Artec Eva digitizes 500 years of history from one of the world’s oldest synagogues
Challenge: To create an ultra-high-quality 3D scan of one of the world’s oldest synagogue arks, the Mantua Ark, for an interactive 3D visitor kiosk and virtual web exhibition of the Nahon Museum of Italian Jewish Art in Jerusalem.
Solution: Artec Eva, Artec Studio, Autodesk Memento, Atangeo Balancer, Meshlab, Adobe Photoshop
Results: An excellent, highly detailed, and interactive 3D model created with Artec Eva that is now available for exploration and a closer look for the museum’s visitors online and in person.
The Holy Torah Ark of Mantua is one of the rarest and most impressive exhibits at the Nahon Museum of Italian Jewish Art in Jerusalem. Designed to house the holy Torah scrolls and created by the finest craftsmen of Mantua, Italy in 1543, this unique wooden ark decorated with the original gilded carving is one of the oldest in the world. Its style echoes that of the biblical Holy Temple in Jerusalem, which is believed to have housed the Ark of the Covenant. It was designed in the shape of a building and features architectural elements such as columns and capitals.
From the time of its construction to the present day, the Mantua Ark has undergone multiple incarnations. Finally, after World War II, with a declining Jewish community, the ark was shipped to Jerusalem and placed in its present abode. Once there, it underwent extensive renovation, preservation, and restoration, all of which brought it back to its wonderful present condition.
For an ordinary visitor to the museum as well as visitors to the museum’s website, however, the ark’s special history in regards to its symbolism and features remains unknown. Its size and position prevents close inspection and even the features which are visible cannot be fully appreciated.
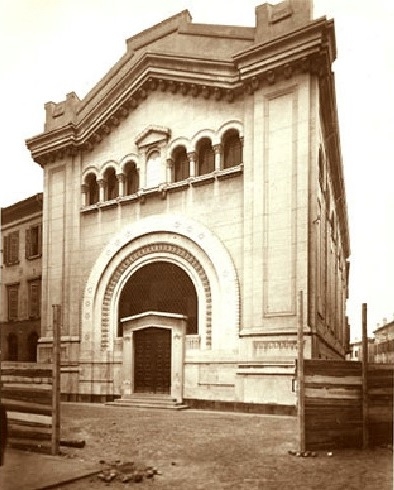
The Scola Grande synagogue in Mantua, where the ark was originally located.
A photo made in the early 20th century, courtesy of the Nahon Museum.
In 2015, the Nahon Museum initiated a project designed to tell the story of the ark, its journey, and its historic meaning in the context of Jewish Italian life. The website Mantua in Jerusalem outlines the history, life, and culture of the Mantua Jewish community and the importance the ark held to its people, generation after generation.
It was for this reason that the museum chose to embark on an ambitious endeavor – to 3D scan the ark and make it fully accessible to visitors, both in person and virtual.
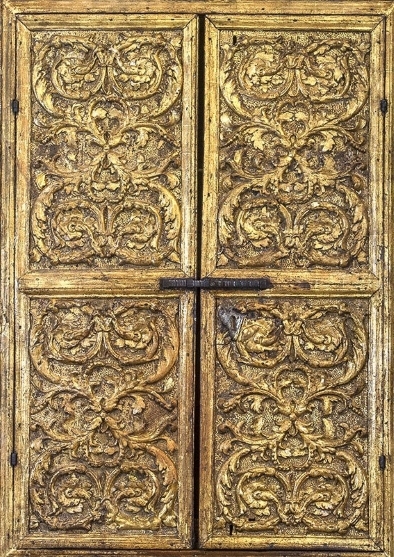
The shiny, symmetrical, and repetitive patterns of the ark [Image by Professor Moshe Caine]
Due to its size, geometry, and the complexity of its texture, the scanning of the Mantua Ark posed certain challenges:
- The topography of the ark – extremely complex, with numerous areas without direct visual access. In addition, the ark stands so close to museum walls it left very little room for the scanning equipment to work, as well as operating the scanner at the angles required to reach the blocked surfaces.
- The texture. The ark was initially made of wood. However, its entire surface is coated in a gold leaf, which is smooth and shiny – one of the most hard-to-capture surfaces for any 3D scanner. When it came time to do the scanning, it was neither permitted nor practical to coat the surface with matte powder. Even if it were, it would have altered the surface quality of the ark.
- Thirdly, while the topography of the ark is complex, the texture is very symmetrical and the pattern is repetitive, which somewhat complicated aligning and fusing the multiple scans.
- And finally, the size of the ark (over 3 meters high) made the scanning process all the more challenging.
After assessing the complexity of the job, it became clear that the highest-quality tool is needed to digitize the ark, and the museum turned to Caliber Engineering and Computers Ltd, Artec 3D’s Gold Certified Partner in Tel Aviv. Zvi Grinberg, head of Caliber at the time, was immediately brought into the project. Being so different from the technical engineering CAD projects his company usually undertook, he recognized both the professional challenge and the unique cultural value of this project, which he volunteered to take on at no cost.
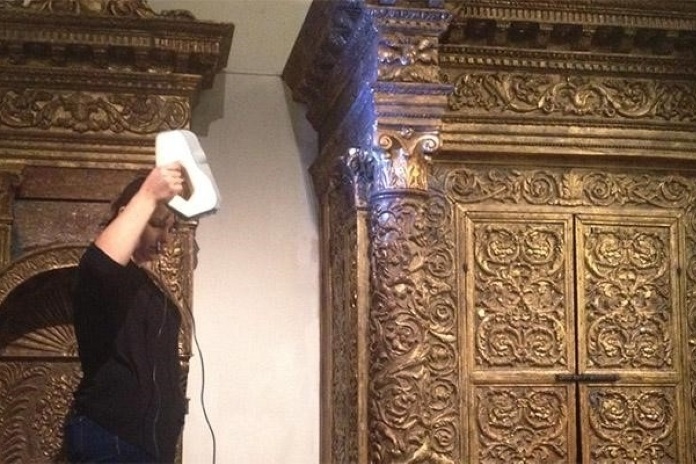
Scanning of the ark with an Artec Eva scanner [Image courtesy of the Nahon Museum]
After a thorough examination of the ark, the Caliber team decided Artec Eva was the most suitable scanner for the job. Called “a monster among handheld scanners,” this structured-light 3D scanner excels at capturing medium-to-large objects with an outstanding accuracy of up to 0.1 mm and exceptional resolution, even for black and shiny surfaces, which gives it an edge over other scanning solutions on the market. Plus, it is lightweight and fast, which makes it especially helpful when capturing diverse historical pieces, sculptures, and monuments in far-from-ideal scanning environments, whether on a sunny day outside or deep within a dimly lit gallery.
Scanning process
To capture the ark from the ground up and give the scanning team easy access to the top of the object, special scaffolding was built in the museum. Normally used for medium-sized objects, it was a personal challenge for Eva to capture such a large object. It took 15 hours over three days for the team to complete the scanning, followed by several more to align, clean, and fuse the multiple scans together. Overall, 78 separate scans were made. The final model was over 700 MB and contained over 16 million polygons.
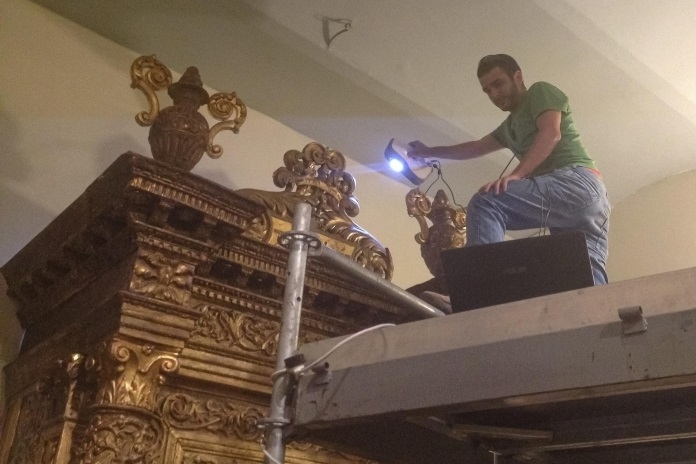
Scanning of the ark from above [Image courtesy of the Nahon Museum]
“Despite the ark’s large size, we’ve managed to get good results with Artec Eva right from the first attempt thanks to the texture and geometry of the ark. After the scan, we were able to finish all the work at the office using Artec Studio software, with no need to come back for additional scans and repair,” said Guy Engel, CEO of Caliber Engineering.
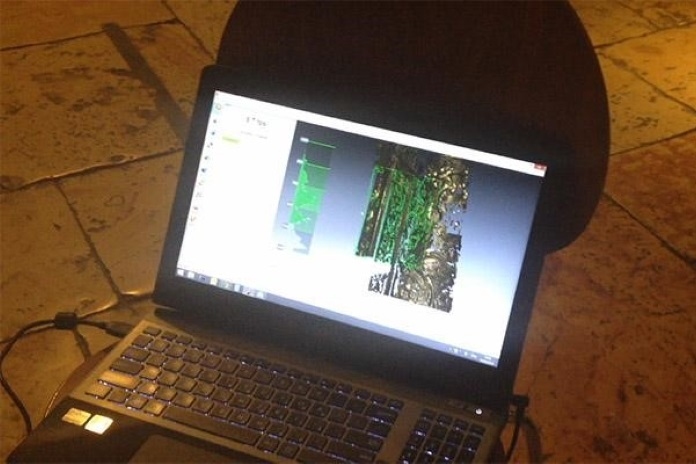
Previewing the results in Artec Studio [Image courtesy of the Nahon Museum]
After the initial processing stage, the Caliber team reduced the size of the file while maintaining the quality of the original scans, and touched up the 3D model to prepare it for public display. At this point, the file was passed on from Caliber to the Department of Photographic Communication at the Hadassah Academic College in Jerusalem, to Associate Professor Moshe Caine specifically. Having extensive knowledge and experience in 3D scanning and photogrammetry solutions for cultural heritage preservation, Professor Caine polished the 3D model of the ark to the peak of perfection.
Data processing workflow of Professor Caine
Professor Caine’s scan processing workflow went as follows:
Fine-tuning and cleaning minor defects of the mesh using Autodesk (beta) Memento Software.
Adding in a back wall and floor. Because the ark was mounted to the museum wall, it was impossible to scan the back and underside of the ark. Rather than construct a false rendition of them, it was decided to computer generate a simple wall and floor and add them to the model.
Image processing of the texture map. Despite the meticulous work during the scanning stage, small defects still remained, as well as an inaccurate color rendition of the ark. Additional photography was subsequently carried out using a DSLR Nikon camera, and the corrected surfaces were fused into the original UV map. Various methods were tested for this purpose, including:
- Parameterization and texturing from rasters in Meshlab.
- Exporting the map as a PSD (Photoshop) file, correcting in Photoshop, reimporting to and then exporting the corrected model.
- Opening the OBJ file in Photoshop and working directly on the texture layer. Ultimately, a combination of the above techniques was employed until satisfactory results were achieved.
- Color correction was carried out on the final texture map with Photoshop software, using the actual ark as the sole reference.
After scanning dozens of historical pieces, Professor Caine elaborated on his approach to the 3D scanning and processing workflow:
“One major piece of advice (for those planning to 3D scan cultural heritage) is this: work slowly and carefully. Don’t hurry. Move in as close as possible to the object. Use lots of soft light. And remember the saying: ‘Garbage in… garbage out.’ The result will only be as good as the work and care that goes into it.”
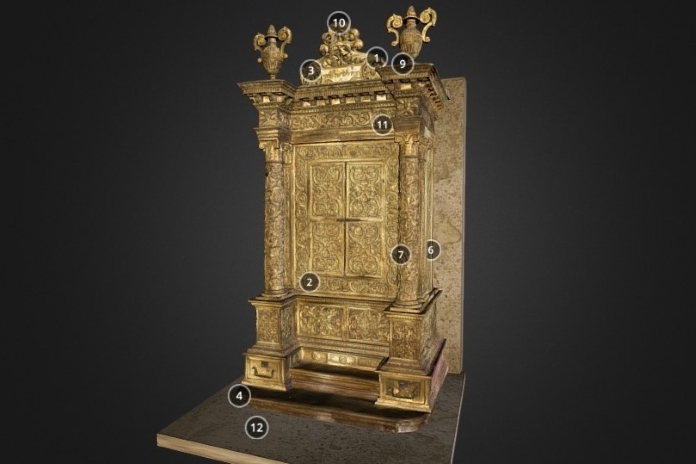
The Mantua Ark, by Caliber & Professor Caine on Sketchfab
When Professor Caine finished his meticulous scan processing, the final model was uploaded for public viewing to the Nahon Museum website Mantua in Jerusalem, dedicated to the art of Mantua’s Jewish community. In addition, an onsite kiosk with a touchscreen was installed next to the ark, making it possible for museum visitors to view the magnificent historical showpiece from all angles, zoom in and out to examine every detail, and most importantly, to have immediate access via hotspots to the relevant information for various aspects of the historic artifact.
The overall response to the model has been very positive and enthusiastic. According to the museum’s personnel and Professor Caine, people particularly appreciate the ability to explore the ark up close and from all angles. This is the magic of 3D models, which 2D images or even physical objects as large as the Mantua Ark normally cannot compete with. Projects such as this are an amazing example of how 3D scanning technologies transform the way we perceive and can preserve cultural heritage.
Back in the 1500s, the citizens and members of Mantua’s Jewish community couldn’t even imagine that their descendants would one day not merely be able to see their community’s signature artifact all in one piece, even after 500 years, but also be able to explore it up close in 360 degrees without even leaving their homes.
Scanners behind the story
Try out the world's leading handheld 3D scanners.