How Artec 3D & HP helped create a revolutionary 3D-printed prosthesis
Challenge: An innovative prosthetics specialist needed a way to create fast, millimeter-precise 3D measurements of molds of lower-extremity amputee residual limbs and other objects in order to guarantee a perfect fit for their revolutionary new 3D-printed Quatro prosthesis.
Solution: Artec Eva, Artec Studio, Geomagic Freeform, HP Jet Fusion 4200
Results: With the handheld 3D scanner Artec Eva, in just minutes, a patient’s residual limb, molds, and sockets can be scanned in submillimeter color 3D. From there, the scans are processed in Artec Studio software; then, just 30 minutes to an hour later, they’re exported over to Geomagic Freeform, where the customized Quatro prosthesis will be sculpted to life, using the Artec Eva scans as unerring reference models.

3D scanning Rustin Hughes’ Quatro prosthesis with Artec Eva
After losing his right leg to a vicious blood clot, U.S. Army combat veteran turned MMA fighter Rustin Hughes didn’t sit around and wait for good news to arrive.
He charged headlong into his grueling rehab sessions at the VA hospital, day after day. Soon he was out of a wheelchair and standing on two feet, one of them prosthetic.
Yet, in Hughes’ words, this first device “was terrible, like wearing a 5-gallon bucket around.”
A typical standard-sized suction socket, common among amputees the world over, the artificial leg never fit right, and throughout the day became loose, as Hughes’ residual limb decreased in volume.
This meant removing and refitting the leg multiple times a day, often placing a sock or two in the socket to achieve a temporarily snug fit.
All in all, this bothersome process takes nearly ten minutes to perform, making it next to impossible for Hughes to take part in athletic competitions, where the breaks between matches are only about a minute long.
Down for the count, but far from out
For an amputee, especially one with such rigorous physical demands on his plate, having a loose prosthesis was not just uncomfortable, but also a safety hazard. More than once, while doing his best to walk down the street, Hughes’ new leg wobbled loose and fell off.
Mired in frustration and pain, Hughes faced an uncertain future, with his plans and dreams hanging in the balance, yet he refused to give up.
He kept searching for a specialist who didn’t offer up simple answers and pre-made solutions. That’s when he met Joe Johnson, CEO of Quorum Prosthetics in Windsor, Colorado.
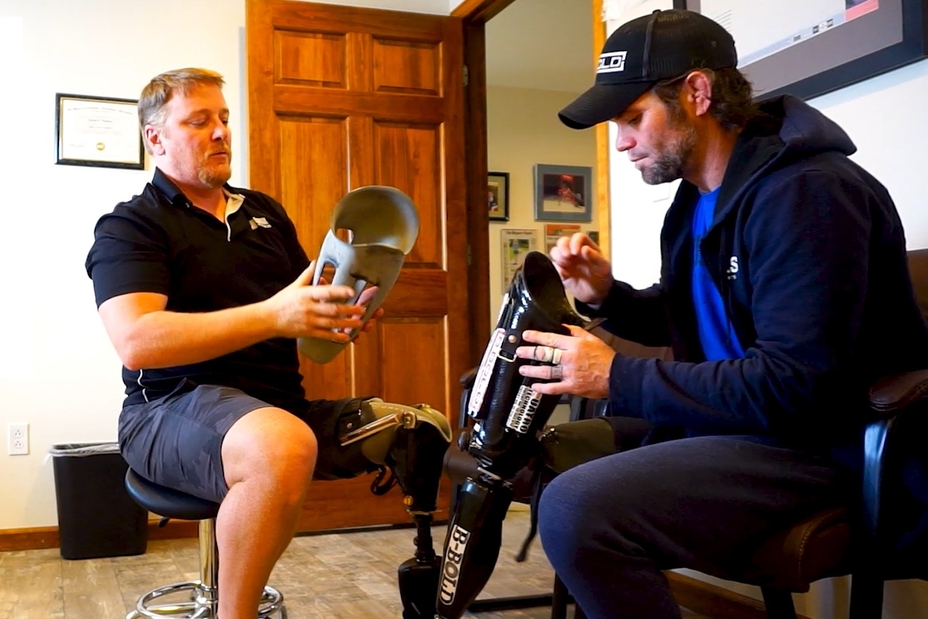
Joe Johnson (L) and Rustin Hughes with new Quatro and liner
In Hughes’ words, “Joe’s also an amputee, so he knew exactly what I was going through, how to verbalize it, and how to help move me from where I was, to where I needed to be.”
Johnson and his team at Quorum made a test socket for Hughes that same day. “They dropped everything to help me,” Hughes recalled.
Days later, when he put on his first carbon fiber Quorum Quatro prosthesis, “The contrast was massive.” Hughes explained, “My new leg felt like a natural extension of my body, and the fit was perfect. From there, my mobility level took a huge leap.”
Back in control with Quatro
While a few socket designs are able to provide the necessary bone stabilization to compete at a high level athletically, only the Quatro combines that with longitudinal compression. This allows the user to have all the advantages of a strong and secure socket, while still being able to make adjustments for changes in limb volume.
The Quatro is a stronger, lighter, sleeker, and fully adjustable socket that can be donned in a mere twenty seconds, then easily adjusted throughout the day, making it a perfect solution for competitive athletes as well as active people of all ages.
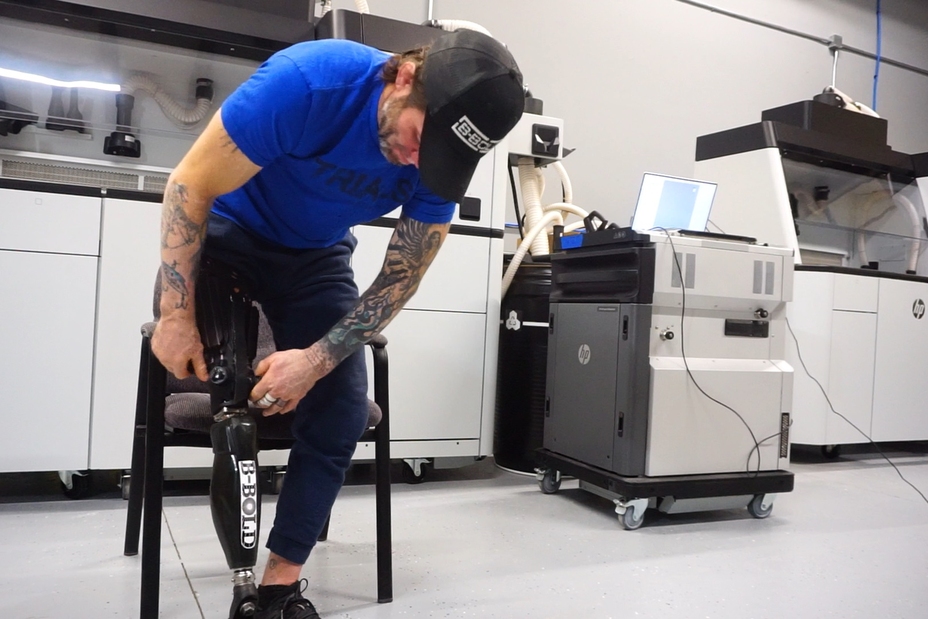
Hughes adjusting the fit of his Quatro
Every Quatro is fully customizable to a patient’s needs, including choices in accessories, design, and colors, with the price being on par with other popular prostheses available on the market.
This has made the Quatro a much-talked-about favorite among a growing number of patients around the country, and for good reason: regaining their mobility.
As Hughes explained, “For a long time, so much had been out of my control. Now just being able to tighten down my socket anytime I want and keep that close fit is totally empowering, because it puts me back in control, right where I need to be.”
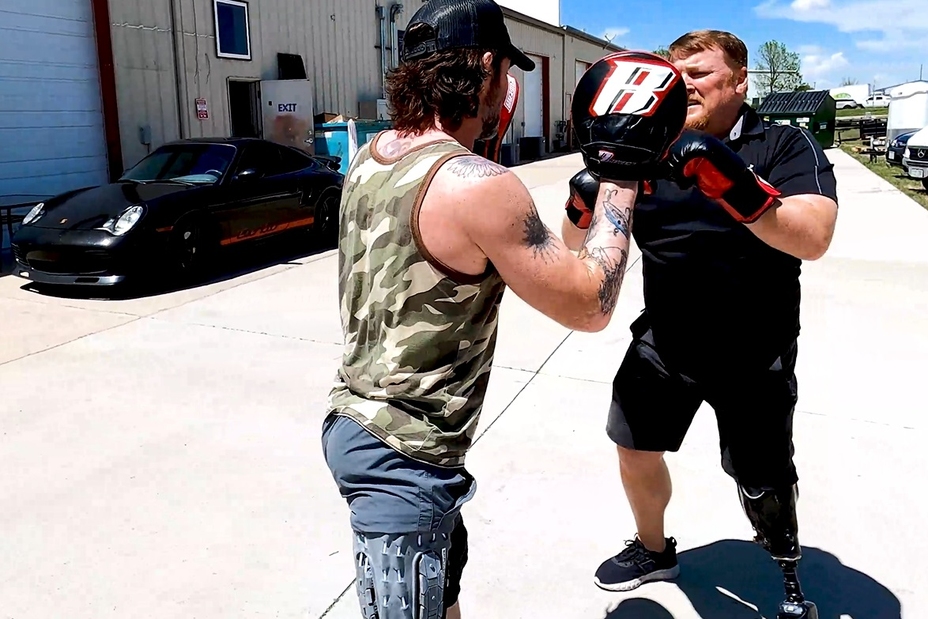
Boxing focus mitt training with Rustin Hughes and Quorum’s Joe Johnson
“Fit is truly everything”
But to achieve such an ideal fit in the first place requires that each patient’s device be created individually for them.
According to Quorum Prosthetics R&D Engineer and Director Sean McClure, “Fit is truly everything, as is maintaining that comfortable fit throughout the day, whatever level of activity is taking place, leisurely or vigorous. How we’re able to achieve that fit is via 3D scanning with our Artec Eva.”
Before they found their Eva, the traditional process that Quorum used involved casting a mold of the patient’s residual limb with plaster.
In McClure’s words, “This was a messy and time-consuming process, and never left a positive impression on our patients. The entire procedure took over eight hours, as well as significant amounts of materials and numerous tools.”
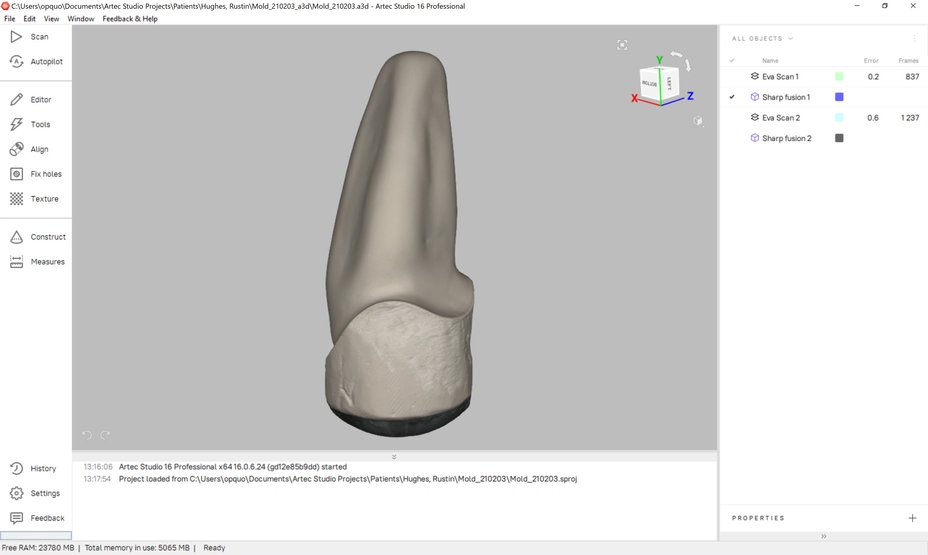
Artec Studio screenshot showing a residual limb mold scanned with Eva
Unsatisfied with the results, they made an initial foray into the world of 3D scanning. But after testing several low-cost 3D scanners, they became discouraged.
Both the accuracy and resolution of the captured data were well below Quorum’s standards, and the devices also failed to properly scan the inside of plaster molds or existing sockets.
“Try as we did, we were unable to modify and clean up the data to provide a better quality digital file for import into CAD, to design and model a well-fitting and functioning final product,” said McClure.
Finding the best 3D scanner for the job
When Joe Johnson mentioned his team’s struggles to Dr. Cory Christiansen of the CU Anschutz Medical Center, the latter recommended they get in touch with Artec Gold Certified partner Reality 3D in Denver, whose specialists have years of experience with orthotics, prosthetics, and other healthcare-related applications.
Soon after, Johnson and McClure met with Reality 3D’s Matt Filkins, who introduced them to the Artec Eva.
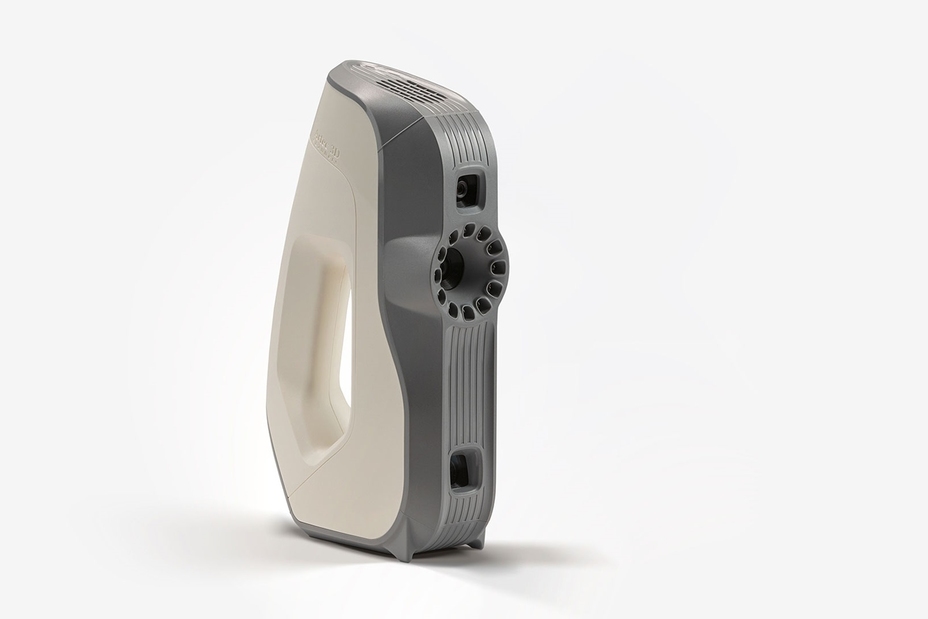
The Artec Eva
For years now, the Artec Eva has been a hands-down choice among prosthetists and many others in healthcare, and for good reason. Time and time again, the Eva has proven its ability to capture surfaces of all kinds, especially those of the human body, with a degree of accuracy into the submillimeter range, and an ease of use that delights both beginners and experts alike.
Initially hesitant because of the price of the scanner, just minutes into the demo, McClure understood that by streamlining their workflow with Eva, it would also markedly reduce their material costs, and the device would pay for itself within two months’ time.
So, they moved forward with the purchase and have never looked back.
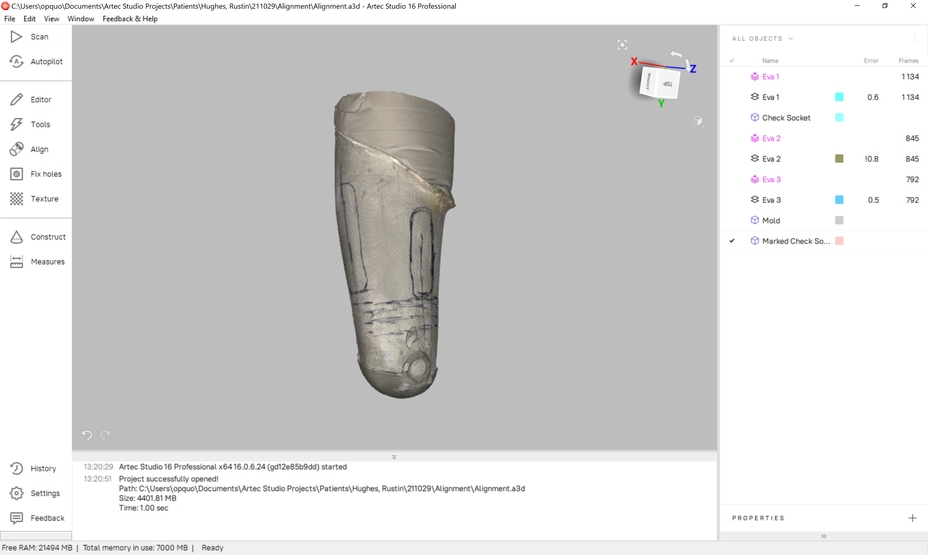
Artec Studio screenshot of a check socket over mold scanned with Eva
The results have been nothing short of phenomenal: “The time it takes us to create each Quatro has been cut by as much as 75% by switching to 3D scanning and printing.”
“Looking at all the time and materials saved, not to mention that now we’re expanding our market like never before, we’re already well past the breakeven point for these new technologies,” said McClure.
Saving hours of time on every project with Artec Eva
McClure continued, “With Eva, we can complete an entire scan in a matter of minutes, compared to the hours it took to properly create a plaster mold.”
“As we progress in our methods and understanding, we expect the time to go down even more. The scans are incredibly accurate, and this gives us the advantage of utilizing the 3D models from Eva for finite element analysis (FEA),” said McClure.
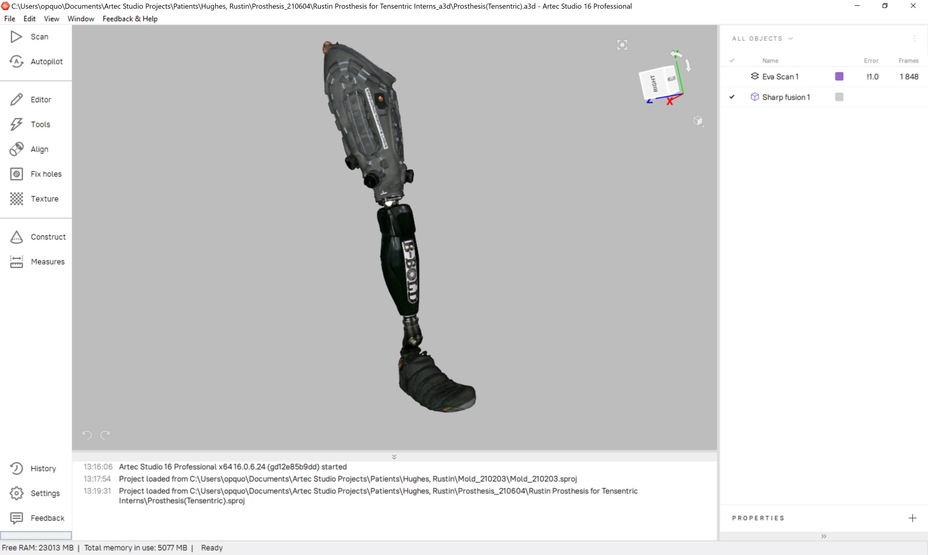
Artec Studio screenshot of an Eva scan of Rustin’s Quatro
The time required varies from patient to patient, and also depends on the objects being scanned: an existing mold, socket, the residual limb itself, etc.
On average, it takes between 30 minutes to an hour to go from beginning a scan, processing it in Artec Studio software, then exporting it as a complete STL file over to Geomagic Freeform.
Digitally sculpting the Quatro to life in Geomagic Freeform
In Freeform, all the STL models are brought together for the project. These include scans of a cast mold of the patient’s residual limb, their existing socket, diagnostic socket, and any other essential components needed for the Quatro.
At this stage is where the submillimeter accuracy of the Eva scans proves most crucial since these models will be used as reference guides for creating the multiple structural elements of the device before they’re arranged in their respective locations.
From there, the Quatro’s four adjustable zones of compression via four panels are easily aligned to the socket in the exact positions specified by the designer.
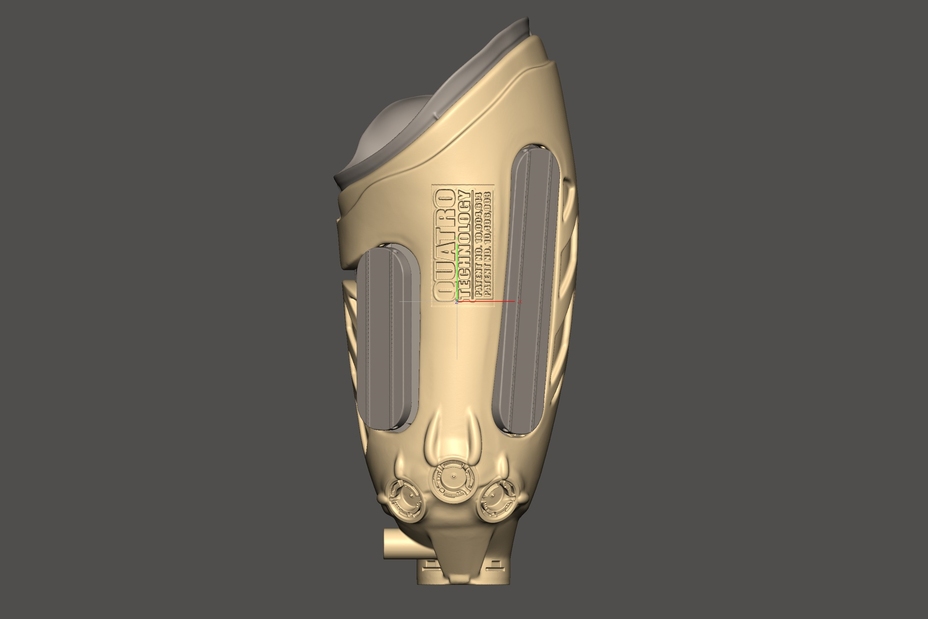
Geomagic Freeform screenshot of the Quatro design
Panel sizes and shapes are customizable, depending on the dimensions of a patient’s residual limb, as well as the type of compression and adjustability needed.
The panels are carefully modeled using traditional CAD tools available in Freeform. Following this step, after 3D printing all the components on an HP Jet Fusion 4200, the full socket can be assembled in as little as 15 minutes.
“It currently takes approximately two weeks to go from scan to finished Quatro on the patient. As we refine the process, we expect to get that down to a matter of days,” said McClure.
Standing head and shoulders above the pack
Although the Quatro is a relative newcomer to the market, initial feedback and studies have shown it to be considerably more durable and with a greater degree of longevity than traditional devices in its class.
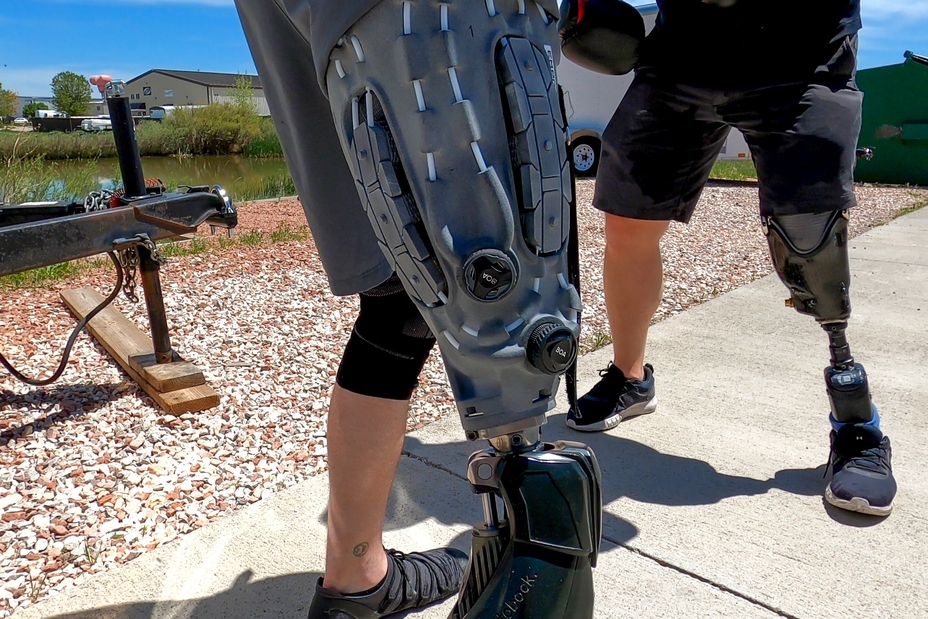
Hughes’ latest Quatro in action
Having the ability to conveniently adjust the fit throughout the day via a set of easy-to-reach dials on the device gives patients full control over their level of comfort and stability.
This, in synchrony with the superior strength and light weight of the 3D printed parts, translates into a socket that will be worn by patients for years to come.
Expanding their market across borders and continents
However, the benefits to Quorum’s practice go well beyond those of its many devoted clients. “Our Eva has allowed us to open up our market far beyond northern Colorado. Today, we no longer need a Quorum prosthetist and technician in the room with the patient,” said McClure.
“A facility anywhere in the world, by utilizing 3D scanning technology, can send us a model for design and printing. This means we can conduct business solely as a manufacturer and spread this technology across the country and the world.”
As for Hughes, with his Quatro dialed in to a perfect fit, he’s more active than ever, competing in the ring or running his nonprofit B-BOLD, where he teaches adaptive, non-contact martial arts exclusively to people of all ages with disabilities.
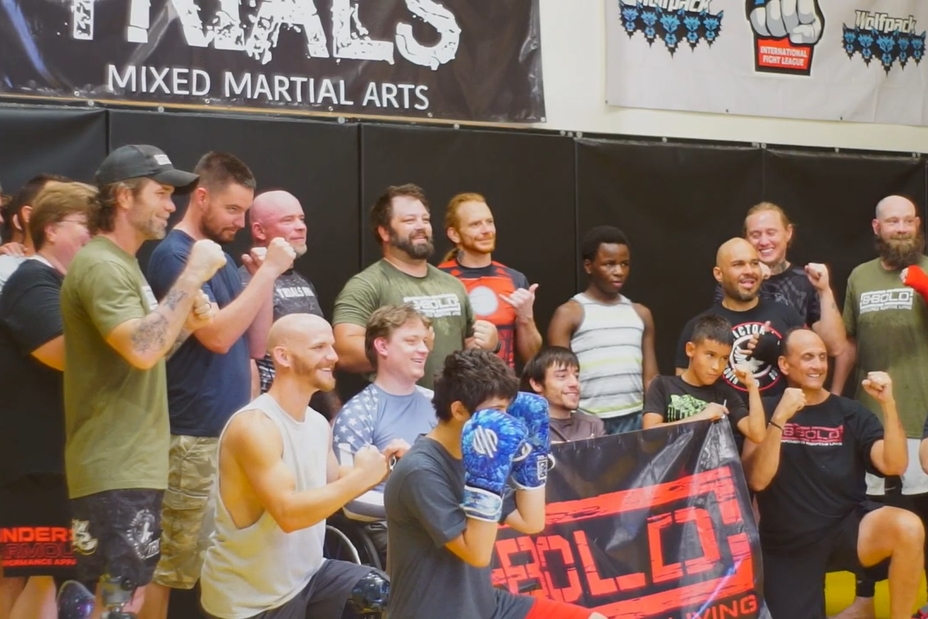
Rustin Hughes (L) with one of his Adaptive Boxing classes
The ever-accelerating need for 3D scanning in O&P
Reality 3D’s Matt Filkins commented on the potentials of the technology in the orthotics & prosthetics field: “If you look at the VA hospital system and their patient base as one example of the surging demand out there, you can see many thousands of aging veterans, amputees among them, in need of care for the rest of their lives.”
He continued, “3D scanning and printing offer O&P providers what traditional fabrication methods simply can’t deliver: superior accuracy and patient comfort, low material and labor costs, fewer office visits, exceptional design possibilities, and so much more.”
Scanners behind the story
Try out the world's leading handheld 3D scanners.