"Down from 20 hours to just 1 hour." Artec's 3D Space Spider shrinks processing time for Swiss chocolate bunny packaging
Summary: Facing rising demand for its products, a Swiss food-packaging manufacturer needed to drastically cut processing time and costs on smart packaging solutions for chocolate bunnies and Santas.
The goal: To slash production time, expenses, and challenges when creating new packaging, reducing the entire process from 20 hours down to an easy fraction of the time.
Tools used: Artec Space Spider, Artec Studio, Geomagic Design X
Artec Space Spider helps Swiss package maker save time and money.
While people certainly love their sweets, especially on birthdays, holidays, and other special occasions, packaging manufacturers follow the old adage – we eat with our eyes first. This is why they design beautiful wrappers for the Santa- and bunny-shaped chocolates that make their way to grocery stores worldwide at various times of the year. And, the more attractive their packaging, the higher their chances of ending up in shopping carts. Everyone wins.
Yet few truly know the gargantuan effort given to designing such complex packaging. And now with the ever-increasing trend for sustainable, custom-made packaging that is easy to manufacture, it only made sound sense for packaging manufacturers to turn to Artec 3D’s effective 3D scanning solutions.
This is exactly what Bachmann Forming AG did. Founded in 1966, Bachmann Forming AG is part of the Swiss family-owned company Bachmann with headquarters in Hochdorf, near Lucerne. There they produce to-spec smart packaging solutions of the highest quality, including the ones for those sweet, smiling chocolate bunnies and Santas you see in your local supermarket.
In order to enhance their workflows, Bachmann Forming AG has begun integrating Artec’s state-of-the-art 3D scanners into their production. Artec’s Official Gold Standard Reseller in Switzerland, 3D Model AG, supplied Bachmann Forming AG with their very own Artec 3D tools. And to get the company’s team up and going, they also provided them with full training. “It has never been so easy to get the shape of an object. We are very pleased that, with our support, our customers Bachmann Forming can now streamline and speed up their work process,” says Christiane Fimpel of 3D Model AG.
Artec 3D cuts out the lengthy process of manual molding
In the past, you had to create a master form or pilot tool, and up until ten years ago, most of the original models were done by hand. They were usually cut out with a hand milling machine or molded from plasticine then polished. All together the process could take up to twenty long hours, depending on the product.
So, how does a manufacturer modernize the package-making process for the modern chocolate rabbit?
The advent of digitization has the answer. Recent technology has dramatically revolutionized, if not entirely supplanted, this procedure. Pilot tools are now designed with the help of computers, i.e. CAD, and manufactured on CNC-controlled milling machines.
But Bachmann Forming AG was on the look out for a way to digitize organic geometries that combined incredible speed and precision. Given that food is usually produced without CAD data, finding a solution would be a big boon to the food packaging industry.
So in comes Artec Space Spider – one of Artec 3D’s best-selling, high-resolution 3D imagers…
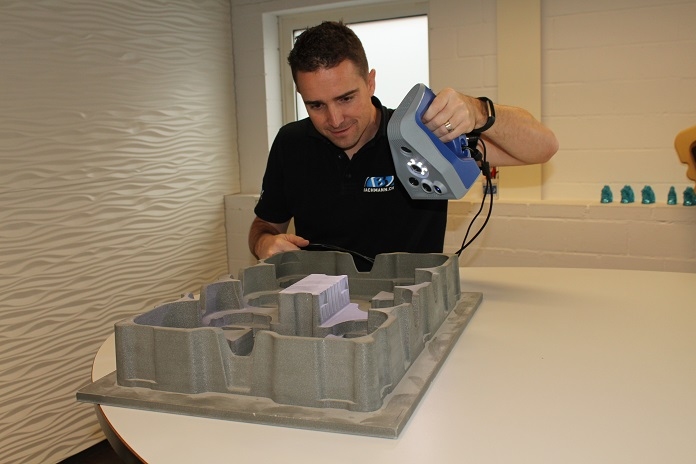
Jörg Nussbaum scanning a master form
Marker-free with Artec
Bachmann Forming AG often comes across objects that are too complex and time-consuming to be sized by hand. Even when some scanning solutions are used, this can still be problem. Often scanners require applying adhesive markers or orientation points to the object in order to maintain tracking and align scans. Clearly, with food, this would be impractical, as Jörg Nussbaum, a design engineer at Bachmann, points out, "Especially in the case of chocolate or pralines, it would be pretty hard to stick something on them."
No wonder Bachmann Forming AG turned to Artec’s Space Spider. "We were impressed by the easy usability and the geometry and texture-based tracking of Artec Space Spider," Nussbaum continues. "Capturing color also makes it easy to create photorealistic visualizations in the design phase."
Indeed, one of the key advantages of Artec’s devices is that, unlike other 3D scanners, their algorithms analyze both the geometry and color data of the object. And, there’s never any need to place targets on the object to capture its shape, textures, and colors.
For the final product, Bachmann Forming AG uses a thermoformal process. Here a plastic film is heated first to soften it. Once a vacuum is created, they pull the film over the master form, the small holes of which help draw in the film. By adhering to the model, it takes on the model’s shape. Then Bachmann Forming AG waits for the film to cool down and harden. Only once it becomes solid can it be peeled off.
Image series:
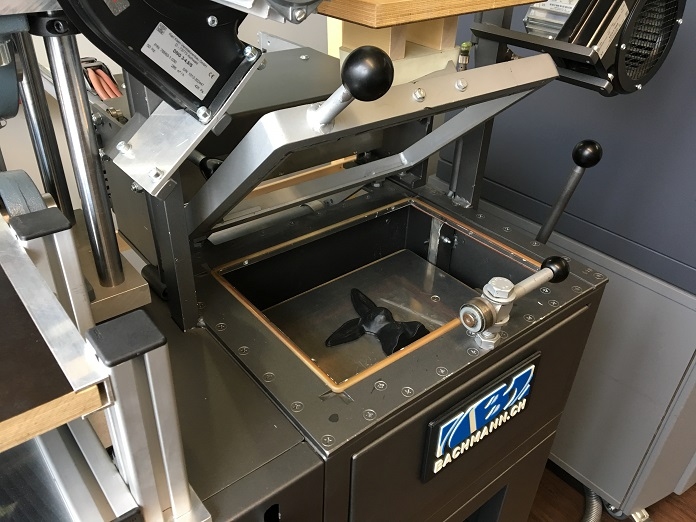
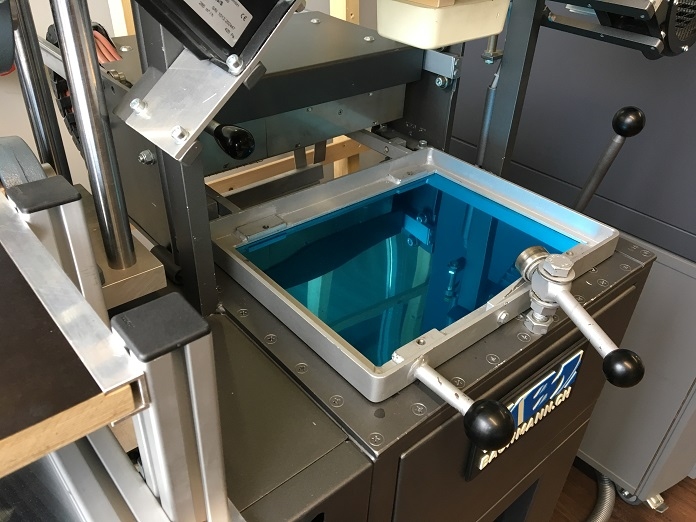
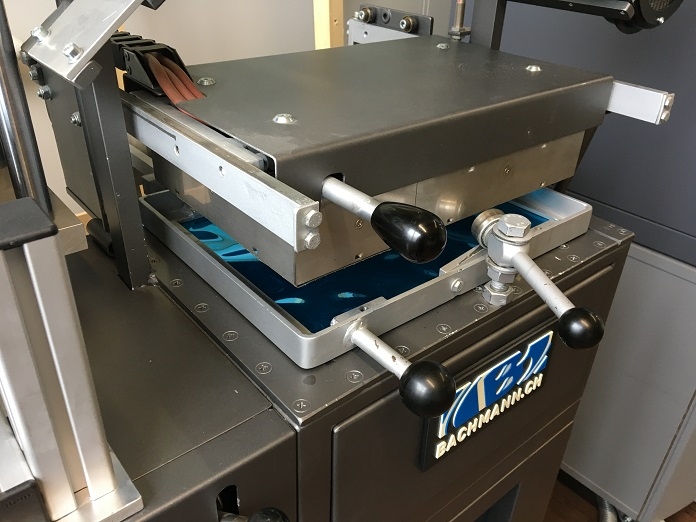
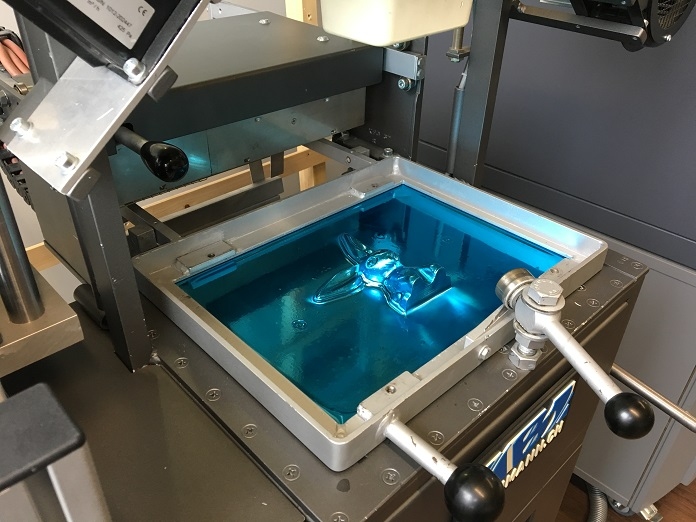
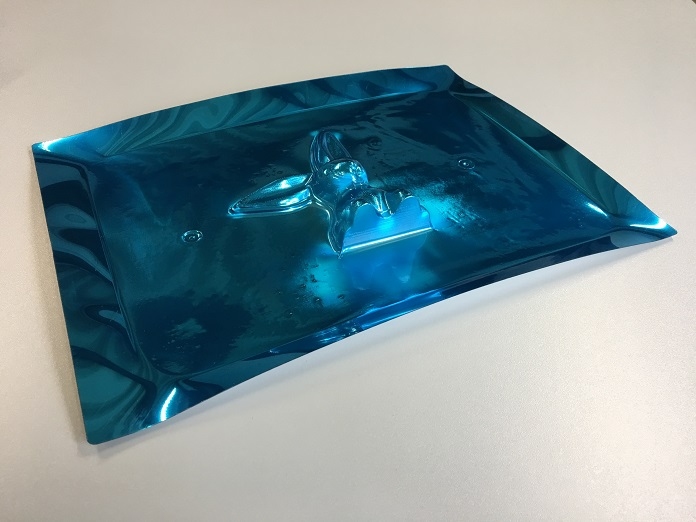
The chocolate bunny during the thermoformal process
Bunny scanning one hop at a time
Once the chocolate bunnies are delivered, scanning can begin. The bunnies are scanned from different sides, and the results are aligned on a computer. It’s worth remarking that the chocolate’s dark color poses no obstacle to capturing the bunny’s full geometry. Only for colorless, reflective surfaces is manual retouching done.
Artec Studio, the software complement in Artec’s scanning suite, processes the data received, which is then further reverse engineered in Geomagic Design X. Once finished, the data is exported as a solid (STEP data) or imported directly into the NX (Siemens CAD) via the CAD interface. For visualization, VRML data is created in Artec Studio and then rendered in Cinema 4D (3D graphics software).
All in all, it takes Bachmann Forming AG only one hour to complete this entire process. Should the traditional method be used, it would take up to 20 times longer!
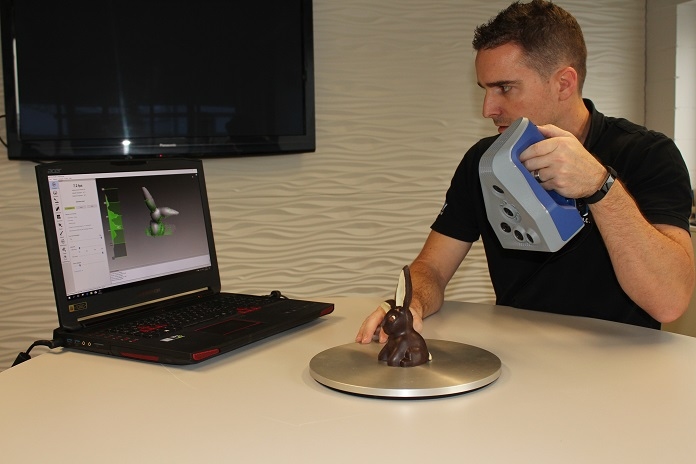
Jörg Nussbaum scanning a chocolate bunny
Artec Studio usually processes the scan data in autopilot mode, which performs the editing automatically. All the user has to do is answer a few simple questions about the object’s characteristics. Afterwards, Artec Studio deletes any unwanted data, automatically aligns the scans, and chooses the most effective 3D algorithms for the data. The result is an extremely precise 3D replica.
"It's fun to see how quickly complicated shapes can find their way from hand to screen. Being able to use a 3D scanner in house is an immense time advantage. The simple usability is a winning factor - we are very satisfied with the results," says Nussbaum, delighted.
Faster, cheaper, more precise
With Artec 3D scanners, you can make chocolate packaging that fits perfectly, and do it in house. "Before we had Space Spider, this kind of work had to be outsourced, which was very time-consuming and cost-intensive," says Nussbaum, looking back. "The external service provider scanned the chocolate bunny as it was, with all the details, so the 3D model also showed all the bumps that were in the chocolate. Now we can immediately intervene in the data processing stage and delete these parts."
Also, because outsourcing the imaging stage of production meant adding two extra weeks to a company’s turnaround time, it was a real drawback to business owners who felt increasingly outpaced by demand. With Artec’s high-performance technology in their arsenal, Bachmann Forming AG can now exercise tremendous control over their manufacturing needs and processes.
Nussbaum concludes, "When we do it ourselves we scan whenever we have time. In the packaging business you have to be fast and innovative. With Artec Space Spider we have found a tool that will help us with many upcoming projects."
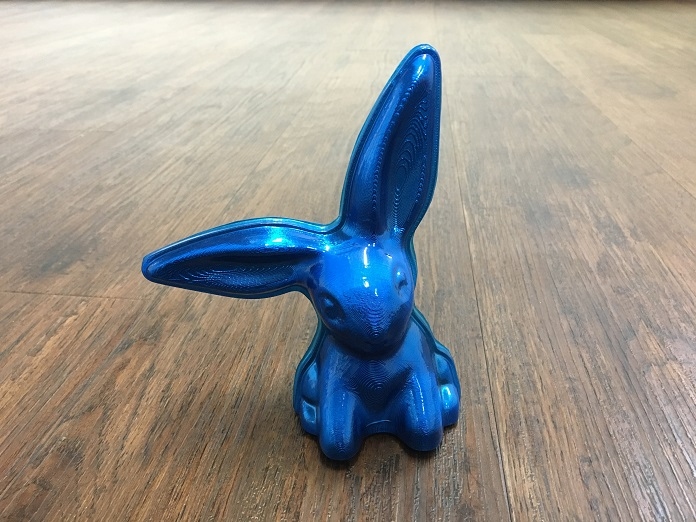
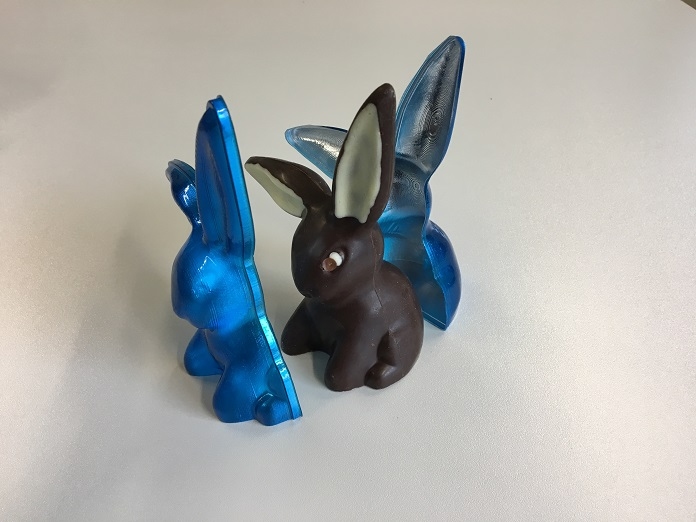
The chocolate bunny in the finished thermoform
Scanners behind the story
Try out the world's leading handheld 3D scanners.