Creating a one-of-a-kind prosthesis with Artec Eva and Geomagic Freeform
Challenge: When a German prosthetics firm needed to create a unique lower-leg prosthesis for their patient, they understood that traditional tools and methods wouldn’t be up to the task, so they reached for their 3D scanner.
Solution: Artec Eva, Artec Studio, Geomagic Freeform
Results: A distinctly original prosthetic leg, designed for daily use, and also equipped for swimming or bathing. Digitally sculpted in Geomagic Freeform, the special prosthesis fulfilled the wishes of the patient, whose lifelong love of diving brought about the request.
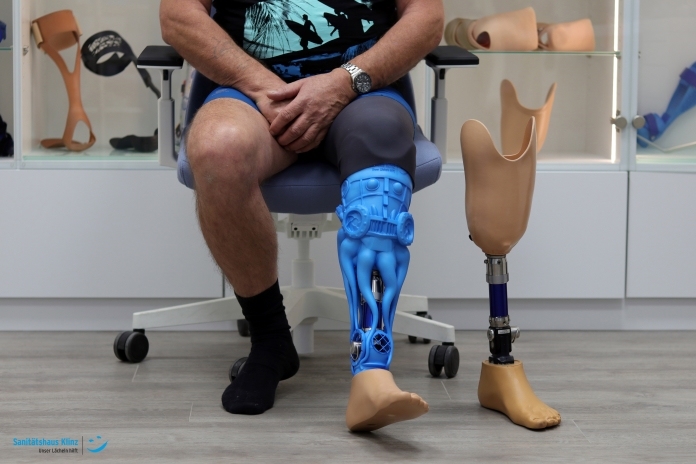
The patient with his new and old Sanitätshaus Klinz prostheses
One brisk morning in central Germany, Wolfgang K. climbed up into his delivery truck and set off on a new route, one that would prove to be the last of his career. His first stop was a hardware store, where he unloaded his shipment and waited for a forklift to carry the boxes away. Then tragedy struck.
Wolfgang was looking the other way when the forklift crashed into him, shattering his foot and knocking him to the ground. All he remembers from that moment is what felt like a slap on the back; then he blacked out. Sometime later, he awoke in unbearable pain, with paramedics around him, and was told about the massive damage to his foot and ankle.
The hospital treated and stabilized the immediate injury, but in the weeks and months ahead, the inflammation grew worse. Wolfgang begged his doctors to amputate his foot, but they weren’t giving up so easily. They did everything in their power to save it, for three years, until the inflammation had spread up his leg, triggering extensive tissue necrosis.
Wolfgang’s doctors were finally forced to amputate his leg below the knee. In the weeks following, after the swelling in the remainder of his leg (his residual limb) went down, Wolfgang was fitted with a transitional prosthesis. Around that time, he saw an advertisement for the Sanitätshaus Klinz orthopedics clinic of Bernburg, Germany, and soon after, he became their patient.
The staggering worldwide demand for prosthetics
With more than 185,000 lower limb amputations every year in the US alone, and over 1 million carried out worldwide, prosthetics specialists have struggled to keep up with the rising demand for their services.
The traditional method of creating prosthetic sockets, the part of the device that interfaces with the patient’s residual limb, involves plaster casting, hours of work, along with ample finesse and experience.
Although the specialists at Sanitätshaus Klinz still employ plaster casting and other analog methods in their work, for the most challenging of projects, especially those impossible to accomplish via traditional tools, they frequently turn to their 3D scanner Artec Eva.
A professional handheld 3D scanner that’s been a leading favorite among healthcare practitioners and thousands of others around the globe, the Artec Eva quickly delivers color 3D scans with a level of accuracy down below a millimeter, making it ideal for capturing the organic surface measurements of patients’ residual limbs and other body parts.
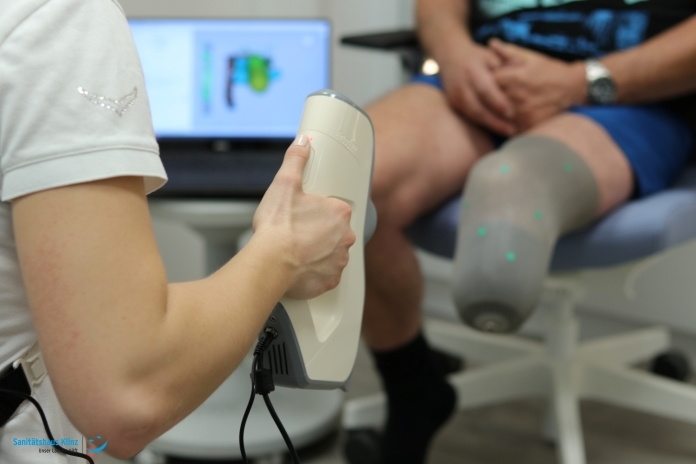
3D scanning the patient’s residual limb with Artec Eva and Artec Studio software
They also make use of the Artec Space Spider, for projects with intricate details that demand the utmost in precision. Originally developed for use on the International Space Station, the Space Spider is a popular choice among designers, engineers, and researchers in many diverse fields.
Dreaming up an entirely new prosthesis design
After having several prostheses since becoming a patient at Sanitätshaus Klinz, it came time for Wolfgang to get a new bath prosthesis, one that could be used in the shower or while swimming.
It would need to be both waterproof and corrosion-resistant, even in salt water environments. When Sanitätshaus Klinz’s biomedical engineer Lisa Pabst saw his request, she decided to offer him something even better.
From their discussion together, Pabst understood that Wolfgang’s great passion was diving. So, she, along with Wolfgang and her colleague master orthopedic technician Carsten Suhle, came up with the idea to create a unique bath prosthesis with a maritime design that wouldn’t merely be cosmetic, but rather to have the prosthesis itself be a one-of-a-kind, maritime-themed design object.
Even after losing his leg, Wolfgang had never abandoned his love for diving and the water. Once he heard Pabst’s idea, he enthusiastically gave her the green light.
Pabst spoke about the challenge of the project: “We wanted to pursue a different approach, to see whether it would be possible for us to integrate a prosthesis into our new design rather than adapting the design to an existing prosthesis.”
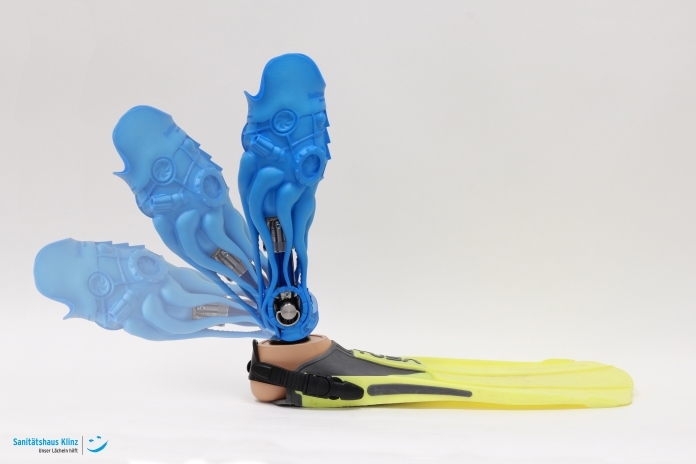
The new design, showing its ability to angle the prosthetic foot, for attaching a swimming flipper
Their goal was to combine all the water-resistant durability of a bath prosthesis with the esthetics of a cosmetic prosthesis, so when it’s being worn under long pants, no one can tell that there’s a prosthetic limb underneath. All the cosmetic elements of the prosthesis would need to cover and protect the mechanical components of the device.
Regarding the inspiration for the design, Pabst said, “We came up with the idea of using an octopus. The body of the octopus covers the upper part of the prosthesis, while the tentacles mimic the shape of the lower leg. A nostalgic diving helmet, entwined in tentacles, was added at the ankle. The ankle joint can be operated via the side openings of the helmet.”
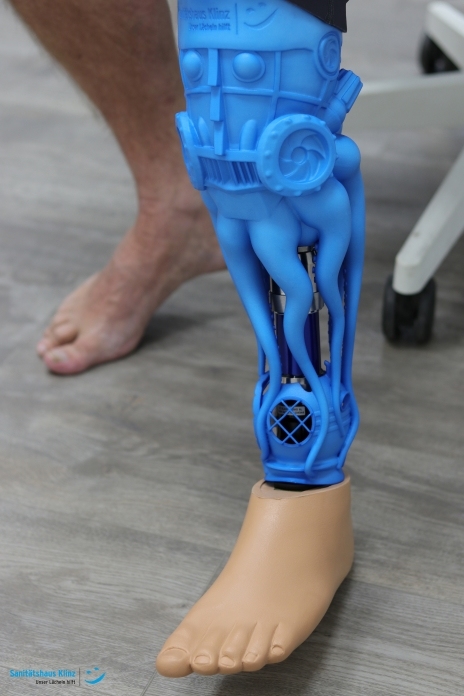
The new bath prosthesis in use by the patient
At the same time, Pabst and her team understand that the most vital part of any new prosthesis is the shape and fit of its socket, with a design that’s unique to each individual patient, where even a mildly incorrect fit can often result in patient discomfort and biomechanical dysfunction leading to future injury.
At worst, an ill-fitting socket can cause a patient to suffer skin ulcers, impaired balance, falls, chronic musculoskeletal overuse injuries, osteoarthritis, and more.
To help achieve a seamless fit for the new socket, they turned to their Artec Eva, which Pabst used to scan all of the surface geometry of Wolfgang’s residual limb in less than a minute. Pabst also scanned his other leg, in order to use its precise volumetric and surface measurements for creating the shape and dimensions of the new bath prosthesis.
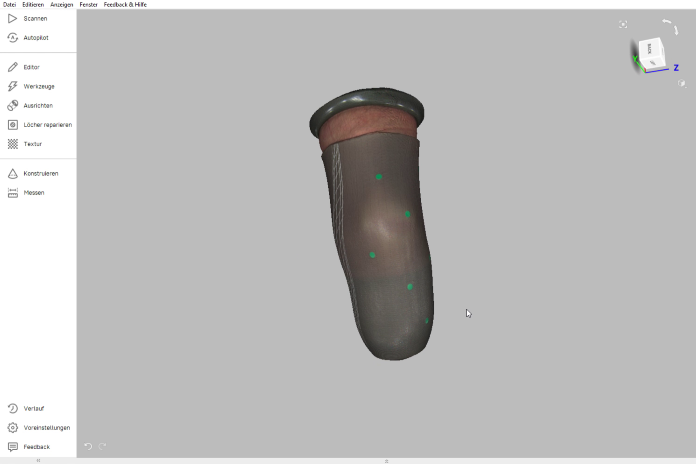
Artec Studio screenshot: an Eva scan of the patient’s residual limb
Right after the scanning session, prior to exporting the 3D meshes to Geomagic Freeform, the scans were processed in Artec Studio software. Using the intuitive tools within the software, Pabst deleted any unwanted data, including the floor and other objects around.
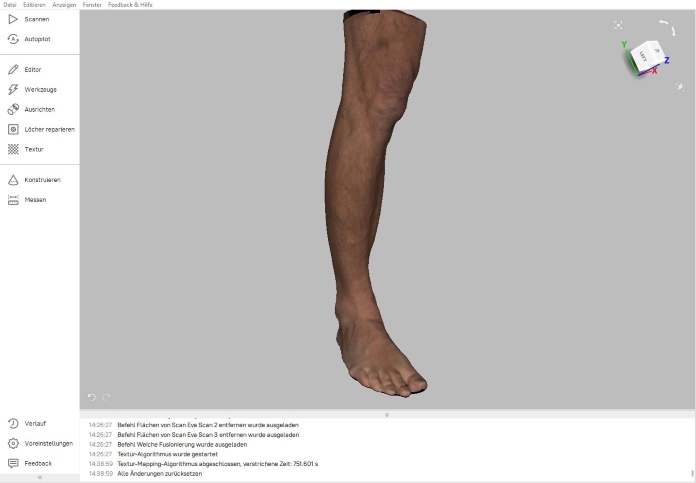
Artec Studio screenshot: an Eva scan of the patient’s contralateral leg
The scans were aligned and registered, then merged together into one object. Finally, the texture was brought in and applied to the mesh. In Freeform, Pabst designed the prosthetic socket and sculpted the cosmetic elements of the design to life.
Pabst commented on how instrumental their Eva has been, in synergy with Freeform: “When I import an Eva scan into Freeform, I’m starting off with a dependable foundation for my prosthetic design work. It takes only seconds for Eva to capture the exact measurements of a patient’s body, and in Freeform, I build my new designs based on these same dimensions.”
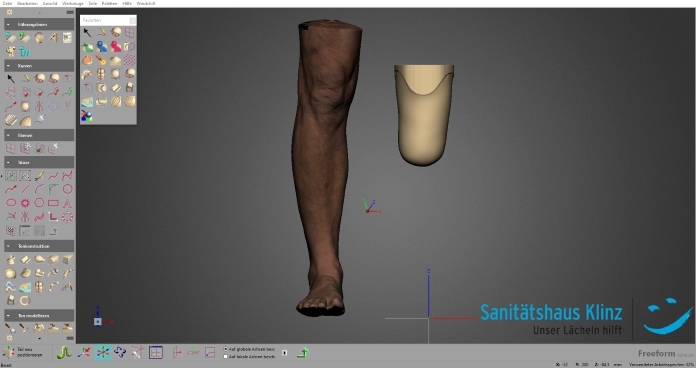
Geomagic Freeform screenshot: an Eva scan of the patient’s contralateral leg & an Eva-scan-based model of his residual leg
Pabst continued, “Particularly when creating a new prosthetic socket, which must perfectly embrace and support the unique shape of a patient’s residual limb, every millimeter of surface should be digitally captured and brought into the design. Fortunately, the Eva does this quickly and easily.”
Her workflow included the following steps: after importing and arranging the meshes in Freeform, she modeled Wolfgang’s residual limb. Then, before moving on to the subsequent steps, she mirrored his contralateral leg in Freeform. From there, she built up the prosthetic shaft, shaping it to the adapter and preparing the design for the functional elements.
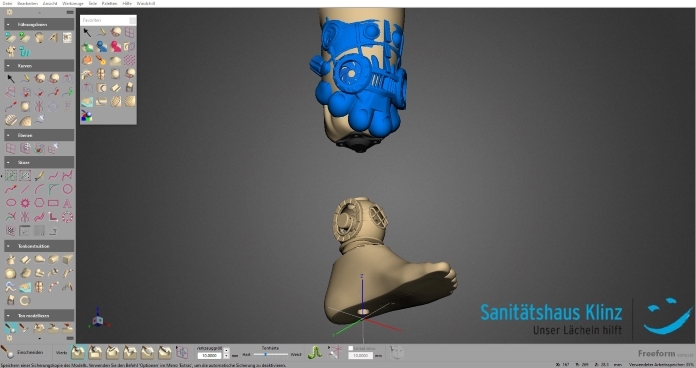
Geomagic Freeform screenshot: Shaping the shaft to the adapter, and adapting the design to the prosthesis’ functional elements
Pabst then shaped the outer dimensions of the tentacles in accordance with the exact measurements of Wolfgang’s other leg, to achieve the same overall circumference of the lower leg.
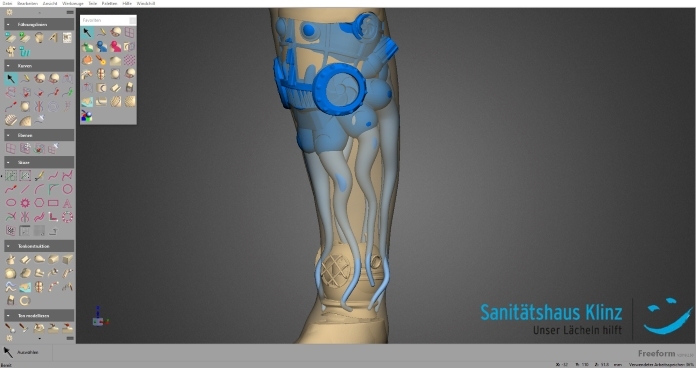
Geomagic Freeform screenshot: Shaping the dimensions of the tentacles using the Eva scan measurements of the contralateral leg
At this point, Pabst created the tentacles’ suction cups, then connected the shaft, octopus, tentacles, and diving helmet. After several other steps, she embossed the design with the Klinz logo and the patient’s name.
After 3D printing the exterior components of the new prosthesis, they were merged with the mechanical elements of the device and locked into place. That’s when Wolfgang was invited to the clinic for his fitting.
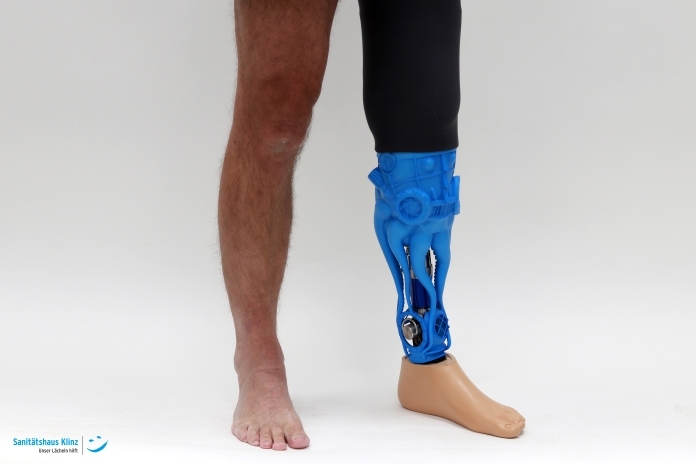
Standing proudly: the new bath prosthesis in place and ready for use
From the moment he caught sight of his new leg, he’s been very happy with it, while the fit is as comfortable as he has come to expect from using his other Klinz prosthetic devices. His wife and daughters are delighted with it as well. On a recent vacation to the Baltic Sea, children wandered over to get a closer look and admire his amazing leg.
The power and potential of 3D scanning in O&P
Pabst commented on the pivotal role that 3D scanning has gained in modern orthotics and prosthetics design, “Whenever you need to create an orthosis, or an upper- or lower-body prosthesis, with high-tech or low-tech materials, first you absolutely must have accurate measurements of the patient’s body where the new device will connect.”
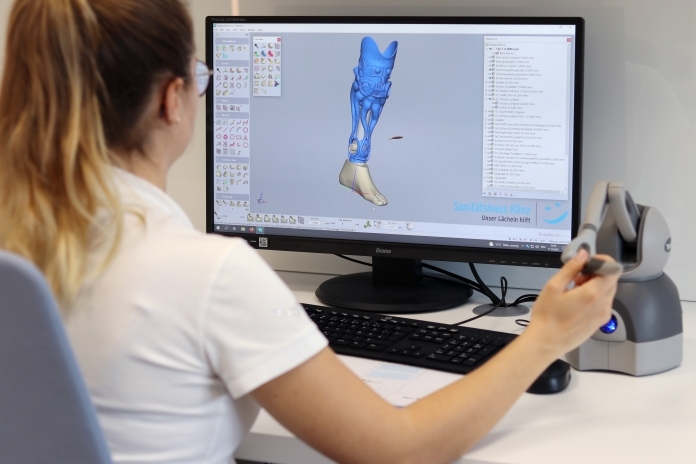
Using a haptic device with Geomagic Freeform to put the finishing touches on the new bath prosthesis
She explained further, “Without this foundation to build on, eventually serious problems will arise, from the fit of the device, to the patient’s physical responses to it, etc. By starting off with Artec scans, every device we produce looks exactly like the other side and a natural extension of their own body. The difference this has made in our work is truly significant.”
Scanners behind the story
Try out the world's leading handheld 3D scanners.