Customizing pipe repairs with Artec Leo to keep oil & gas refineries running
Challenge: Accurately measuring complex, damaged piping and equipment in hot, cramped refinery conditions so that custom repair solutions can be designed, manufactured, and installed to carry out repairs as quickly as possible.
Solution: Artec Leo, Artec Studio, Geomagic Design X, SOLIDWORKS
Result: Sub-millimeter accuracy scans are now captured, cloud-shared with engineers, and used to tailor clamps to piping that needs repairing. Six times faster than hand measuring, this rapid new workflow keeps facilities online to minimize costly unplanned downtime.
Why Artec 3D?: Tough and ultra-compact, Leo is ideal for capture in confined industrial spaces. Artec Studio makes processing seamless, while Artec Cloud allows technicians to instantly share scan data with remote partners for custom part design and manufacture.
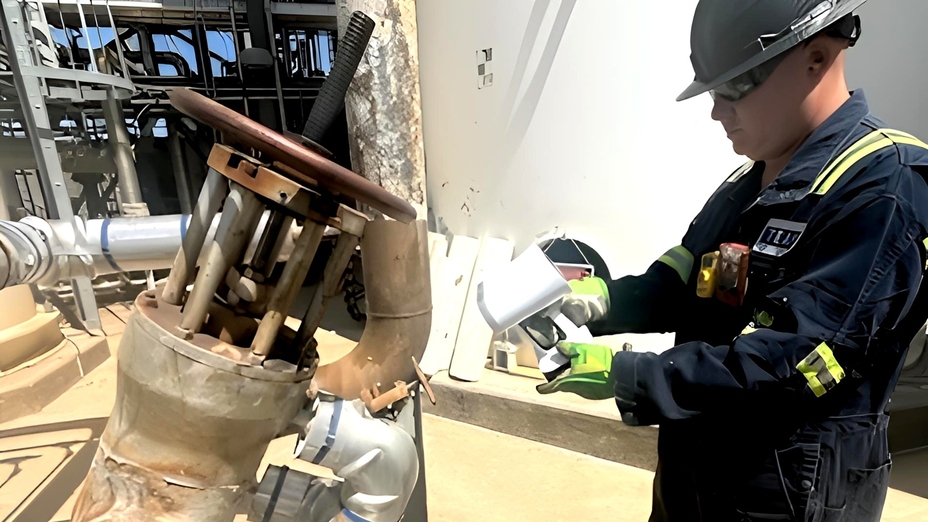
A Team, Inc. technician digitizing complex pipe geometry with Artec Leo
Most of the time it goes unnoticed, but our world is covered by millions of miles of pipes carrying vital resources from plants and refineries to users. It’s only when things go wrong with oil and gas networks that they hit the headlines, often triggering damaging coverage for operators.
Leaks cause environmental issues, impact customer confidence, and in some cases necessitate unplanned downtime. Pipes can carry resources worth millions of dollars each day, so incidents are also extremely expensive – and with repairs, time is of the essence.
Aiming to avoid such disasters, pipeline operators tend to shut down every 2-3 years for maintenance. But between these checkups, piping is prone to damage caused by corrosion, erosion, or cracking. This is where specialty service providers like Team, Inc. come in.
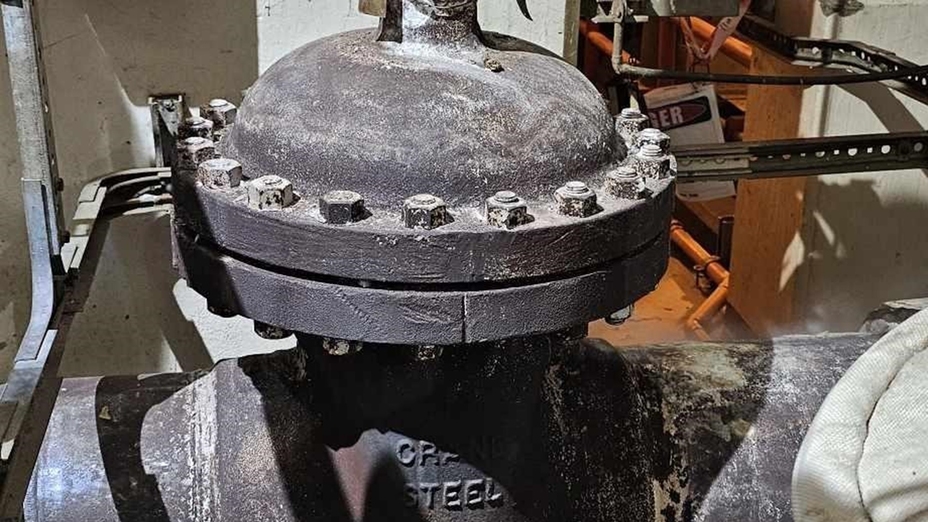
An example of the pipework Team, Inc. 3D scans for urgent on-site repairs
Team, Inc’s inspection and repair services allow clients to verify integrity, carry out preemptive maintenance, and conduct repairs that keep assets operating. While much of the industry still sizes up damaged piping by hand, Team, Inc. has taken a different approach: adopting Artec Leo to measure and repair damaged parts with unprecedented pace and precision.
Cutting out costly errors
While based in Houston, Texas, Team, Inc. has a presence in more than 20 countries and a service offering for industries ranging from energy to aerospace, making it a global engineering solutions provider in every sense of the word.
But until fairly recently, its on-stream repair offering still depended on caliper-based measurement. According to Adam Thistlethwaite, its VP of on-stream services, hand measuring was not only time-consuming but highly risky. Pipe networks tend to feature complex angles that are difficult to judge by eye, while dimensions written on paper and sent by photo are easy to misinterpret.
Repair parts are costly to produce, making manufacturing mistakes expensive, but even more importantly, issues also impact the repair timeline. It’s this risk that prompted Team, Inc. to digitize its workflow. Initially, its engineers tried measuring pipework with wired, target-based 3D scanning. But applying/removing target stickers proved clunky in refinery environments, and in some cases, heat haze distorted results.
That’s why they reached out to US-based Artec Gold-certified partner GoEngineer, who has equipped them with Artec Leo. Team, Inc’s technicians had always taken measurements by hand and never used 3D scanning before. But the device’s click-to-scan functionality meant they could quickly get to grips with it and move into field use with just a few hours’ training.
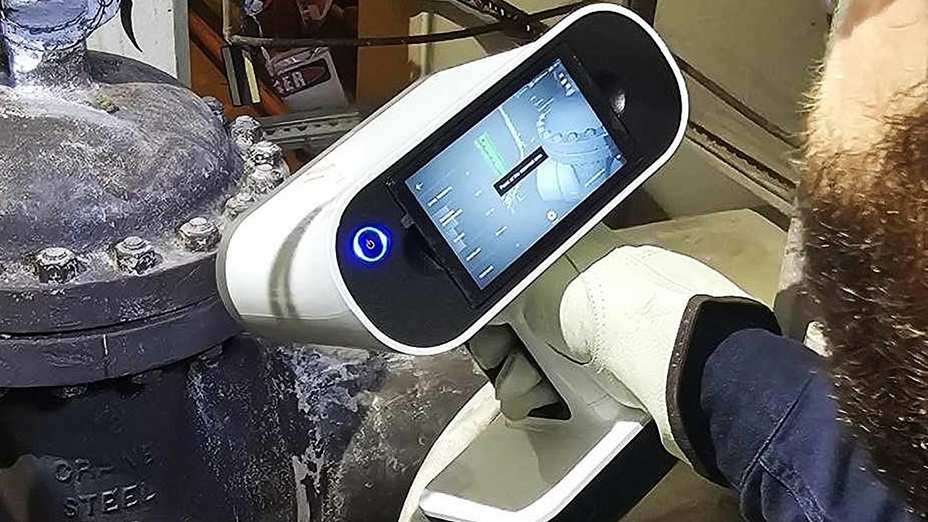
Artec Leo’s built-in display providing real-time feedback to a Team, Inc. technician
Rugged, portable, accurate, and incredibly easy to use, Leo has slotted straight into the company’s workflow to relieve any lingering doubts and allow for error-free leak clamp customization.
“With some corroded pipes, you’d assume they turn 90°, but it’s actually 92°,” explained Thistlethwaite. “If we tried to force on a clamp, it could fail the pipe, causing a safety concern. Now, if something’s not quite a ‘perfect angle,’ we can capture that with 3D scanning and incorporate it into the design so it fits first time.”
Pipeline design on the cloud
Even when capturing carefully, Team, Inc. can now digitize 1m2 (10 sq. ft.) piping inside an hour – a huge time saving against 5-6 hour sketching sessions – but that’s not the only place it’s making gains.
Its engineers start by capturing and aligning data in Artec Studio. Autopilot streamlines the process by choosing the best algorithms on their behalf while combining registration, alignment, and decimation into a single step. The latter is particularly vital to Team, Inc’s workflow, as it reduces file size during mesh export and makes things easier to share on Artec Cloud.
“Before, we would note down dimensions, take a photo of the page, and send it to engineers that rebuilt the geometry in SOLIDWORKS. These handoffs created opportunities for errors and the cost of poor quality to arise,” said Thistlethwaite. “With Artec Cloud, we can now upload data on-site and share it directly with colleagues at the office, who immediately start work on repairs.”
In order to repair, modify, and turn captured scan data into CAD bodies for clamp design on SOLIDWORKS, its engineers back at base use Geomagic Design X. The software’s advanced reverse engineering toolset is ideal for rapidly iterating upon existing product designs. Even so, the company continues to seek out even faster ways of creating bespoke repair clamps.
“We are making efforts to identify new ways of becoming more proficient on the software side – both through internal training – and with the support of our partner GoEngineer,” added Thistlethwaite. “In particular, we’re looking into methods of processing scans that could achieve the same results in a more efficient manner.”
Making urgent repairs faster
All Team, Inc’s technicians in the US now have access to a Leo, which they use to capture at remote locations before sending data to facilities across the company’s global footprint. Sharing 3D scans instantly has not only made it easier to meet typical enclosure deadlines of 1-2 days but allowed them to build up a record of captured designs that can be revisited for quality assurance.
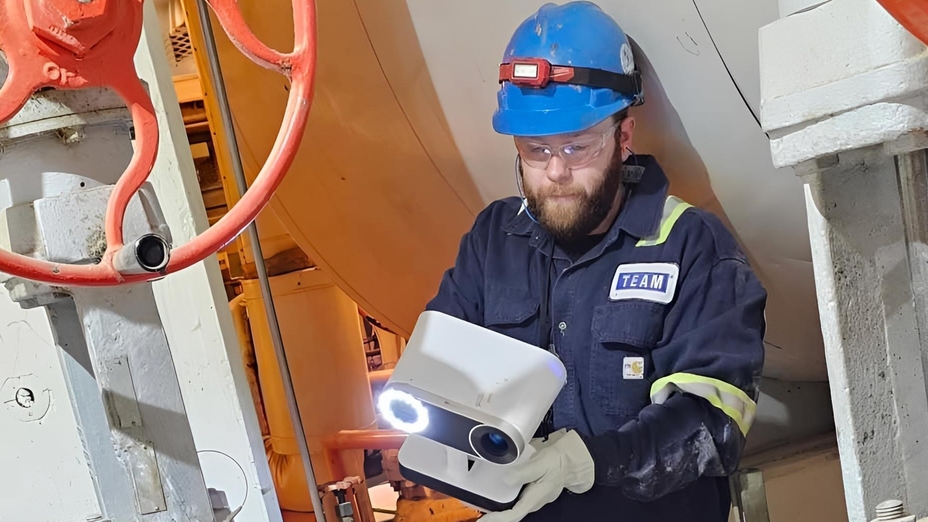
Artec Leo capturing additional facility data, just in case it’s required later in the job
Then there are the portability benefits. Leo’s unique wireless all-in-one configuration means that it can be used to capture anywhere in the world, with resulting scans shareable by WiFi. This ability to near-instantly share measurement data has enabled Team, Inc. to accelerate its manufacturing workflow and meet urgent customer needs at an unprecedented pace.
However, their seamless, multi-site data-sharing workflow remains under constant review, as they seek out new ways to repair client’s critical assets. Thistlethwaite says 3D scanning complex geometries has already become a no-brainer, and with Leo proving so easy to get to grips with, it could yet find new applications across Team, Inc’s business.
“Our technicians are particularly happy with the technology,” concluded Thistlethwaite. “They’re clambering over each other to use the 3D scanners – they love the speed, convenience, and accuracy!”
Scanners behind the story
Try out the world's leading handheld 3D scanners.