Artec scanners take flight for the US Air Force Advanced Manufacturing Olympics
Challenge: To demonstrate 3D scanning and modeling technology as part of the US Air Force Advanced Manufacturing Olympics, and to identify how 3D scanning can provide fast and accurate reverse engineering solutions.
Solution: Artec Eva, Leo, Space Spider, Artec Studio
Results: Taking home a bronze medal using only Artec scanners in a nationwide challenge with hundreds of participants.
When the team at 3D Printing Colorado first came across a LinkedIn post about a scanning challenge with an impending deadline, they knew it was something worth checking out.
“We did some research on the event and thought we would be a good fit to compete,” Marketing Coordinator David Cano recalled. Having been accepted to a 3D scanning reverse engineering challenge called “Box of Parts,” the competition was on. “We thought we were well equipped to provide some viable competition in this space… so we went for it!” he said.
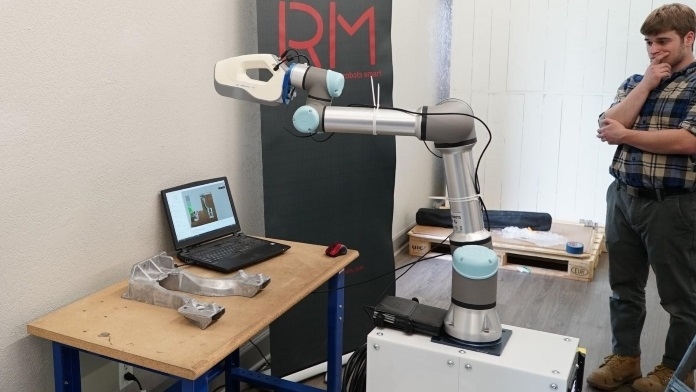
3D Printing Colorado’s Nick Conklin observes Artec Eva working with a robotic arm.
The parts in the box were mostly mechanical, and ranged in materials and surfaces from shiny steel to dull rubber. With such a variety, the team decided that they knew just what was needed: an equally varied range of Artec 3D scanners. For scanning all items in the box, they used Artec Leo, Eva, and Space Spider. In collaboration with the Artec scanners, a Universal robotic arm was used.
“We used the combination of a MiR (Mobile Industrial Robots) cart and a robot arm to experiment with possibilities of automation,” Cano explained. While most of the scanning was done manually, the team was here able to see what was possible with the robots and 3D scanning.
This highly precise automated scanning station saves time and reduces all risk of human error, intuitively capturing and providing the best results in the least amount of time.
Cano said, “We made a great case for ourselves by leveraging our deep industry experience, Artec 3D Gold certified accreditation, 3D scanning equipment and software tools, unique innovation ideas, and great video content to showcase our skills.”
And while the team was up against some stiff competition – including large teams, companies who had paired up, those who had budgets in the millions, or access to far more resources – the 3D Printing Colorado team were armed with Artec scanners and ready for the job. “It was just the five of us, and we used the skills and tools that we had to compete against some very strong competition,” said VP of Sales and Marketing Nick Yosha.
“Besides the scanning competition, we had to run a business the entire time as well. If we had been using any other scanners or software, that would have been really, really hard to do.”
With a range of Artec scanners in play, the team was able to match the features of each scanner to the object and its more challenging parts. In some cases, scanners were paired up for the best results. For example, an engine part known as a Rear Engine Frame Gas needed a combination of scanners and expertise. “With this part, we demonstrated our scanning expertise well, as we used a combination of scanners to capture data with very high accuracy in the shortest time possible,” said Applications Engineer II Nick Conklin. “We used the Leo to quickly take a composite, then infill with high-accuracy scan data from the Spider.”
“Most of the scanning, thanks to Artec scanners, was just a quick and easy experience,” added Cano.
Artec Leo, the first 3D scanner to feature onboard processing, lets you see the 3D replica being built in real time on its rear touch panel screen. There, you can rotate the 3D model, make sure you’ve captured all the surfaces of your object, and fill in any parts you may have missed. This gives you the easiest and most intuitive workflow. With HD Mode, you now can expect even more: Fine lines, sharp edges, and complex geometry perfectly captured, twice the resolution, and plenty of features designed for effectively capturing intricate details and tricky surfaces.
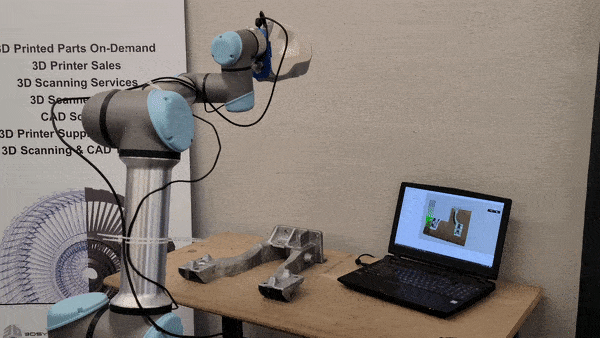
A robotic arm saves time and reduces risk of human error.
For other parts, individual scanners did the job. When scanning chain-operated wheels for overhead valves, internal geometries were difficult to scan without proper angles or rigging, Conklin explained. “This part also had multiple moving components that had to be disassembled to scan properly,” he added. “We used the Spider exclusively for this one.”
First designed for use onboard the International Space Station, the aptly named Space Spider is a high-resolution 3D scanner that employs blue light technology. Space Spider specializes in capturing small parts, as well as intricate details of larger parts, and all in high resolution.
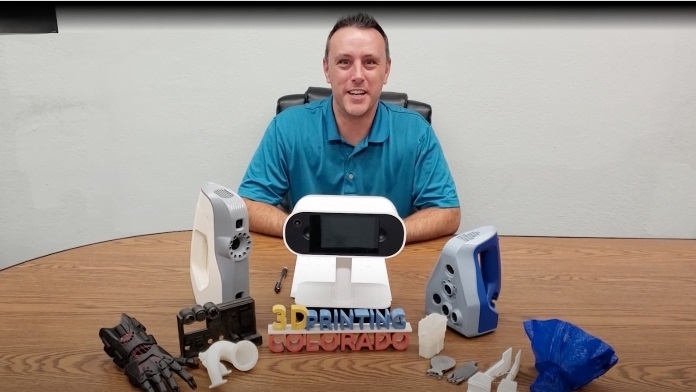
Introducing some of the Artec family: Nick Yosha of 3D Printing Colorado and Artec scanners Eva, Leo, and Space Spider.
And while some parts presented a few challenges, they were nothing that the team and their scanners couldn’t easily approach and complete, leaving them extra time for a bit of fun, too.
“This was our first time scanning these parts, but we do have experience scanning mechanical parts in general,” said Conklin. “Overall, the scanning part was a breeze. We finished all scanning the first morning of the competition. Any other scans were for video b-roll footage.”
As part of the first-ever Advanced Manufacturing Olympics, the scanning challenge points to the Air Force’s interest and growing utilization of 3D scanning in the aerospace industry. This ranges from the digitization of legacy components and in situ repairs through the scanning of damaged parts, to the enabling of legacy components to be taken through topology optimization workflows for fuel reduction and increased performance, among other uses.
“3D scanning already plays a huge role in aero,” Conklin said, pointing to faster innovation, development processes, and more accurate simulations. And that’s just for now. Looking to the future, there are countless ways in which 3D scanning can soon be incorporated into Air Force operations, including being able to analyze enemy locations quickly and accurately, as well as enabling space repairs without being tied to ground engineering teams.
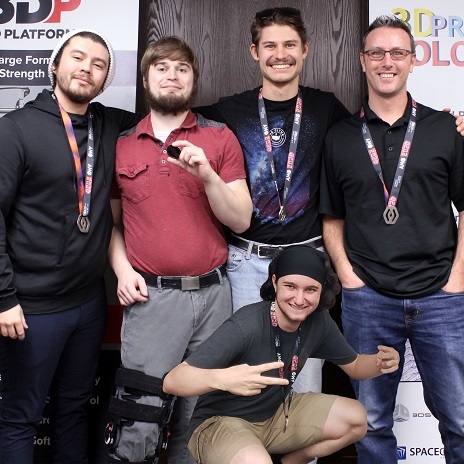
The happy team showing off their medals, which they also plan on 3D scanning.
“Competition sparks innovation in general, so I thought it was really clever of the Air Force to throw a bone into scanning and manufacturing, and have the best of the best in the country compete to find the best solutions for them,” said Cano.
As the team looks forward to receiving their unique 3D-printed bronze medals (they plan on 3D scanning these too!) they’ve already set their sights on next year’s competition. “We had a lot of fun, and we totally want to do it again,” Yosha said.
“It was a blast,” Cano added. “And we’re going for first place next time around!”
Scanners behind the story
Try out the world's leading handheld 3D scanners.