Breakthrough AI trained with Artec Leo 3D scanning to predict bridge capacity
Challenge: Easing the load on local authorities across the USA, each charged with maintaining thousands of bridges to budget, and minimizing costly closures caused by safety concerns.
Solution: Artec Leo, Artec Studio, ABAQUS, in-house AI algorithms
Result: Bridge beam datasets indicating corrosion levels with such high accuracy, they can be fed into a novel AI that works out capacity, and flags the repairs needed to avoid failures.
Why Artec 3D?: Featuring a built-in display and full wireless functionality, Artec Leo captures infrastructure with unmatched flexibility, speed, and accuracy for rapid, reliable analysis.
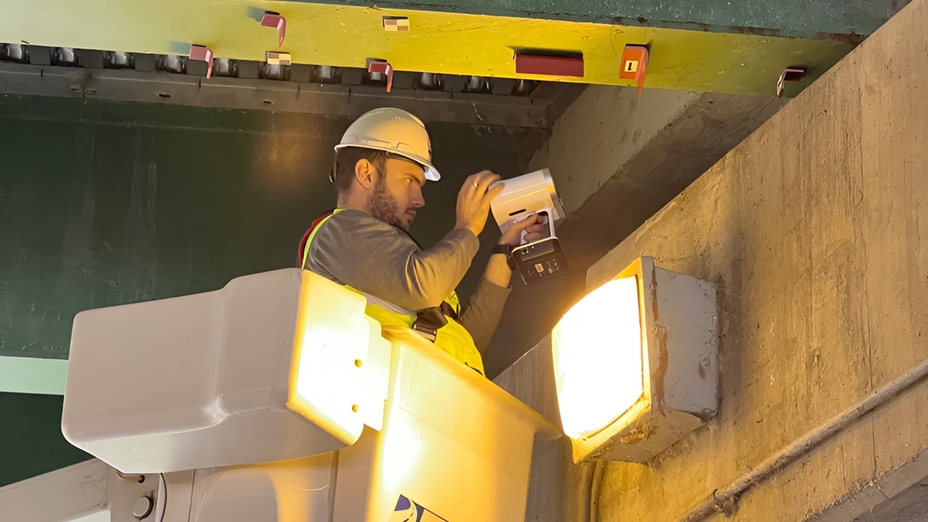
The Artec Leo 3D scanner being used to digitize beams underneath a bridge
In everyday life, saying an object is ‘as tough as steel’ is a way of emphasizing its durability. After all, the material is one of the strongest on the planet. But even steel has its limits.
Many public bridges, for example, are upheld by steel beams prone to deterioration triggered by extreme weather conditions. With failures having previously caused numerous injuries and fatalities, as well as significant financial loss, around the world, regular inspection is vital to ensuring that these remain safe to operate at full capacity.
In cases where bridges are found to be deteriorating, their load limit can be lowered, and in certain circumstances, they may even face closure – at a huge economic cost.
As you can imagine, authorities manage infrastructure in towns and cities with thousands of bridges, as well as being responsible for providing other public services. This balancing act also makes efficiency essential to stretching resources as far as they’ll go.
That’s why researchers at Technische Universität Dresden and the University of Massachusetts Amherst have begun developing a faster, more accurate steel bridge inspection method.

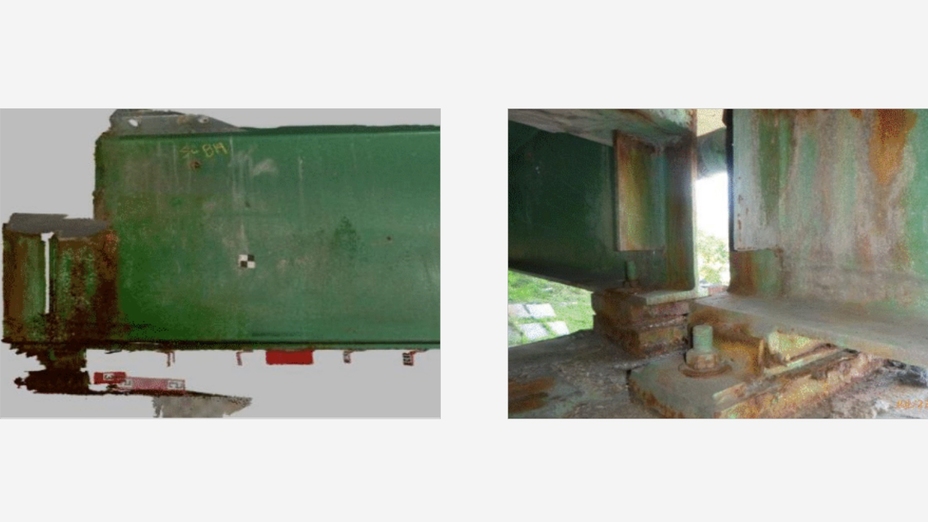
Steel bridge girders showing signs of deterioration (reflected in the captured 3D scan data)
Currently, scrutinizing such infrastructure involves removing corroded material and measuring what’s left, using time and labor-intensive ultrasound single-point capture. With Artec Leo, on the other hand, researchers have now identified a far more efficient way of measuring beams and acquiring the highly detailed data needed for faster, deeper analysis.
Leo’s efficiency “in another universe”
Initially, the researchers developed their workflow around data captured with a terrestrial laser scanner. The University of Massachusetts Amherst is home to a Digital Media Lab 3D Innovation Center filled with advanced technologies, including a tripod-mounted device, which had previously been used to digitize and research open landscapes like river banks.
When it came to identifying corrosion patterns on a decommissioned steel girder, this LiDAR scanner was also found to capture sufficient detail. However, in real-life bridge inspection, beams need to be measured at either end, in areas requiring a bucket crane to access.
Targeting greater flexibility, the team switched to Artec Leo, a wireless, all-in-one device with 0.1 mm accuracy and a capture speed of up to 35 million pts/s. Supplied by Artec 3D Ambassador Source Graphics, Leo is not just fast and compact, it’s incredibly intuitive, making it easy to learn how to use, even for relative newcomers requiring high precision from the outset.
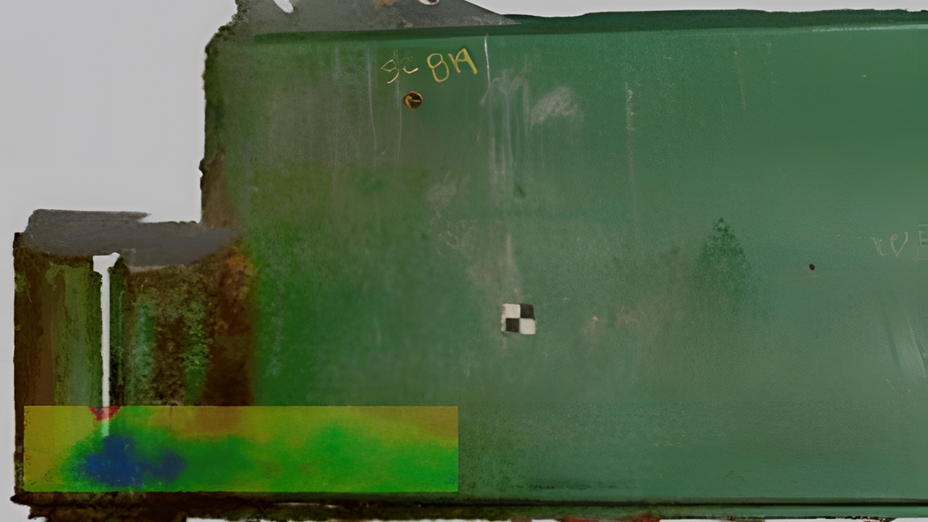
Beam deviation and remaining thickness analysis carried out on a naturally corroded bridge beam using Artec Leo 3D scan data
“Usually corrosion happens to beams – the support structures of the bridge deck. Because of the deck of the bridge, you have to scan one side, stop, move the bucket, then scan the other,” said Simos Gerasimidis, Associate Professor at the University of Massachusetts Amherst. “So being handheld, versatile, and easy to move around is very important. Leo also tells you if you’re too close or too far away, so you know on the spot if the scan was good or not.”
“With Leo, you’re gathering (at least) hundreds of thousands of points in five minutes. Using traditional methods, you capture one point in three minutes. So, if you measure efficiency by time per data captured, it’s in a different universe.”
Predictive inspection with AI
Having mastered Leo 3D scanning, Gerasimidis and his colleagues turned to honing their workflow. Processing began inside Artec Studio, Artec 3D’s scan capture and processing software, featuring HD Mode for ultra-sharp scans – even when digitizing shiny metal surfaces – and unique algorithms that allow for best-in-class texture and geometry tracking.
Beam analysis would also be possible using the program’s built-in inspection tools, but the team opted to work with raw point clouds instead, to avoid any chance of misalignment.
During data tidy-up, they generated 2D contour maps, which illustrated the remaining thickness of each girder’s ‘web plate’ (or steel panel). On their own, these maps offer inspectors a quick and easy way of visualizing a beam’s condition. But the researchers weren’t done there – they wanted to develop a way of using this data to uncover bridge capacity.
So, once they’d placed data into a coordinate system, the team fed it into the ABAQUS finite element analysis (FEA) software for structural analysis. After repeating this process with multiple scans of three decommissioned beams, they used their combined FEA findings to computationally generate ‘scenarios’ in which overloading would lead to failure.
“For each of the 1,400 corrosion scenarios created, we used an in-house developed algorithmic framework to generate a finite element model,” explained TU Dresden researcher George Tzortzinis. “From there, we could identify the capacity and exact failure mode of the corroded beam.”

A complete girder 3D scan, including small holes and fine surface details
Aiming to further accelerate bridge analysis, the team then used these scenarios to train an AI capable of finding patterns between input data using machine learning, and calculating capacity. The idea being that if load rating engineers fed contour maps captured with 3D scanning into this AI tool, they could automatically assess a beam’s ability to carry predetermined loads.
After demonstrating this approach in a controlled environment, the team went on to apply it in practice, with the inspection of an in-service bridge in Massachusetts. Despite vibrations and accessibility restrictions, they managed to quickly and efficiently identify areas of wear in similar areas across beams and generate the data needed for engineers to assign bridge load ratings with much greater accuracy.
Where next for AI-powered inspection?
Like conventional bridge inspection methods, the researchers’ requires crane rental and partial road closures, but it’s also faster and significantly reduces inspection uncertainty. With over 20,000 US steel bridges rated as being in ‘poor’ condition, and more than 100,000 rated ‘fair,’ it’s believed that their more efficient approach could help the Federal Highway Administration and state transport authorities address an estimated $125 billion repair backlog.
Moving forward, the team proposes that their findings be rolled into a comprehensive data collection training course, which brings uniformity to the industry. In the longer term, they believe integrating AI-powered load rating and section loss comparison tools into bridge management systems could also enhance public infrastructure maintenance across the US.
“There are several US states considering integrating 3D scanning into their workflow – some already have Artec Leos,” concluded Gerasimidis. “This is a slow-changing industry, people need to see proof, and now we have it. I think the technology will continue to grow here. It might not happen in six months, but over a 5-10 year scale, things are going to change.”
Interested in finding out more about this pioneering research? You can read the full paper here.
Scanners behind the story
Try out the world's leading handheld 3D scanners.