Ausco Products ramps up heavy-duty brake system inspection with Artec 3D scanning
Challenge: Accelerating the process of inspecting externally sourced brake castings to ensure they’re dimensionally accurate and meet required tolerances.
Solution: Artec Leo, Artec Space Spider, Artec Academy, Artec Studio, Geomagic Design X, SOLIDWORKS, SOLIDWORKS SimulationXpress
Result: Switching from manual measurement to Artec 3D scanning has cut a 90-minute process down to just 20 minutes – a 78% reduction. This digitized workflow also makes it easier for Ausco quality receiving inspectors to identify issues that can affect machining operations, assembly processes, braking performance, and ultimately customer satisfaction.
Why Artec 3D?: The incredibly precise Space Spider repeatedly captures trustworthy measurements, while Leo’s accuracy and portability make it ideal for field deployment. Artec Academy also helps users maximize both data capture and processing with Artec Studio – a software packed with editing and analysis features for all but the most complex inspections.
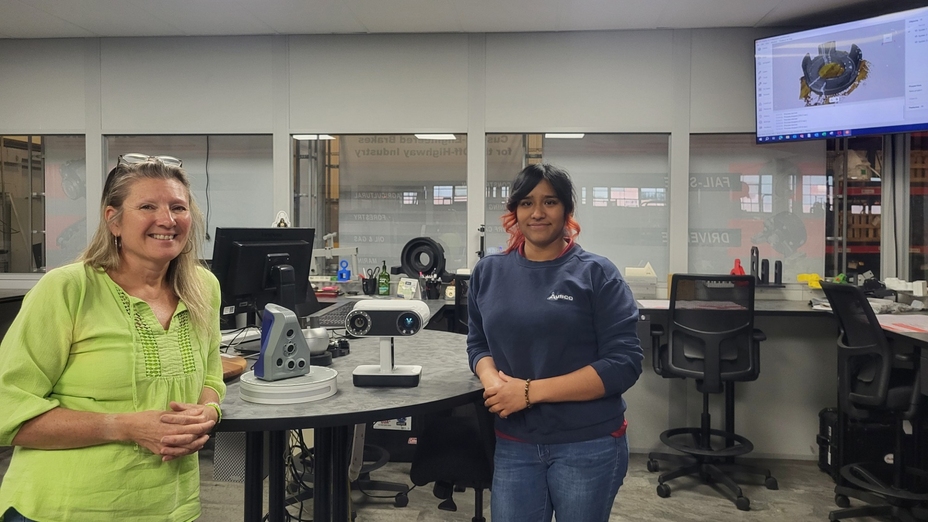
Ausco engineers Nancy Leonard and Veronica Moreno with Artec Leo & Artec Space Spider. Image courtesy of Ausco
For off-highway brake experts like Ausco Products, going through raw shipped-in castings with a fine-tooth comb is essential to responsible and efficient manufacturing.
Ausco specializes in developing high-performance custom brakes for customers globally in off-highway industries such as construction, mining, agriculture, forestry, recreation, and airport ground support. Naturally, vehicle braking systems are safety-critical, so thorough quality inspection and evaluation is vital to peak product performance and customer satisfaction.
In the past, the company would measure castings for analysis using tools like calipers and CMM machines, which only measure point location and dimensions. However, this labor-intensive process has now been optimized with Artec Leo and Artec Space Spider. Adopting Artec 3D scanning has allowed engineers to start evaluating entire surfaces, not just single points, and develop a more complete picture for better decision-making and communication.
Having signed up to Artec Academy, a catalog of expert-led online 3D scanning courses, its team is also continuing to optimize and explore new ways of applying the technology. With Ausco eyeing up even further efficiency gains, it seems like nothing can put the brakes on its digital manufacturing ambitions.
A less-trodden path to digitization
Many manufacturers end up adopting 3D scanning after an extensive search for efficient digital measurement solutions, which starts at the very top. But Ausco’s introduction was a little different – it was spearheaded by long-serving advanced technology engineer Nancy Leonard.

Leonard’s Artec Academy certificate, awarded for passing the Artec Eva and Artec Space Spider course. Image courtesy of Ausco
Leonard was first introduced to 3D scanning as part of a University of Illinois 3D printing course. Tasked by her lecturer with identifying a device possessing professional potential, she initially tried using the flexible, ultra-accurate Artec Eva. But, with Ausco sending a US-based engineer to South Africa for customer vehicle measurements at the time, her project quickly took on new dimensions.
Time-tested across industries, the lightweight, agile Eva would’ve been up to the task. However, Leonard sensed that it would be difficult to remotely deploy something with wires that relied on a separate display. That’s why she recommended that Ausco adopt the cable-free Leo, as well as the more precise Space Spider – one scanner for complete capture freedom and another for taking on the most complex use cases.
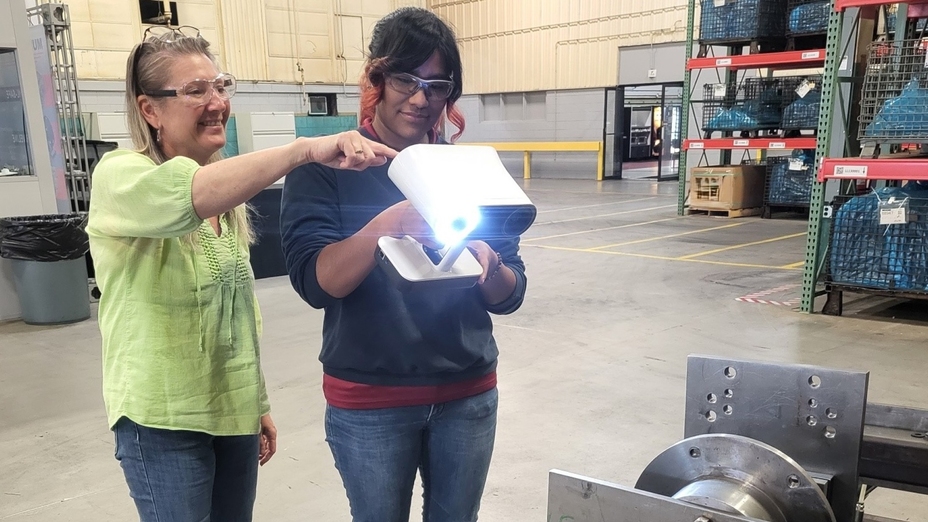
Leonard and Moreno utilizing Artec Leo’s built-in display to check data capture in real time. Image courtesy of Ausco
Now charged with training colleagues to get the most out of these devices, Leonard says Leo is especially easy to grasp, allowing for rapid, accurate data capture at the click of a button.
“The fact that its power supply is onboard, it’s all packed into one lightweight design, these are absolutely huge wins,” said Leonard. “It’s also so easy to use. You can see what you’re scanning right there. All I have to do is teach colleagues how to capture good data with its built-in display – if it’s green, it’s good – it’s as simple as that!”
Mesh mastery with Artec Academy
Much of Ausco’s inspection workflow now takes place in Artec Studio. At first, Leonard only used the software’s core data capture and processing capabilities, but completing the Artec Studio module on Artec Academy introduced her to many of its more advanced features.
Using distance mapping, for example, Ausco can now instantly tell if a casting has been manufactured to specification, while section analysis makes finding deviations quick and easy. With Artec Studio’s primitive tools, its engineers can even create basic geometries without having to export to third-party programs – further ramping up their inspection workflow.
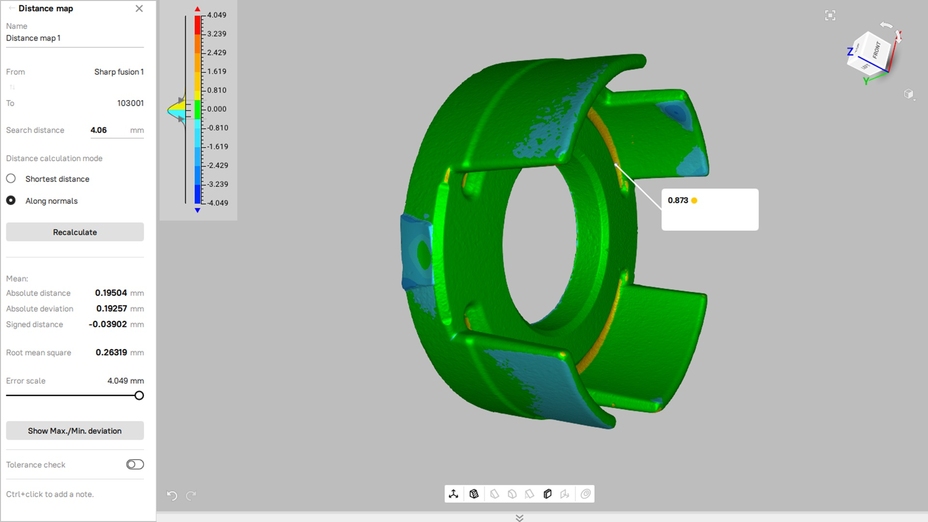
A piston casting being inspected with distance mapping in Artec Studio. Image courtesy of Ausco
That said, when tackling especially complex use cases, including those that demand higher-level features, Leonard and her colleagues still send scans to Geomagic Design X. Artec Gold-certified partner GoEngineer has been central to optimizing this part of their workflow, offering the training and support needed to fully utilize both 3D scanning and CAD surface generating software.
One key feature has been SOLIDWORKS LiveTransfer, which allows Ausco to seamlessly send parametric models for iteration while retaining all the constraints set up in Design X. Its team has also begun trialing SimulationXpress, an in-depth stress analysis tool for evaluating part performance, reducing test iterations, and increasing design confidence.
“Recently, I was training one of our engineers Veronica Moreno to use Leo. She needed to scan an irremovable plate for a torque stand. There were holes everywhere, the thing was like a piece of cheese!” explained Leonard. “We created a set of primitives and exported straight to SOLIDWORKS. That whole process took just two days and most of the work was back end.”
“With SimulationXpress, we’re also able to apply different forces to ensure that plates can withstand torque demands. It’s a pretty exciting area and we’ve got lots of room left to run with it.”
Optimizing industrial work cells
Ausco’s inspection workflow is now so rapid that its team can tell if a casting meets tolerances in well under an hour. But they don’t just use Artec 3D scanning for inspecting castings – the technology also allows them to check if brakes will fit into tight areas such as wheel wells, in a way that accelerates product customization and ensures product compliance.
In fact, Leonard says Leo has proven such a capable digital measurement tool – in some cases capturing parts just 0.006” (0.015mm) in size – that it still has significant untapped potential. While Ausco is considering investing in a 5-micron accurate Artec Micro II, for inspecting the most intricate tiny parts, it’s also thought that Leo could unlock opportunities at customer sites.
With manufacturing work cells, for instance, optimally positioning factory resources is key to improving productivity. The ability to take the compact, all-in-one Leo out to customers could allow these to be digitized for virtual optimization or planning upgrades to tools like torque stand plates.
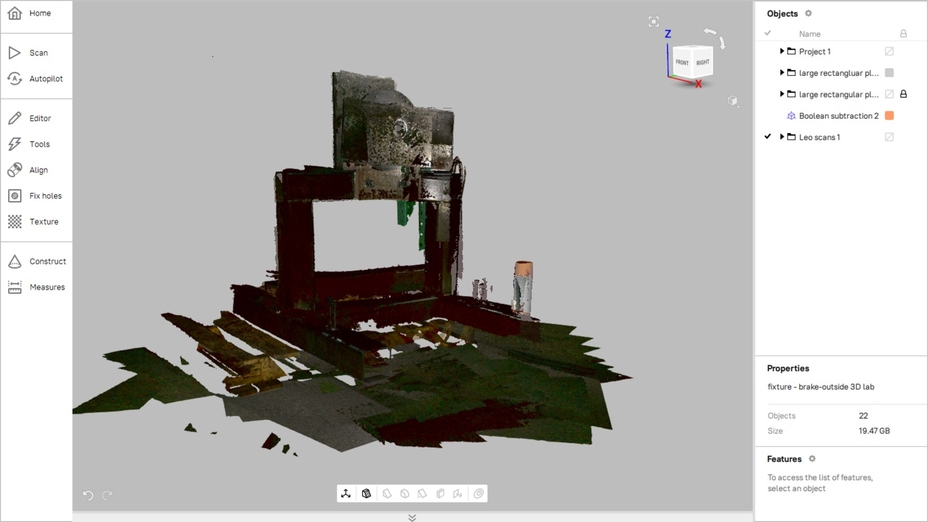
A torque testing stand captured by Leonard and Moreno with Artec Leo in Artec Studio. Image courtesy of Ausco
“I can see us going out and helping our manufacturing engineers bring their older work cells into CAD,” concluded Leonard. “That way, they can update plates, move palettes, and optimize by virtually moving things around the cell.” As they build up experience with larger scans and Leo-captured models out in the field, the concept of reviewing customer data live, on-site is seeming increasingly promising for Ausco and its talented team.
“We get all the information needed to make decisions with Artec 3D scanning. Right now, we use Space Spider more but Leo’s growth potential is pretty exponential.”
Having gone from honing her skills on Artec Academy to applying Eva, Space Spider, and Leo in ever more daring ways, Leonard is herself a case study in 3D scanning discovery. By sharing this expertise with colleagues, she’s now sowing the seeds for further cost and lead time gains at Ausco Products, where they continue to push boundaries in product engineering and inspection.
Scanners behind the story
Try out the world's leading handheld 3D scanners.