it wants to create 3D models of people too. While sister firm Vorteq has previously used 3D scanning for developing race bikes, Catesby now operates a 2.7-kilometer underground test facility, where it has ambitions of using 3D scanning to capture every vehicle passing through the tunnel.
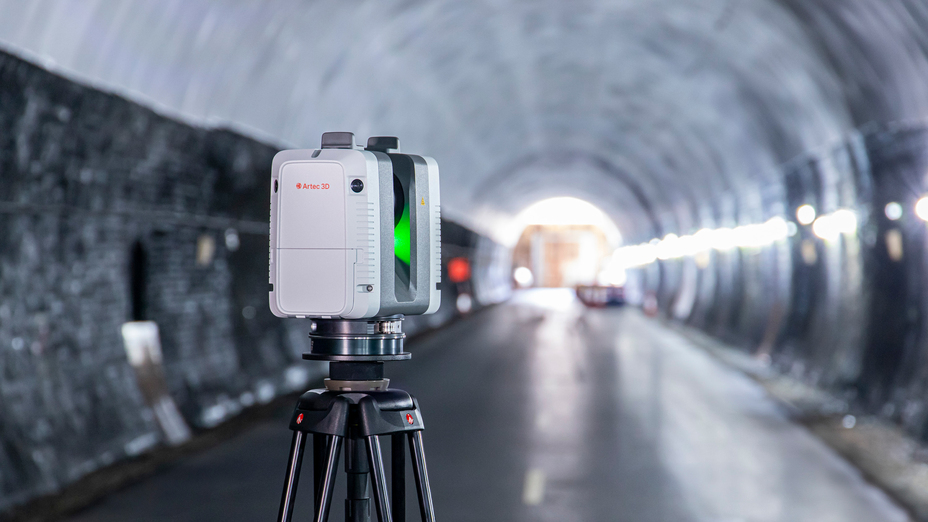
Artec Ray II in the process of 3D scanning the Catesby test tunnel facility
Elsewhere, it also has its own athlete-scanning business, in which it works with Olympians to help make gear as skin-tight and aerodynamic as possible. Moving forward, Paton says Catesby sees promise in both these applications, with scanning unlocking opportunities to analyze competitors in motorsport, and “really gathering pace” in the world of cycling.
“The cycling world is getting more and more custom fit, whether that be a skinsuit or a bike,” concluded Paton. “So, to be able to capture the geometry as quickly as possible is perfect.”
“Artec Leo is probably the best solution we’ve found to customizing athletes’ equipment by a distance.”
Scanners behind the story
Try out the world's leading handheld 3D scanners.