Artec Leoを用いたヘルキャット性能を装備した 一九五七年製インターナショナルメトロバンの製作
課題:生産の終了している自動車のパーツや部品を一から製作する過程を、品質や精度を犠牲にせずに大幅に効率化し、簡素化すること。
ソリューション:Artec Leo、Artec Studio、Autodesk Alias、及びSOLIDWORKS
結果:Artec Leoによるスキャンデータを参照しながら、製作やプロトタイピングにすぐに使用できる、全く新しいCADモデルを古い現存するパーツから製作することで、その所要時間は数日からほんの二,三時間までに短縮された。
なぜArtec 3Dなのか:Leoは、他のスキャナでは不可能な自由度をScratch Buildに提供している。データのキャプチャに必要な時間は削減され、より多くの時間をCADモデリングや設計、プロトタイピングに費やすことができる。
背景
五歳の頃から、チャッド・フォワード(Chad Forward)は何かを創り上げたいと思っていた。十五年もの間、オーストラリアの一流の自動車設計企業に務め、個別製作の自動車製作会社で設計コンサルタントをしていたフォワードは、自分の好きなことである自動車の製作に引き続き携わるため、自身の修理企業であるScratch Build Coを立ち上げた。
フォワードが週末に専念することができる社外活動用として二〇一二年に設立されたScratch Buildは、今や正規の設計企業兼共同作業スペースとなっている。そこでは、フォワードと仕事仲間である自動車設計者や技術者、電気技師などの下請け業者が、自動車製品や個別製作の乗用車などの補修部品分野の製作者に向けた設計ソリューションの作成に当たっている。
「自身の創り上げようとしている物に夢中になっている人々に、いつも憧れていた」と、フォワードは語る。「トヨタやフォードなどの設計企業で、驚くべき職人や素晴らしい設計者の方を身近で見ているうちに、このような人々を雇った上で、誰もが参加でき、オーストラリアの自動車市場にプラスになるものを製作していく場所を作り上げるチャンスが、はっきりと見えてきた」
その企業名が示すように、フォワードの業務の多くは、扱う物品が購入不可能となったパーツであっても、クライアントが再編成しようとしている工程全体であっても、何かをゼロから創り上げることを伴う。二〇一七年までは、フォワードの通常のリバースエンジニアリングのワークフローには、具体的な製作物を伴わない場合でも非常に時間が掛かっていた。「時には、基本的な寸法を得るためにシャシーを計測して、その情報を基にCADでモデルを完成させるのにさえ、丸一日掛かった」とフォワードは付け加える。「すべての作業を素早く引き受け過ぎて、非常に大事な作業を忘れることも度々あった。そのため、工程を数回行ったり来たりしないといけないこともあった」
「Artec社の最先端技術による完全携帯式スキャナであるLeoは、3Dスキャン産業における大きな進歩である」
Artec社がその二〇一七年にワイヤレスの携帯式3DスキャナであるArtec Leoを発売すると、フォワードは直ちに購入へと動いた。「二十年前、初めての個別製作の自動車製作業務に携わった時には、このようなテクノロジーを自分の生きている間に目にすることなど、考えもしなかった」とフォワードは話す。フォワードは、Artec社のオーストラリアの販売代理店であるObjective3D社を介してスキャナを先行予約したが、代理店チームによると、フォワードはその当時に最初にスキャナを手にした、幸運な顧客であったそうだ。
「Artec社の最先端技術による完全携帯式スキャナであるLeoは、3Dスキャン産業における大きな進歩である。Objective3D社の我々は、このテクノロジー機器をオーストラリアやニュージーランドの市場に誇りを持って提供している」と、Objective3D社の最高経営責任者のマット・ミニオ(Matt Minio)は語る。「リバースエンジニアリングを施すパーツに使用し、その車両の走行への影響を確かめることができるため、自動車技師の方には特に役立つスキャンである」
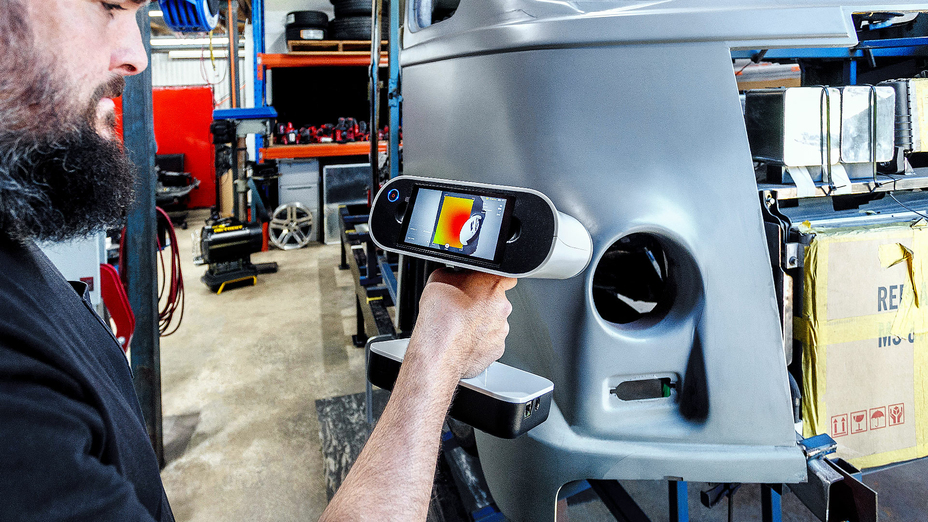
Scratch Buildの創立者であるフォワードはArtec Leoにより、どんなパーツも簡単に計測することができるようになった(画像提供:streetmachine.com.au)
機動性と使い易さを想定して設計されたArtec Leoは、PCもラップトップも必要としない、パワフルで唯一無二の3Dスキャナである。Leoはその広い視野により、保証された精度と並外れた解像度で、中規模から大規模の産業パーツや車両全体を三次元でスキャンすることが可能である。
このスキャナは自動オンボード処理機能、ワイヤレス接続性、内蔵タッチスクリーン及びバッテリーを搭載し、完全自律性で、個別注文車両製作所や工場の生産現場、電力へのアクセスの無い遠隔地など、どんな場所でも自由に稼働することができる。
フォワードにとっては、簡単な決断であった。「3Dプリンターに四千ドル投資する必要があると、自分を説得するのには四年もかかったが、四万ドルするスキャナの購入には十五分しか掛からなかった」
作業への着手
スキャナが手元に到着すると、フォワードは急いでそれを業務で使用し始め、未だにその使用を続けている。Leoはフォワードの企業でも社外でも、車両関連の計測の必要のあるすべての物品のスキャンに使用され、フォワードや取引先の貴重な時間の節約に貢献している。フォワードは現在、そうして節約した時間を自動車のパーツや部品のスキャンデータを参照しながらのCADモデリングや設計、プロトタイピングに利用している。
「この一台の機器のお陰で、信じられない程の自由が手に入った。場所やパーツの複雑さに関わらず、簡単にデータのキャプチャを行うことができる」と、フォワードは語る。
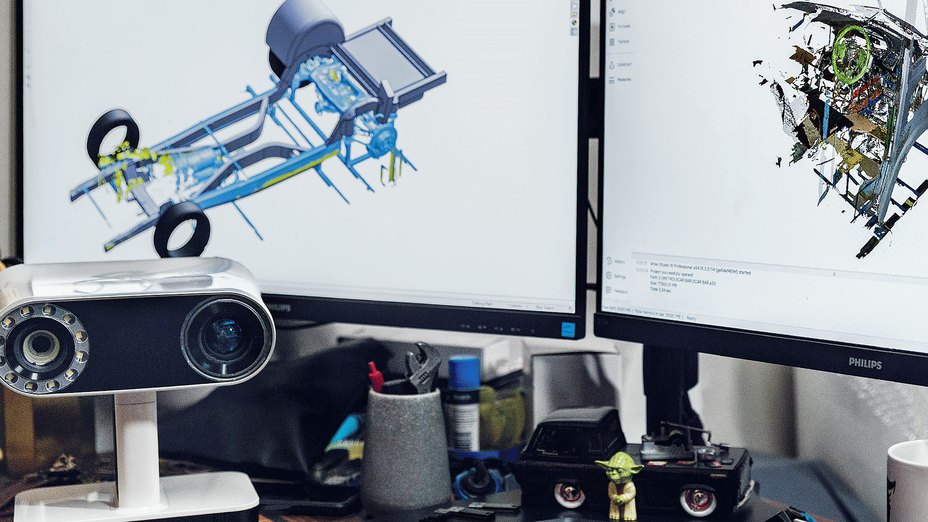
フォワードはLeoによるスキャンデータを参照用に使用して、SOLIDWORKSやAutodesk Alias上でCADモデリングを行っている(画像提供:streetmachine.com.au)
通常のワークフローは、次のようなものである。フォワードと設計仲間の一人が取引先へ車で向かい、スキャンの必要なものをすべてキャプチャし、Artec Studioでの処理専用に用意されたデスクトップコンピューターのうちの一台に、収集したデータを転送する。
「社内には、二つのデスクトップコンピューターがある。一つはすべてのスキャンデータの処理用で、二台目はCADモデリング用である。社内では常に何らかの作業が行われているので、このように並行してコンピューターを作動させておきたい」とフォワードは説明する。この後の作業では、スキャンした箇所により、フォワードはSOLIDWORKSもしくはAutodesk Aliasにデータをロードした上で、ソリッドCADモデルを作成する。
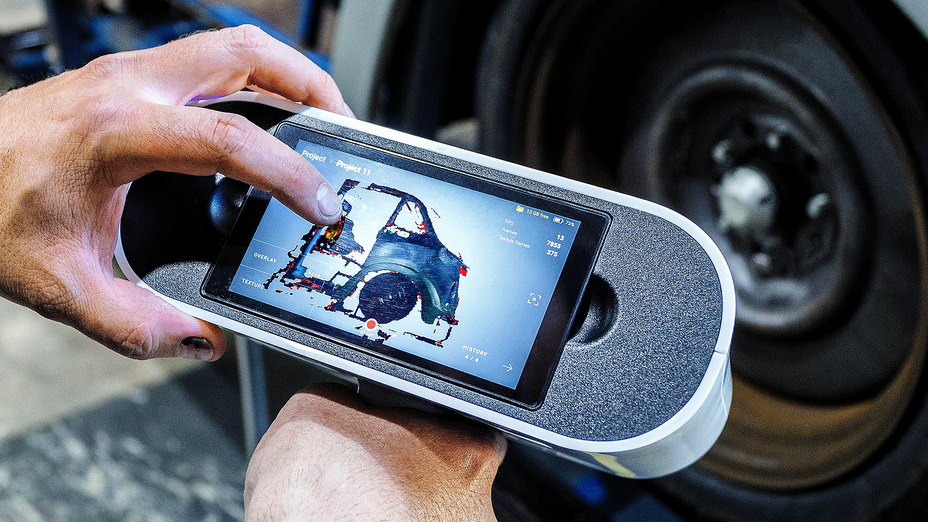
Artec Leoの内蔵ディスプレイにより、フォワードはリアルタイムでスキャンの結果をプレビューすることができる(画像提供:streetmachine.com.au)
取引先で3Dスキャナを使用できることにより、フォワードには新しい仕事のチャンスも入ってくるようになった。「Leoを社外での業務に持参する度に、一ヶ所の訪問につき、新しい仕事が一つ、ほぼ必ず手に入る。その取引先が別の取引先を紹介してくれて、紹介先の取引先がまた、別の取引先を紹介してくれる、という状況だ」と、フォワードは語る。現場では、フォワードはカタログのようなものを作成するために、市場ではもう出回っていないパーツからも貴重なデータを取得するなど、必要な数よりも多めのデータを収集している。
一九五七年製インターナショナルメトロバン
フォワードがこれまで手掛けたものの中で、スキャナを最大限に活用した最大のプロジェクトの一つは、社外の自動車製作所のビジネスパートナーであるルーク・ウィリアムス(Luke Williams)と共に二〇二三年末までに修復を完了するために作業中の、一九五七年製のインターナショナルメトロバンである。
バンの持ち主の要望は車両をそのまま改修するのではなく、過給6.2リットルHEMIヘルキャットエンジンを装備することにより、年代物の外観を持ちながら、スポーツカーの馬力をも備えた車とすることであった。
現在、最も強力な現代の『アメ車』であるダッジチャレンジャーSRTヘルキャットモデルに搭載されるV8エンジンは七〇〇馬力を誇り、バンの元のエンジンとは違い、持ち主が国中を自由にドライブできるような性能を持つ。エンジンの他にも、持ち主はヘルキャット標準搭載の電子機器や装置もすべて装備し、さらに、バンの丸々としたイメージを抑えるよう、デザインの調整をすることも依頼してきた。
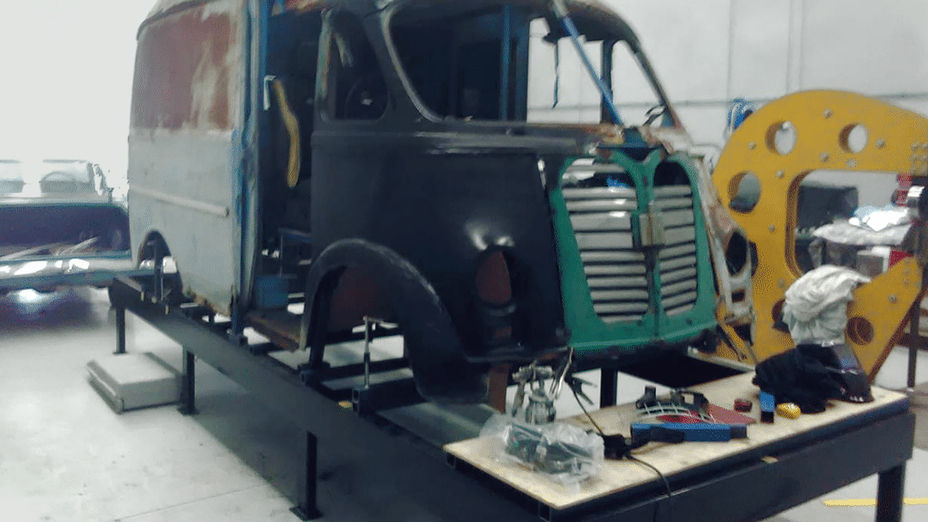
修理前の一九五七年製メトロバンの元の車体(画像提供:チャド・フォワード)
持ち主から設計技術上の要求をまとめて初期段階のスケッチをした後、フォワードとウィリアムズはある計画を思い付いた。バンの車体は修復するには使い古されている上に錆もひどいため、より古いが改良済みのパーツのスキャンデータを基にCADでパーツを新しくモデリングし、車両全体を始めから製作した方が速いように思えたからである。
ステップ1:車体のスカルプティング
作業の最初のステップは、車体を切断し、改造することだった。計画は、現存する車体もしくはパーツの一つを注文通りに改修し、そのパーツを3Dスキャンし、そのデータをCADで車体全体をモデリングする際の土台として使用する、というものであった。
そのために、ウィリアムズはアングルグラインダで工場の車体を切断し、それを少し異なった箇所に溶接し直し、多量の車体用の充填材や下塗り材を使用して、満足の行く艶消しのマット状のサーフェスを作成した。
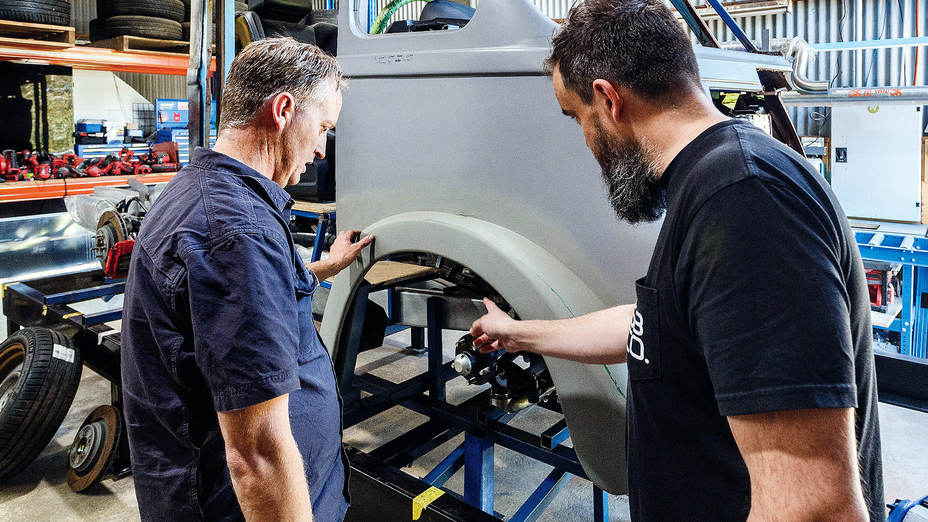
計画は、車体のパーツの一つを注文通りに改修し、そのパーツをCADで車体全体のモデリングを行う際に使用するために3Dスキャンする、というものであった(画像提供:streetmachine.com.au)
ステップ2:シャシーの製作
その一方で、フォワードはエンジン、すべての配線、前輪、後輪用サスペンションに至るまで、ダッジヘルキャットの動力伝達装置の部品を全部、シャシーの周りに組み立てたベースとなるプラットフォームに設置した。フォワードは、すべての部品の納まり、及び部品がADR(オーストラリア設計基準)に準拠しているかどうかを確かめ、また、スキャンすることにより、新しいシャシー用にどのパーツをCADでモデリングする必要があるのかを見極めたかったのである。
ステップ3:3Dスキャン
その後、シャシーやその他の車両内部の部品と共に、最も重要なバンの前面左の角部分をArtec Leoでスキャンする段階となった。スキャニングは数分で完了し、フォワードは後処理とSTLファイルの制作のために、Artec Studio上にすべてのデータをアップロードした。
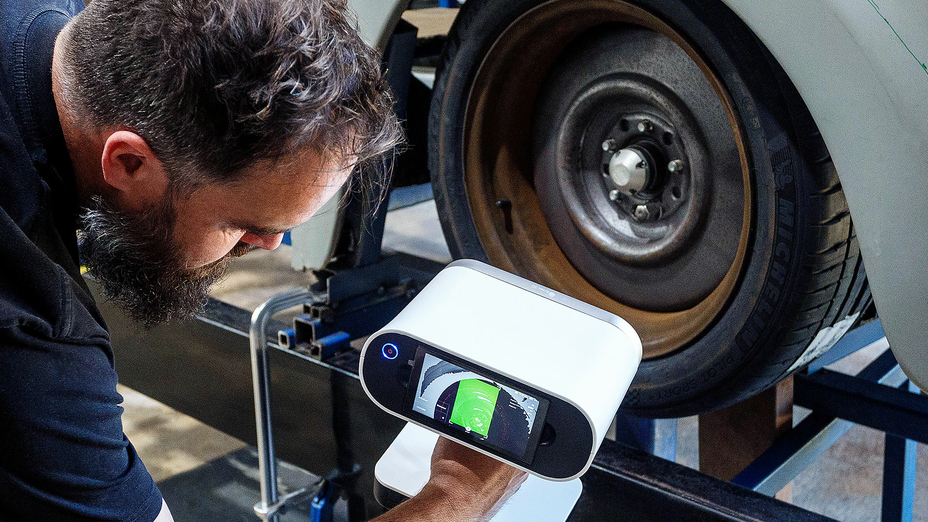
Artec Leoでバンのスキャンを行うフォワード(画像提供:streetmachine.com.au)
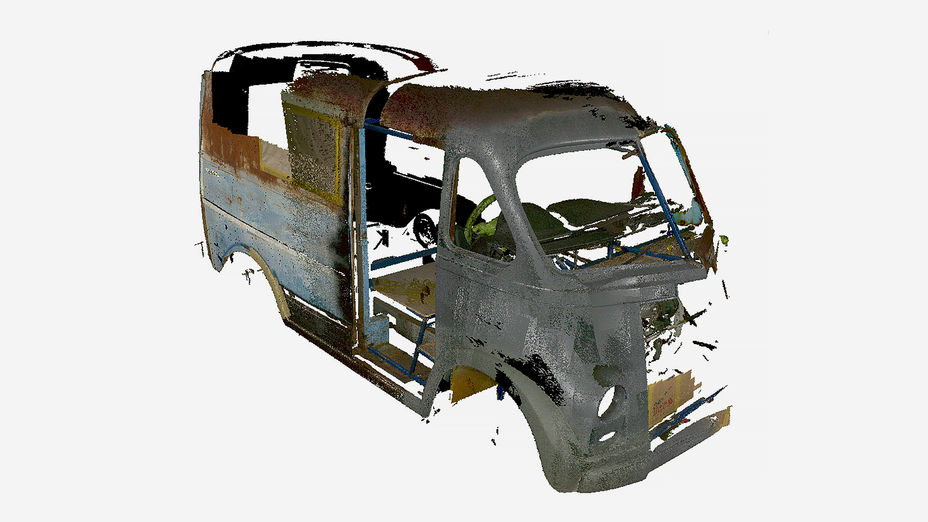
Artec Leoでキャプチャされた、改修された車体の3Dスキャンデータ
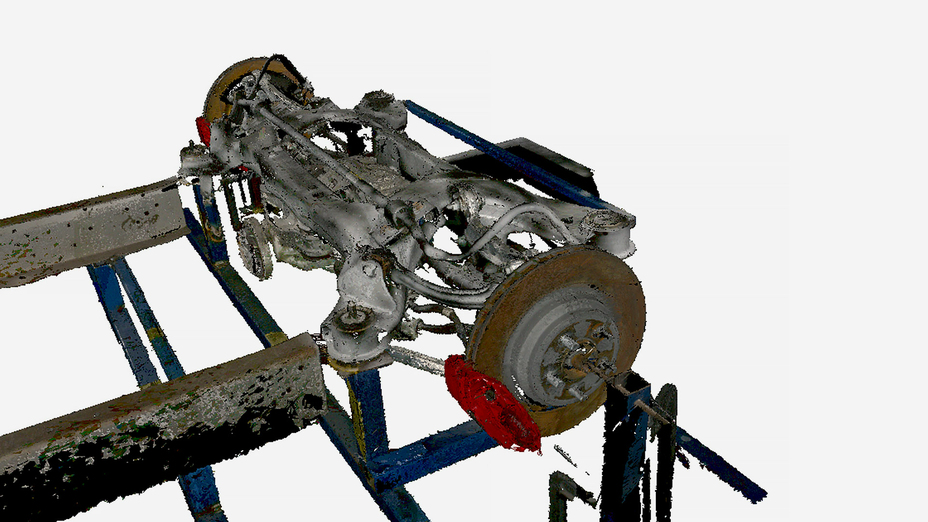
後輪用サスペンションの3Dスキャンデータ
ステップ4:バンの車体のモデリング
次の段階は、車体のサーフェスのモデリングである。フォワードは、自動車外観用のコンピューターベースのインダストリアルデザインソフトウェアであるAutodesk Alias上にArtec Studioからのスキャンデータをインポートし、データを青写真として使用しながら製作中の車体のサーフェスのスケッチを作成した。
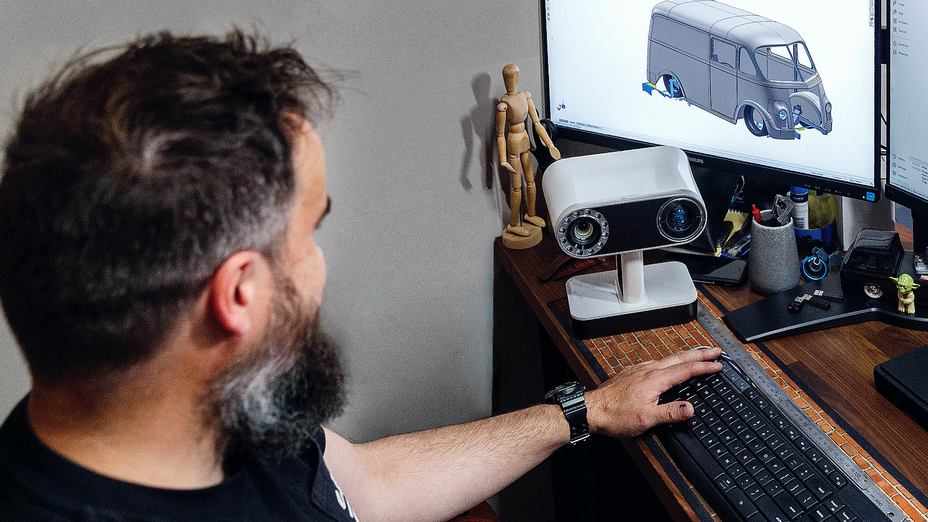
フォワードはAutodesk Aliasを利用し、スキャンデータの上面からの自身のスケッチを基に車体のサーフェスを作成した(画像提供:streetmachine.com.au)
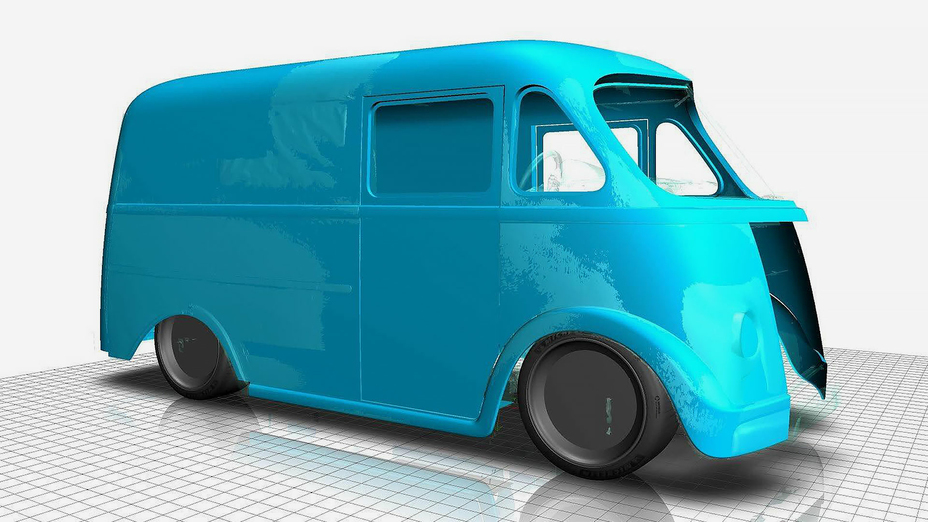
Autodesk Aliasソフトウェア上の3Dスキャンデータ(水色部分)とCADデータ(青色部分)
ステージ5:シャシーのモデリング
フォワードは、シャシーやその他すべての技術的なパーツのモデリングにはSOLIDWORKSを使用した。フォワードは同じワークフローに沿って、LeoでキャプチャしたスキャンデータをSOLIDWORKSへアップロードし、それを利用して新しいパーツのモデリングを行った。フォワードは、車両内部の部品の正確な3Dレプリカを自身の設計過程において正確な参照用に利用し、また、生じる可能性のある問題点をより明確な形で把握する際にも役立てた。設計を進める上で、フォワードは更に多くの部品をスキャンし、参照モデルとしてソフトに追加した。
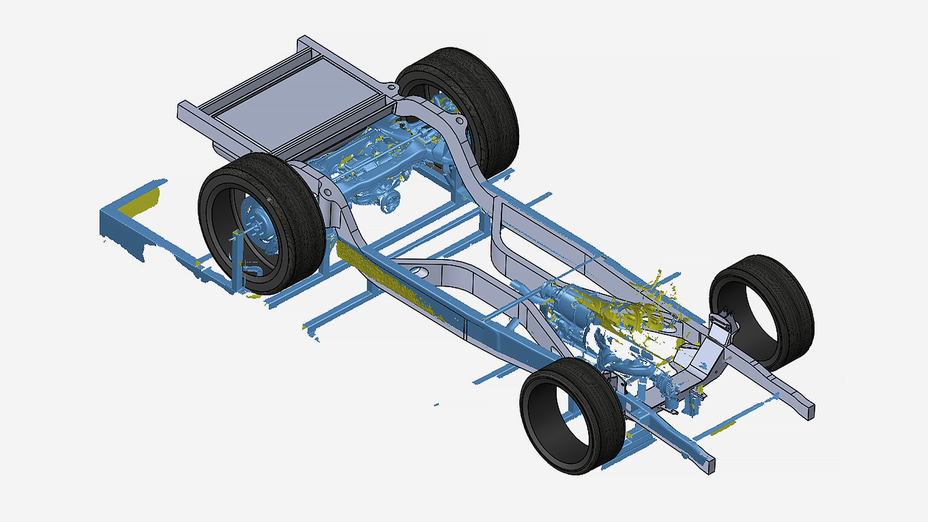
フォワードはSOLIDWORKS上でCADモデルを作成するため、シャシーのスキャンデータをプラットフォームとしてモデル化するために使用した
ステップ6:新しい部品のレーザーによる切断及び溶接
SOLIDWORKSでの作業の後、フォワードはすべてのCAD生成物をレーザーによる切断と、その後のシャシーへの溶接作業のために送付した。
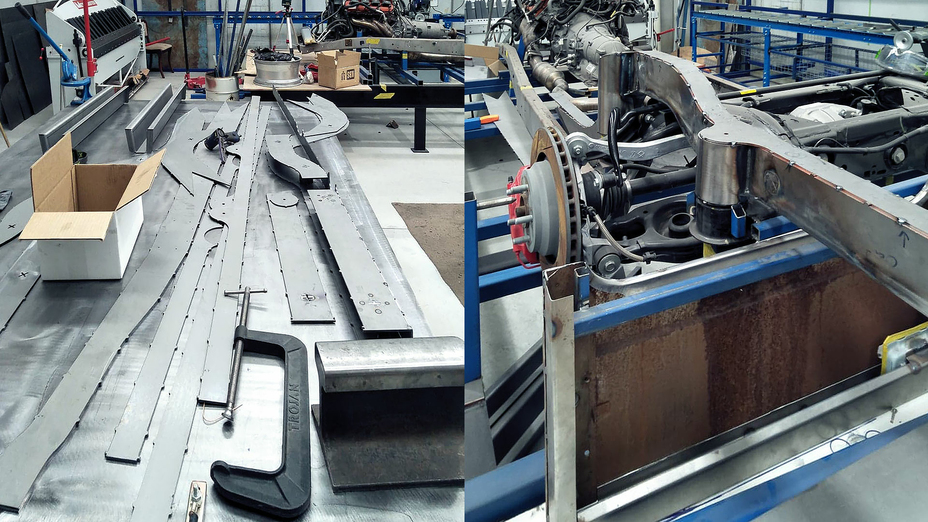
シャシーへの最終段階の溶接前の、簡易的に組み合わされたレーザー切断済の平坦なパーツ(画像提供:streetmachine.com.au)
すべての部品をシャシーへ溶接した後、車両内部の全体の型はヘルキャットの標準搭載の部品すべての取り付けのため、自動車電気工へ送付された。この間、フォワードはパネルの製作や適合性の試験に使用できる自動車のボディバック(body buck)の製作を行うため、スキャンデータ(ステップ4参照)からモデル化した車体のサーフェスを分割する準備に取り掛かった。
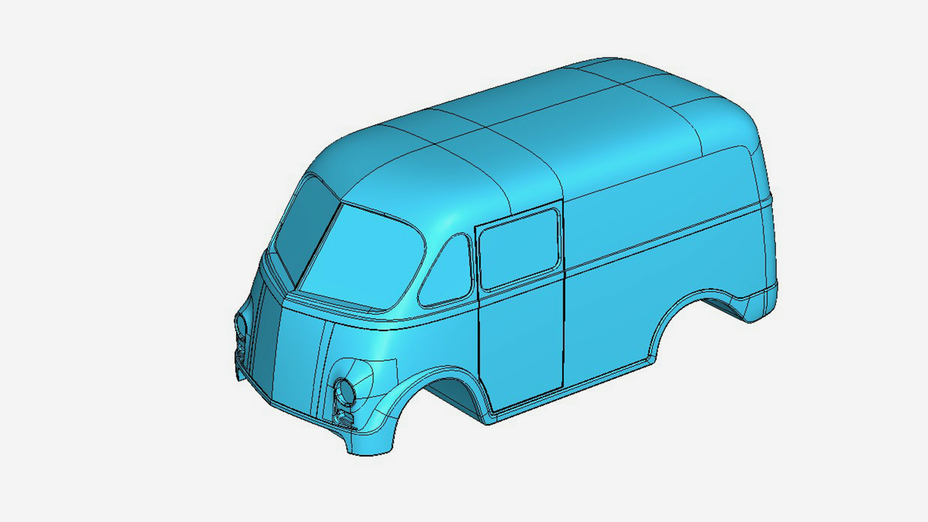
フォワードがボディバックの製作に使用する、新しい車体の型の完成デザイン
製作チームは、車体製作の全作業を一年以内に完了し、さらなる二,三ヵ月を費やして、内装や塗装、その他の小規模の作業を二〇二三年末までに済ませる予定である。完成した暁には、フォワードは、このプロジェクトが他のスタジオや取引先を教育するための良いプラットフォームになれば、と願っている。
「メトロバンは、私の考える車両の再製作の理想の形を体現したものの一つとなる」と、フォワードは語る。「我々のプロセスは時間が掛かるが、古い車両をそのまま改修するのは3Dスキャンデータを用いて始めから製作するよりも時間が掛かる。三次元で情報をキャプチャし、そのデータを基に部品のリバースエンジニアリング及び製作を行うことができることこそ、私がこのビジネスを立ち上げた基本的な理由である」
「HDモードには、入手可能になってすぐ、その凄さに圧倒された。まるで、新しいスキャナを買ったようだった」
フォワードは3Dスキャニングに舵を切ってから、振り返ることはなかった。手作業で計測する代わりに、自動車パーツの正確なデジタルコピーを作成可能であることは、業務過程、収集データの精度、そして生産性全体に大変革をもたらした。
その上、状況は良くなるばかりだ。「Artec社のワークフローや、同社が常に最先端であることを維持するために行っている継続的なアップグレードには、いつも感心させられる」と、フォワードは語る。「製品がアップグレードされる度に、興奮の度合いが上がるようだ。Artec Studio 15と16の違いは並外れていた。HDモードには、入手可能になってすぐ、その凄さに圧倒された。まるで、新しいスキャナを買ったようだった」